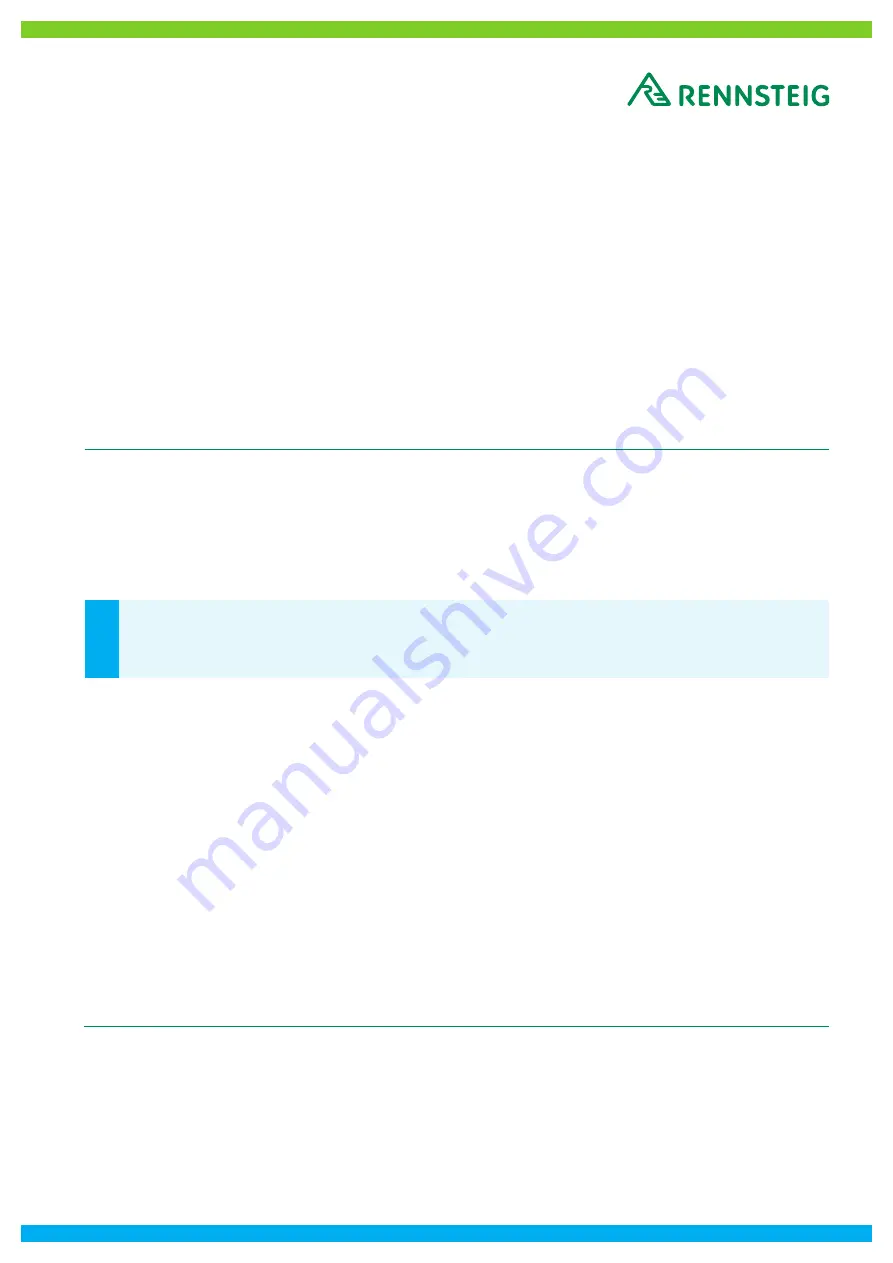
Owner‘s Manual Crimping Machine CM 25-3.4
Rev.: 2020-06-24
14 / 20
Before starting any job, the base setting of the crimping unit (crimping dimensions) needs to be tested.
• Turn crimping unit on by using the “ON/OFF” switch
• Turn the adjustment wheel to the basic setting of the crimping unit (1 or 2 mm depending on the model).
Please ensure that the selected value needs to be set by always dialing down from a larger value to the
desired value, for example, to set the tool to crimp value 2,0 mm, dial up to 2,05 mm first and then down
to 2 mm.
• Push the hand or foot switch to engage the trigger mechanism for the working stroke, keep foot pedal
pushed down (crimping indenters will stop at base setting) now insert the plug gauge between the
indenters. Please note the following:
• The plug gauge is movable in between the indenters without any play – conclusion: There is no
measurement deviation; the crimping unit can be used right away.
• The plug gauge has too much play between the indenters or cannot even be inserted in between the
indenters - There is a measurement deviation; the crimping unit needs to be recalibrated.
10.8. Recalibration of Crimping Unit / Wear and Tear Forecasting Function
The wear and tear forecast function serves the purpose to have the crimping unit, depending upon the
quantity of crimps and the preset crimping measurement, prompting the user to recalibrate the unit (REC in
display).
The recalibration should only be executed by authorized personnel, because an
improper calibration can lead to faulty crimping results.
Attention
• Push the “MODE” button and select mm shown in the d isply ( see chapter 1. 2 “Operational Functionality”)
• Turn the adjustment wheel until the crimping indenters have a value of 2 mm (or 1 mm depending on
crimping unit) and then use the plug gauge to test for the proper fit (plug gauge must fit tight without any
play)
• Start the machine by pressing the hand or foot pedal and keep the button or pedal pushed down (Crimping
indenters will stay in the base position until the proper fit is determined)
• Repeat procedure until the plug gauge value is reached
• Please note that the selected value needs to be set by always dialing down from a larger value to the
desired value, for example, to set the tool to crimp value 2,0 mm, dial up to 2,05 mm first and then down
to 2 mm.
• Keep “ON/OFF” button pressed and at the same time use the plug gauge to push the recessed “MODE”
button for at least 5 seconds
• After 5 seconds release the “MODE” button and afterwards the “ON/OFF” button
• The digital display will jump automatically to the plug gauge measurement of 2 mm (or 1 mm depending
on the crimping unit)
• The crimping unit is now recalibrated and ready for the entering of crimping parameters