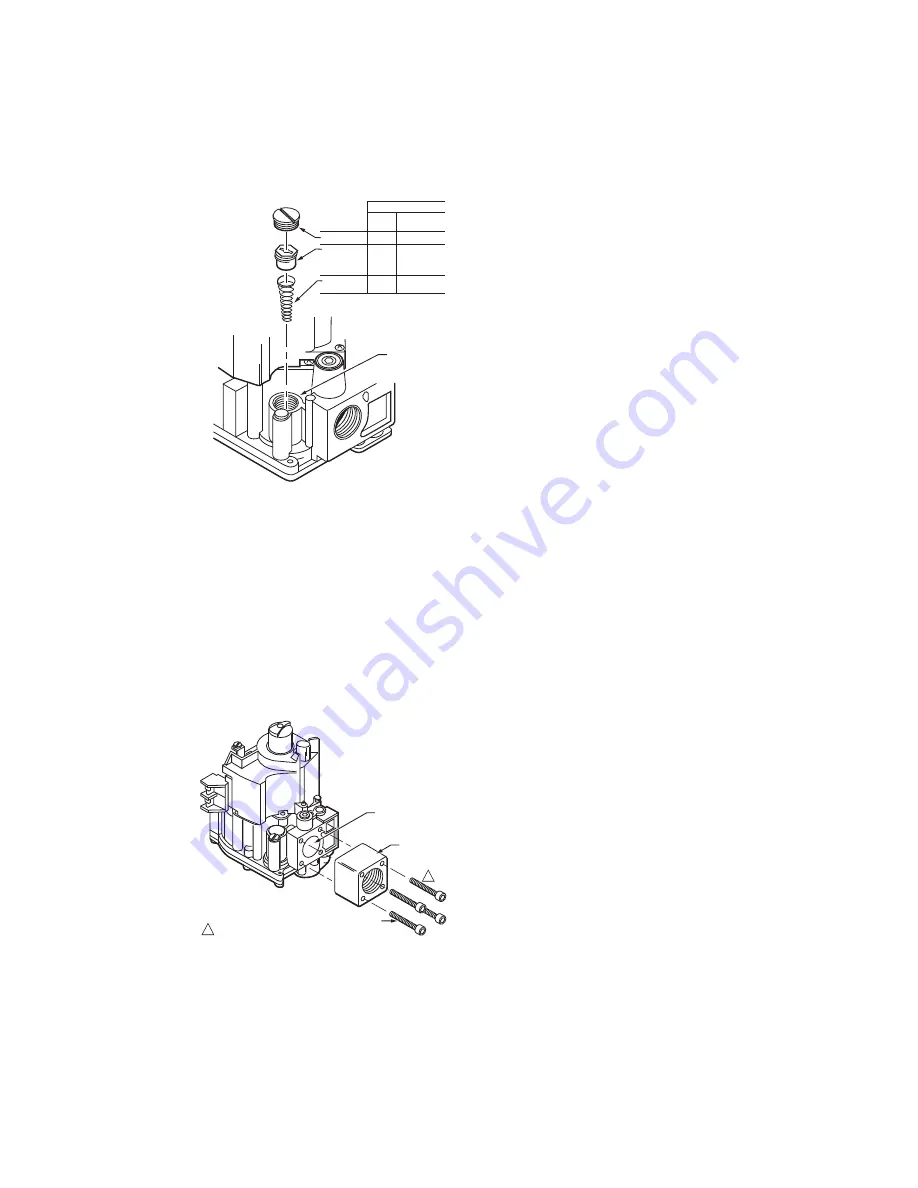
VR8300 CONTINUOUS PILOT COMBINATION GAS CONTROL
3
69-0668—05
Fig. 2. Install conversion kit in regulated gas control.
Install Adapters to Gas Control
If installing adapters on the gas control, mount them as
shown in Fig. 2:
Flanges:
1.
Choose the appropriate flange for your application.
2.
Remove the seal over the gas control inlet or outlet.
3.
Ensure the O-ring is fitted into the groove of the
flange. If the O-ring is not attached or is missing,
do not use the flange.
4.
With the O-ring facing the gas control, align the
screw holes on the gas control with the holes in the
flange. Insert and tighten the screws provided with
the flange. See Fig. 3. Tighten the screws to 25 in.
lb of torque to provide a gas-tight seal.
Fig. 3. Install flange to gas control.
Bushings:
1.
Remove the seal over the gas control inlet or outlet.
IMPORTANT
On LP installations, use a compound resistant
to LP gas. Do not use Teflon tape.
2.
Apply moderate amount of good quality pipe com-
pound to bushing, leaving two end threads bare.
3.
Insert bushing in gas control and thread pipe care-
fully into bushing until tight.
Follow the instructions below for piping, installing
control, connecting pilot tubing, thermocouple and
wiring. Make certain the leak test you perform on the
control after completing the installation includes leak
testing the adapters and screws. If you use a wrench on
the valve after flanges are installed, use the wrench only
on the flange, not the control.
USE ADAPTERS TO SOLVE
SWING RADIUS PROBLEMS
In some field service applications, it is difficult or
impossible to thread the gas control onto the gas supply
pipe because of space limitations. This problem can
usually be resolved by using an adapter. The adapter is
installed on the end of the supply pipe in place of the gas
control, following the same precautions and instructions
that are used for installing the gas control. After the
adapter is installed, the gas control is attached to the
adapter as outlined above. Note that using an adapter
increases the overall length of the gas control.
Choose Gas Control Location
Do not locate the gas control where it can be affected by
steam cleaning, high humidity, dripping water, corrosive
chemicals, dust or grease accumulation, or excessive
heat. To ensure proper operation, follow these guidelines:
• Locate gas control in a well ventilated area.
• Mount gas control high enough above the cabinet
bottom to avoid exposure to flooding or splashing
water.
• Make sure the ambient temperature does not exceed
the ambient temperature ratings for each component.
• Cover gas control if appliance is cleaned with water,
steam, or chemicals or to avoid dust and grease
accumulation.
• Avoid locating gas control where exposure to
corrosive chemical fumes or dripping water is likely.
Locate the gas control in the appliance vestibule on the
gas manifold. In replacement applications, locate the gas
control in the same location as the old gas control.
Install Piping to Gas Control
All piping must comply with local codes and ordinances
or with the National Fuel Gas Code (ANSI Z223.1 NFPA
No.54), which ever applies. Tubing installation must
comply with approved standards and practices.
1.
Use new, properly reamed pipe free from chips. If
tubing is used, make sure the ends are square,
deburred and clean. All tubing bends must be
smooth and without deformation.
2.
Run pipe or tubing to the gas control. If tubing is
used, obtain a tube-to-pipe coupling to connect
the tubing to the gas control.
COLOR CODE FOR
LP
GAS
NATRUAL
GAS
CAP SCREW BLACK
SILVER
PRESSURE
REGULATOR
ADJUSTING
SCREW
WHITE
WHITE
TAPERED
SPRING
RED
STAINLESS
STEEL
PRESSURE
REGULATOR
HOUSING
M16015A
M803A
FLANGE
GAS CONTROL
INLET
9/64 IN. (3.6 MM)
HEX SCREWS (4)
1 DO NOT OVERTIGHTEN SCREWS.
TIGHTEN TO 25 IN. LB.
1