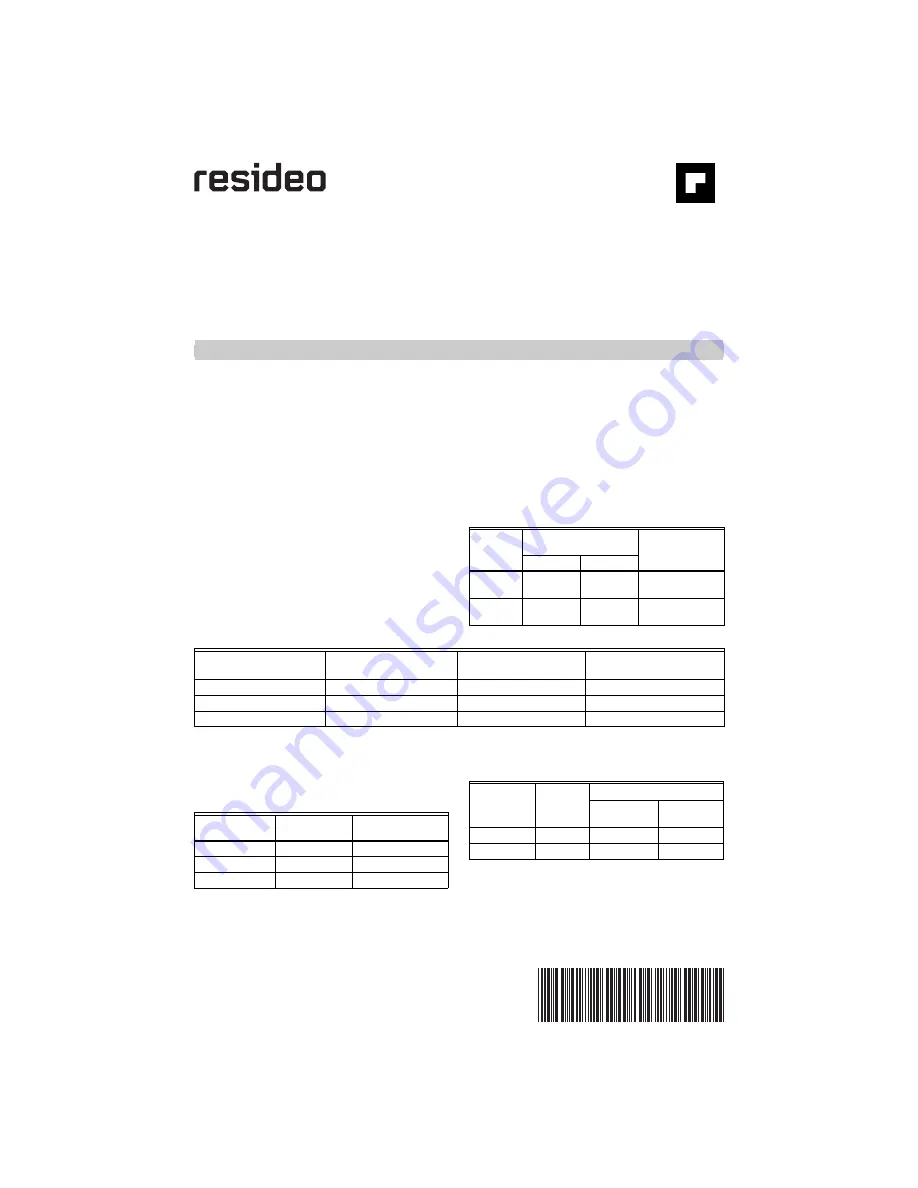
INSTALLATION INSTRUCTIONS
69-0668-05
VR8300 Continuous Pilot
Combination Gas Control
APPLICATION
These continuous pilot gas controls are used in gas-
fired appliances with capacities up to 200 cfh at 1 in. wc
pressure drop (5.7 cmh at 0.25 kPa) on natural gas.
Included are a manual valve, safety shutoff, two
automatic operators, and a pressure regulator. See
Table 1 for temperature range and regulator type.
The VR8300 setup for natural gas includes a 393691 LP
Conversion Kit. The kit contains a new cap screw, a
pressure regulator adjustment screw, a tapered spring
and a conversion label. The LP to Natural gas
conversion kit is 394588. Step-opening gas controls
cannot be converted.
Conversion Kits:
Natural to LP conversion kit is 393691. LP to Natural
conversion kit is 394588. Conversion kits contain a
new cap screw, a pressure regulator adjustment
screw, a tapered spring and a conversion label. Step-
opening gas controls cannot be converted.
Body Pattern:
Straight-through body pattern.
Inlet x Outlet Sizes Available:
1/2 x 1/2 in., 1/2 x 3/4 in., and 3/4 x 3/4 in.
Adapters:
Adapters available for 1/2 and 3/4 in. straight and angle
connections. Refer to Table 4.
Electrical Voltage:
Voltage and Frequency: 24 Vac, 50/60 Hz.Current Draw:
0.70A.
Table 1. Temperature Range and Regulatory Type.
Table 2. Capacity
a
Capacity based on 1000 Btu/cu ft, 0.64 specific gravity natural gas at 1 in. wc pressure drop (37.3 MJ/cu m, 0.64
specific gravity natural gas at 0.25 kPa pressure drop).
Use conversion factors in Table 3 to convert capacities
for other gases.
Table 3. Gas Capacity Conversion Factors.
Table 4. Flange Part Numbers.
a
Flange kits include one flange with attached O-ring
and fan mounting screw.
b
Do not use flanges on gas controls with 3/4 inch inlet
and 3/4 inch outlet. On models with
1/2 inch inlet and 3/4 inch outlet, use flanges only on
the 1/2 inch inlet side.
Approvals:
CSA 112395
Model
Number
Ambient Temperature
Range
Regulatory Type
°F
°C
VR8300A 0° to 175°
18° to 79°
Standard-
opening
VR8300M -40° to
175°
-40° to 79° Standard-
opening
Size (Inlet x Outlet)
Capacity at 1 in. wc
Pressure Drop
a
Minimum Regulated
Capacity
Maximum Regulated
Capacity
1/2 in. x 1/2 in.
180 cfh (5.1 cmh)
30 cfh (0.8 cmh)
225 cfh (6.4 cmh)
1/2 in. x 3/4 in.
190 cfh (5.4 cmh)
30 cfh 0.8 cmh)
290 cfh (8.2 cmh)
3/4 in. x 3/4 in.
200 cfh (5.7 cmh)
30 cfh (0.8 cmh)
300 cfh (8.5 cmh)
Gas
Specific Gravity
Multiply Listed
Capacity By
Manufactured
0.60
0.516
Mixed
0.70
0.765
Propane
1.53
1.62
Inlet/Outlet
Pipe Size
Flange
Type
Part Number
a, b
Without Hex
Wrench
With Hex
Wrench
1/2 in. NPT
Elbow
393690-13
3/4 in. NPT
Straight
393690-4