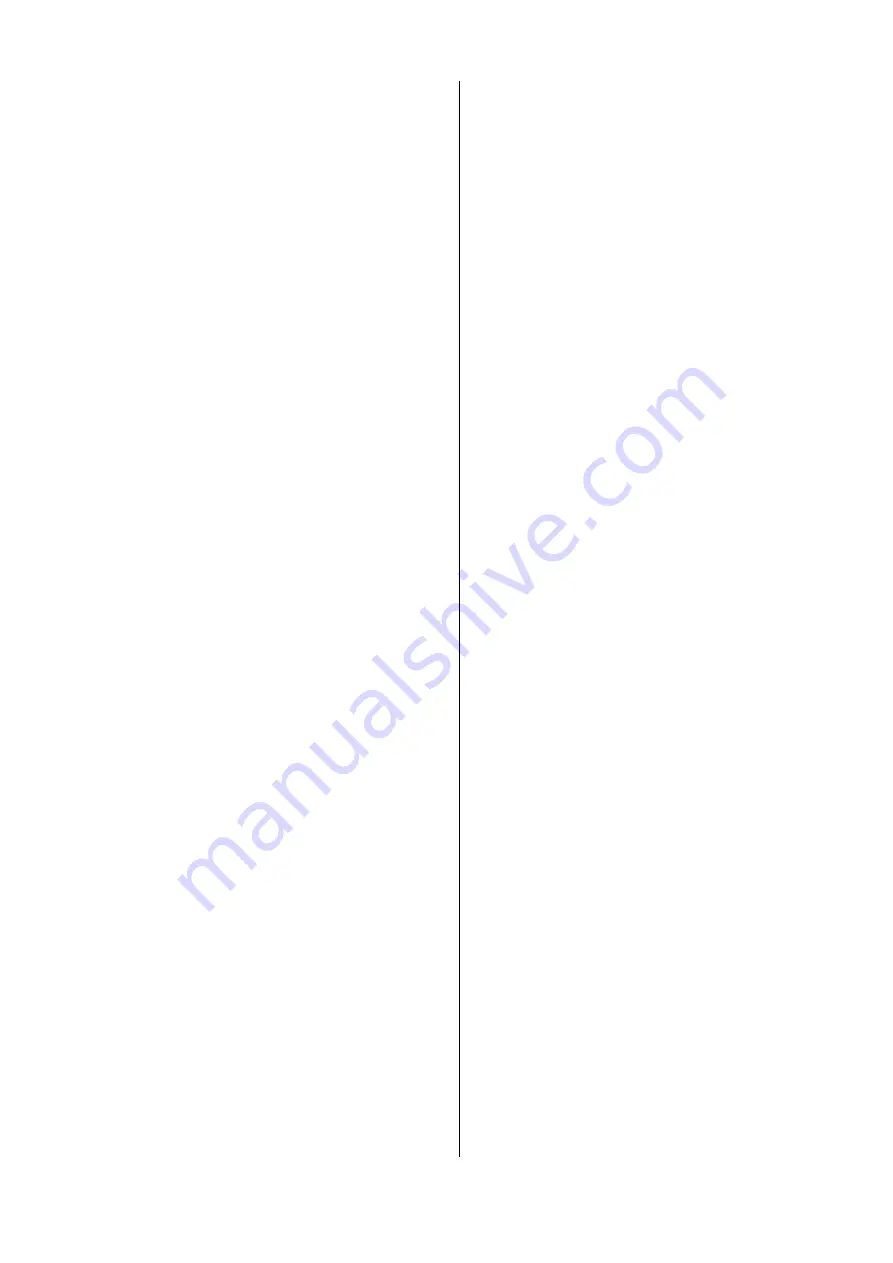
5
General Instructions
The unit may only be operated by persons who have
received proper training in its operation and how to
handle liquid gas.
When operating the unit, make sure to comply with
the relevant national/regional guidelines.
The unit may only be operated in rooms
– with sufficient air supply for combustion
– that are well-ventilated
– where the quantities of substances which can be
harmful when breathed in are admissible.
Good natural ventilation exists when, for example:
1. The room content in m³ equals 30 times the rated
heat output of all units in operation in the room
and natural ventilation is supplied through doors
and windows or
2. There are non-closable openings for air output
and intake close to the ceiling and floor whose
size in m² equals at least 0.003 times the rated
heat output in kW of all heating units in operation
in the room.
A standard unit connection pressure of
1.5 bar
(1500 mbar)
of category I
3B/P
is required for all EU
countries.
The connection pressure may not fall below or ex-
ceed the required value.
When longer hoses are used, the corresponding
pressure loss has to be taken into account.
Use only those parts, such as gas hoses, pressure
controller and mechanisms which protect lines and
hoses from breaking and safety mechanisms that
prevent gas leakage, that have been tested and are
suitable for the intended purpose.
The pressure controllers must have a fixed initial pres-
sure of 1500 mbar and must be equipped with a
mechanism that prevents the hose from breaking.
The unit may not be operated if the gas is in a liquid
state as it enters the burner.
At building sites, only hoses designed for use with
liquid gas may be used.
In accordance with regional regulations.
The length of the gas hose should not exceed 2 me-
tres.
Longer hoses may be used if safety regulations are
observed and the length of the hoses is kept as
short as possible.
Gas hoses must be protected against chemical,
thermal and mechanical damage.
If unit operation is unmonitored, hoses must be used
that protected against breakage.
If work is performed on the gas supply hose or if
the gas cylinder is replaced, all stop valves must
be closed and nothing which can potentially ignite
may be present in the immediate surroundings.
*
Prior to operating the unit, the operating personnel
must check that the unit and its safety mechanisms
are functioning properly and that the safety mecha-
nisms have not been removed.
Any defects are to be reported to the supervisor im-
mediately.
The unit must be switched off if any defects are
found which endanger the safe operation of the unit!
The unit may be only serviced by authorised person-
nel; only original spare parts may be used.
Parts that wear out must be replaced on a regular
basis unless an authorised service person confirms
that the unit is functioning smoothly.
If the unit has been switched off by the temperature
limiter due to overheating, the reason the problem
occurred has to be identified and fixed.