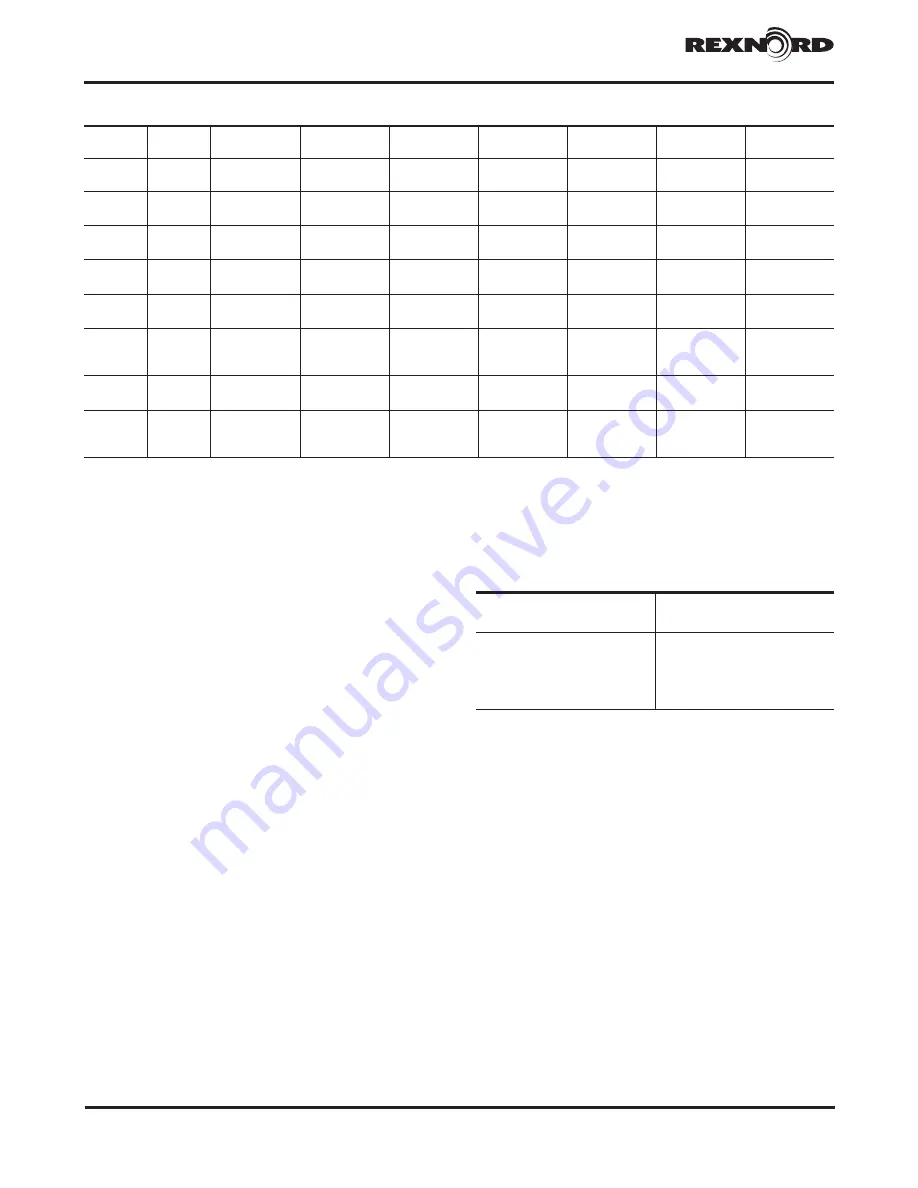
Falk
®
CT-Series Gear Drives • Operation and Maintenance
(Page 6 of 7)
Sizes 2160 thru 2400
GR3-014
Rexnord
January 2017
3001 W. Canal St., Milwaukee, WI 53208-4200 USA
NEW
Telephone: 414-937-4359 Fax: 414-937-4359 www.rexnord.com
8. MAINTENANCE
8.1 OIL CHANGE
The first oil change after about 200 working hours.
Subsequent oil changes must be made after every
1500 to 5000 operating hours, depending on working
conditions. The oil change intervals should, however,
not exceed 18 months.
If possible, the oil should be drained warm.
Where the gear unit has to be stored for a long time,
consult us in advance for advice and to enable us to
give a special treatment before dispatch, for storing
the gear unit for a longer time. As an alternative to the
oil- change intervals indicated in Table 1 (see item 8.5)
it is possible to have the oil sample tested at regular
intervals by the Technical Service of the relevant oil
company and to have it released for further use.
If re-usability has been confirmed, no oil change will
be necessary.
Drain the oil while the gear unit is still warm, i.e.
immediately after shutting down the machinery. When
changing the oil, always re-fill the gear unit with the
same type of oil. Never mix different types of oil and/
or oils made by different manufacturers. Polyglycol-
based synthetic oils in particular must not be mixed
with PAO-based synthetic oils or mineral oils. If
changing to a different grade or make of oil, the gear
unit must, if necessary, be flushed out with the new oil
grade. Flushing is not necessary, if the new service
oil is fully compatible with the old service oil in all
respects. Compatibility must be confirmed by the oil
supplier. If there is a change to another oil grade or
make, Rexnord recommends flushing out the gear unit
with the new grade of service oil.
When changing the oil, the housing and the oil-
supply system, if available, must be flushed with oil to
remove sludge, metal particles and oil residue. Use
the same type of oil as is used for normal operation.
High-viscosity oils must be heated beforehand using
suitable means. Ensure that all residues have been
removed before filling with fresh oil.
For oil renewal period refer to Table 1 based on the
operating temperature.
Place a suitable container under the oil-draining point
of the gear-unit housing.
Unscrew the breather plug including reducing screw
at the housing top.
Unscrew the screw plug or the open oil-drain cock and
drain the oil into the collecting container.
Drain the oil from the oil-supply system (see operating
instructions to the oil-supply system).
There is a danger of scalding from the hot oil
emerging from the housing. Wear safety gloves and
safety glasses! Remove any oil spillage immediately
with an oil-binding agent.
Check the condition of the sealing ring (the sealing
ring is vulcanized onto the oil-drain plug). If necessary,
use a new oil-drain plug.
Screw in the screw plug again and shut the oil-drain cock.
Clean the oil filter in the oil-cooling system (see
operating instructions of the oil-supply system).
Clean the breather plug (see item 8.2).
Screw in the breather plug including reducing screw.
Table 1 — Oil Renewal Period
Unit operating temperature (ºC)
Renewal period
Mineral oil ISO VG Class
Up to 75ºC
4320 hrs or 6 months
75ºC to 85ºC
3000 hrs or 6 months
85ºC to 95ºC
2500 hrs or 3 months
95ºC to 105ºC
2000 hrs or 3 months
Lubricants Chart
DIN (ISO)
ISO VG
Class
Mobil
Shell
Total
Castrol
MAK Lubricants
Servo
HP
CLP
VG 150
...
...
...
Castrol
Alpha SP 150
Bharath Amocam
Oil 150
Servo Mesh SP
150
Parthan EP 150
CLP-HP
VG 150
Mobilgear SHC
XMP150
...
Carter SH
150
Optigear Synthetic
X 150
...
Servosyngear 150
...
CLP
VG 220
Mobilgear
XMP220
Shell Omala
F220
Carter EP
220
Castrol
Alpha SP 150
Bharath Amocam
Oil 220
Servo Mesh SP
220
Parthan EP 220
CLP-HP
VG 220
Mobilgear SHC
XMP220
Shell Omala
Oil HD 220
Carter SH
220
Optigear Synthetic
A 150
...
Servosvneear 220
...
CLP
VG 320
Mobilgear
XMP320
Shell Omala
F320
Carter EP
320
Castrol
Alpha SP 320
Bharath Amocam
Oil 220
Servo Mesh SP
320
Parthan EP 320
CLP-HP
VG 320
Mobilgear SHC
XMP320
Mobil SHC 632
Shell Omala
Oil HD 320
Carter SH
320
Optigear Synthetic
A 320
...
Servosyngear 320
...
CLP
VG 460
Mobilgear
XMP460
Shell Omala
F460
Carter EP
460
Castrol
Alpha SP 460
Bharath Amocam
Oil 460
Servo Mesh SP
460
Parthan EP 460
CLP-HP
VG 460
Mobilgear SHC
XMP460
Mobil SHC 634
Shell Omala
Oil HD 460
Carter SH
460
Optigear Synthetic
A 460
...
Servosyngear 460
...