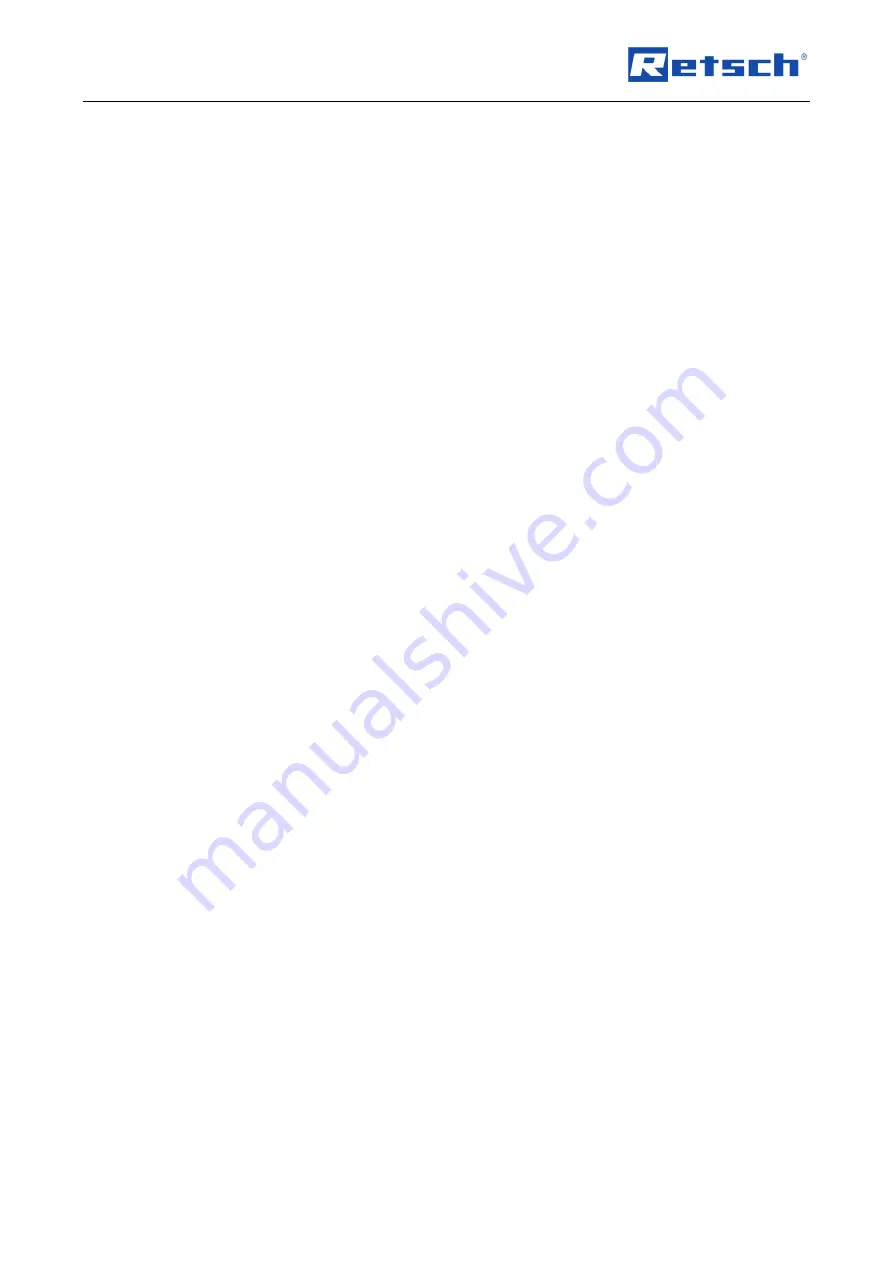
Safety
15
2.8 Avoiding damage to property
•
Protect the device from condensation in case of expected strong temperature fluctuations
(e.g. during air transport).
•
When transporting the device to the place of use or when setting it up, avoid any impacts
and vibrations.
•
Observe the conditions for the installation site when setting up the device.
•
When inserting the grinding tools, make sure that the anti-rotation device is correctly
engaged. Otherwise, the device cannot be started and the ring sieve may be damaged.
•
The device must not be started if the grinding tools are not complete and correctly inserted.
•
The device must not be started without the ring sieve in place.
•
Do not feed any sample material before the grinding gear is running. Mechanical
components can be damaged when starting with sample material in the cassette.
•
Do not feed sample material too quickly and do not overfill the cassette, which serves as a
collecting vessel. Excessive filling can lead to overheating and damage to the housing.
•
After grinding, do not remove the rotor by force, but wait for the temperature to equalise.
Forcible removal will damage the rotor shaft and rotor.
•
Use a damp cloth for cleaning.
•
Do not use solvents or aggressive cleaning agents for cleaning.
•
For maintenance, only use original spare parts.
•
If the rotor is not used for a longer period of time, pull it off the rotor shaft, otherwise crevice
corrosion may occur due to moisture and rust.
•
Do not lock the device hood when it is not used for an extended time as this may damage
the cassette seal.