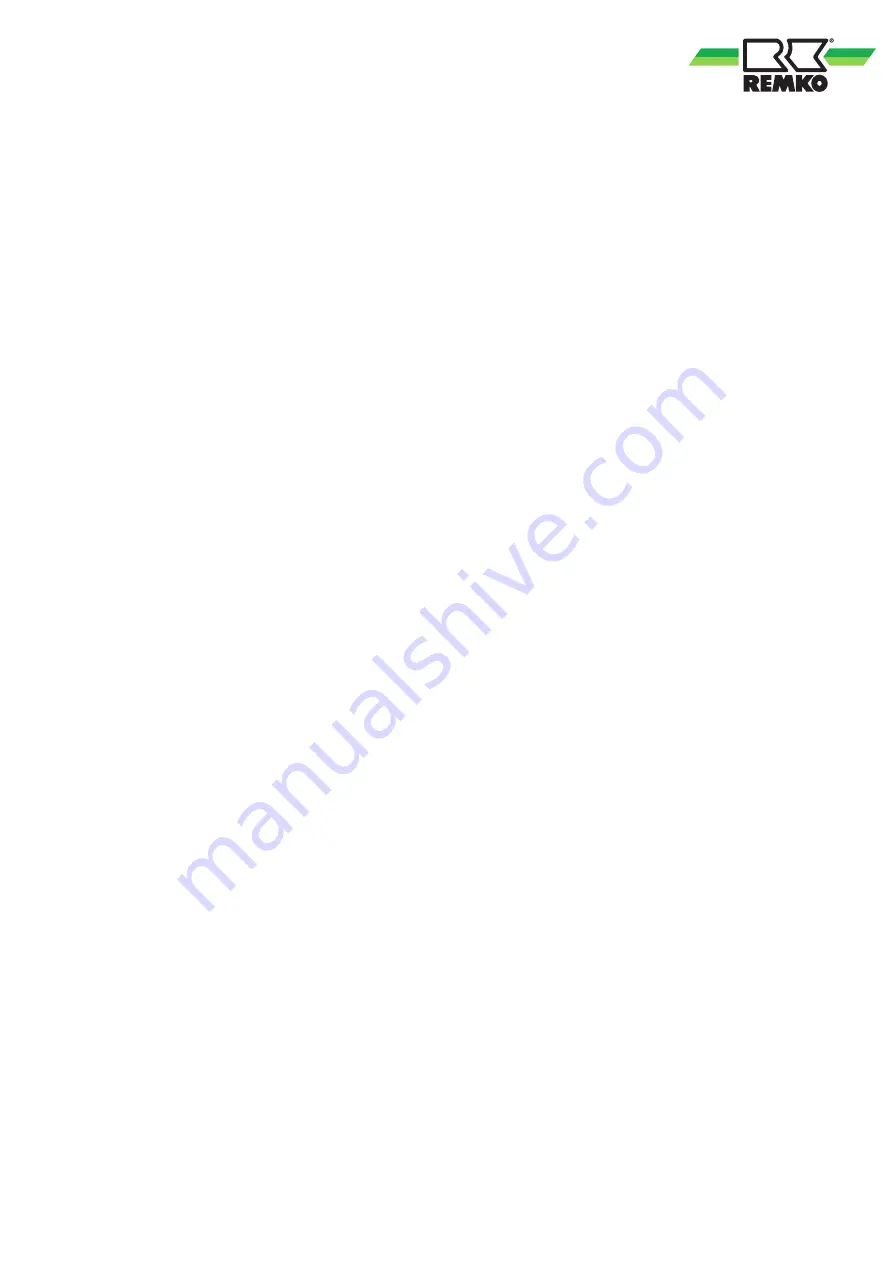
the safety functions, is used to
control the cooling capacity.
A potential-free contact provides
for remote enabling.
The unit is designed for outdoor
installation. Under certain
circumstances, it can also be used
in indoor areas.
The unit cooling cycle comprises an
evaporator, compressor, electronic
injection valve, condenser,
condenser fan, pressure transducer,
high and low pressure switches
and a 4-way changeover valve
for heating mode. The medium
cycle comprises a tube bundle heat
exchanger, a circulation pump and
a flow switch.
Vibration dampers, cabled remote
controls and glycol concentrate are
available as accessories.
The units are shipped in sturdy
transport packaging. Immediately
check the units on delivery and
make a note of any damage or
missing parts on the delivery note.
Inform the forwarding agent and
contractual partner.
Claims under guarantee made at
a later date will not be accepted.
Unit description
Transportation and packaging
In cooling mode, the unit (an
air-cooled chiller) takes heat out
of the operating medium to be
cooled, water or a mixture of
water and glycol, within a closed
medium cycle in the evaporator
(plate heat exchanger) and passes
it on to the closed cooling cycle.
As a consequence of the heat
exchange, the medium cools and
the refrigerant in the cooling cycle
vaporises under low pressure.
The gaseous refrigerant
enters an electric compressor
(scroll construction) which
increases the pressure and
the temperature of the refrigerant.
The gaseous refrigerant is
led into a finned condenser,
which, as a consequence of
the heat exchange, condenses
the refrigerant under high
pressure to a liquid. The air
emerging at the condenser heats
the environment. The liquid
refrigerant is fed by means of a
variable injector valve back to
the evaporator where the circuit
begins again.
A return temperature dependent,
seamless controller, which ensures
the unit's operation and all of
Intended use
Depending on the model and
the unit, the units are only
intended to be used as a chiller
for the cooling of the operating
medium water or a water-glycol
mixture within a closed medium
cycle.
Any other use or use in a way
that exceeds the definition above
is considered non-intended
use. The manufacturer/supplier
assumes no liability for damages
arising from non-intended use.
The user bears the sole risk in such
cases.
Intended use also includes working
in accordance with the operating
and installation instructions and
complying with the maintenance
requirements.
Applicability
Within the course of continuous
further development of all
products, REMKO GmbH & Co.
KG reserve the right to carry
out technical changes to the
units as well as updates to
the documentation.
The documentation on the unit
(name plates, wiring diagrams,
etc.) shall be considered as part of
the overall documentation.
Ecological design directive
The regulation (EU) 2016/2281
(LOT 21) approved by
the European Commission is
the enforcement action for
the ecological design directive
2009/125/EC, whose principal
objective is to reduce the primary
energy demand in the European
Union by 2030 and to reduce
the emissions of hazardous
substances associated with this.
The chillers from REMKO
comply with the applicable
energy requirements from
the ecological design directive.
The product datasheet required
per the ordinance, to verify
ERP conformity is attached as
a separate document and is also
available for download from
www.remko.de.
Proper handling
Insofar as intervention is required
in the refrigerant circuit of the unit
during maintenance or repair
work, all work shall be carried
out exclusively by persons and
companies who have a certificate in
accordance with the prerequisites
of EC ordinance no. 517/2014 of
the European Council.
5