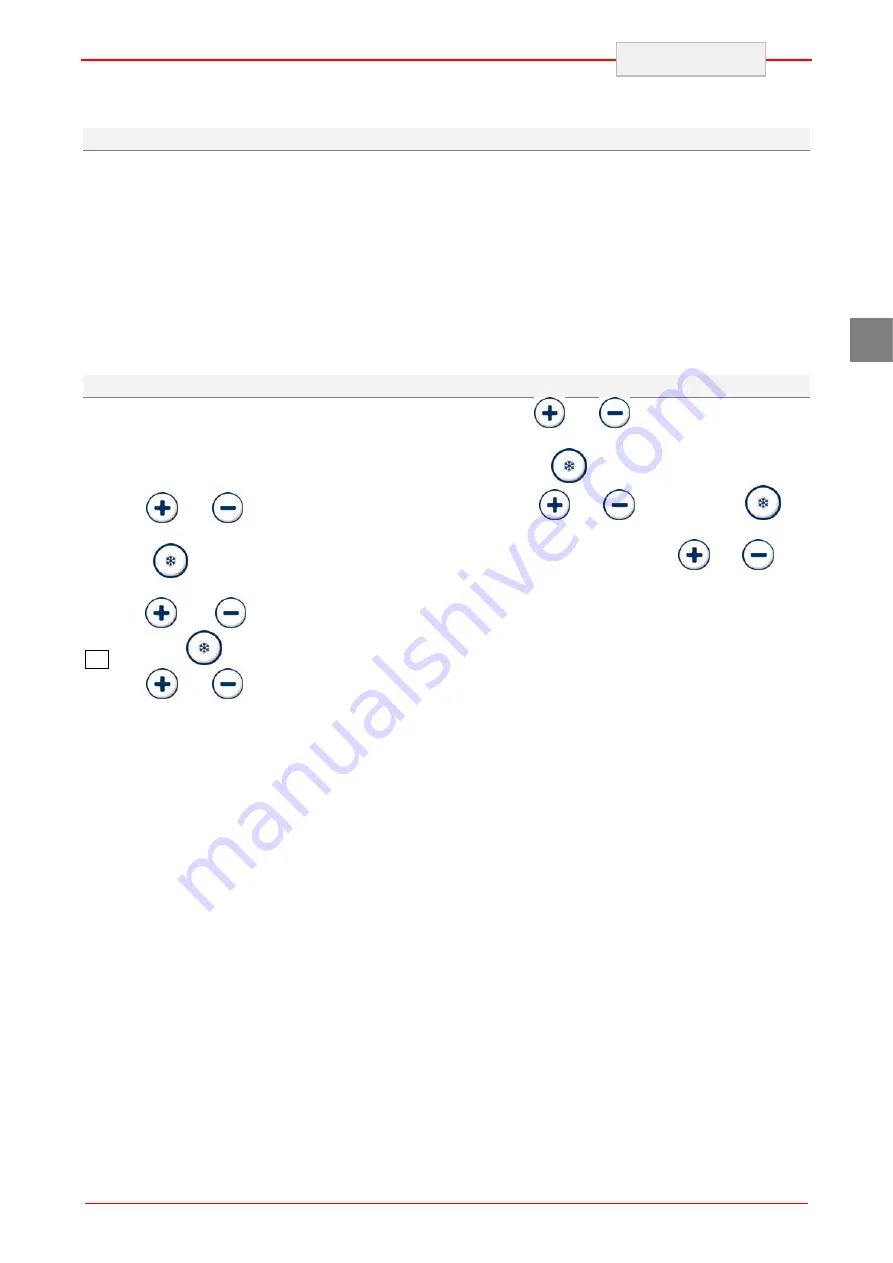
23
ENGLISH
GB
8.4. Inspection
The appliance is delivered in conditions such that
it can be started-up by the user.
This functionality is guaranteed by passing the
tests (electric inspection - functional inspection,
appearance inspection) and relative certification
through the specific attachments.
At least the following should be checked after
installation:
Check the electric connections.
Check the functionality and efficiency of
drains.
Check that there are no tools or materials
left in the appliance that could jeopardise
its functionality or even damage the
machine.
Have the appliance perform at least one
complete chill blasting/shock freezing
cycle
8.5.
Programming the settings
It is only possible to program the configuration
settings in
STANDBY
mode.
Make sure the keyboard is not locked.
Hold the
and
keys down for 4 seconds:
the screen will display the letters "
PA
".
Press the
key: the password will be required
to access the parameters.
With the
and
keys enter the password
-19
: press the
key to confirm.
Hold the
and
keys down for 4 seconds:
the screen will display the letters "
SP
" (first
available parameter).
With the
and
keys it is possible to scan
the list of parameters
Press the
key to change the parameter
using the
and
keys: press the
key
to confirm the change.
To exit the procedure hold the
and
keys
down for 4 seconds.
To make some of the parameters
operational it is necessary to turn the appliance off
and on again.