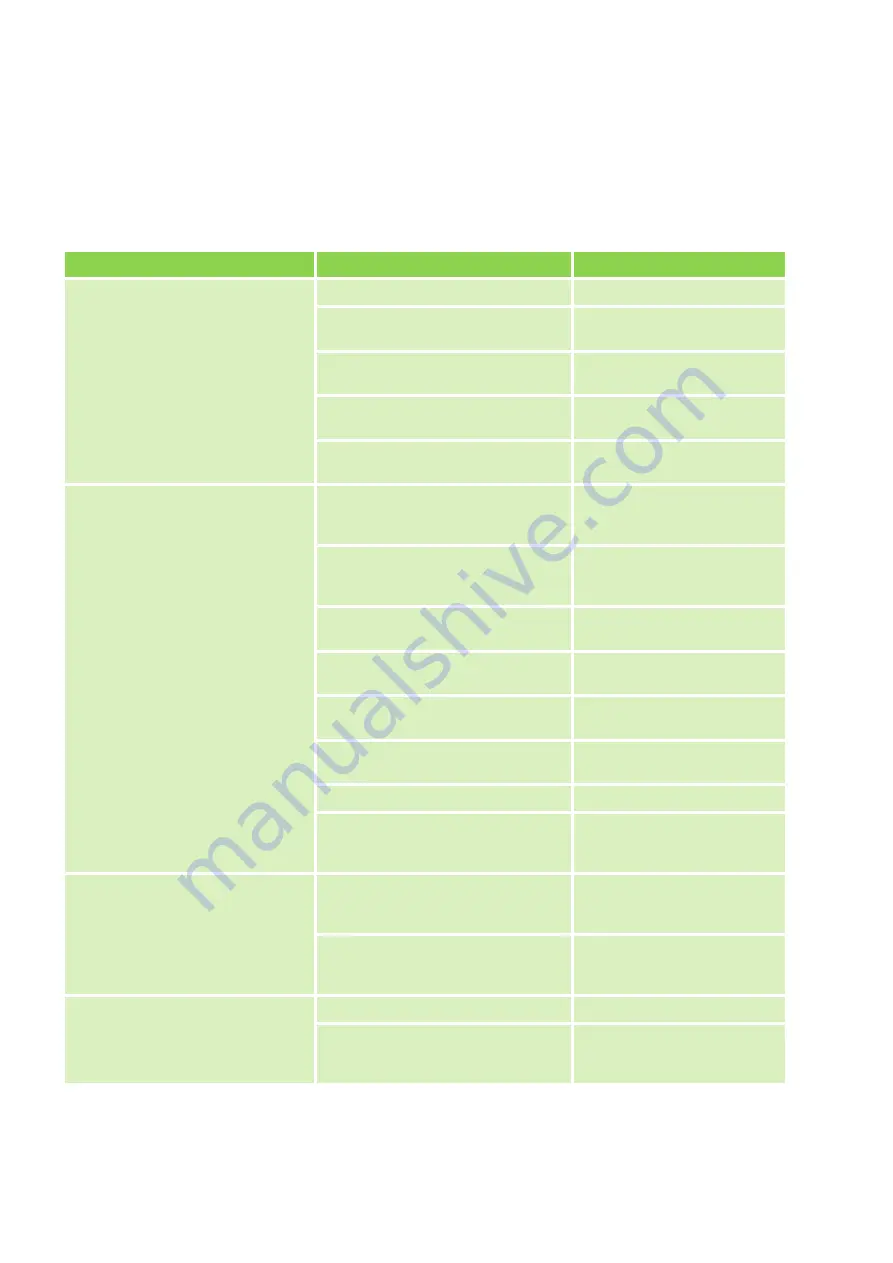
8
Troubleshooting and customer service
The unit has been manufactured using state-of-the-art production methods and has been tested several
times to ensure that it works properly. If malfunctions should occur, please check the unit as detailed in the
list below. Please inform your dealer if the unit is still not working correctly after all the function checks have
been performed.
Fault description
Cause
Remedy
The unit does not start or switches
itself off.
Power supply interrupted.
Check power supply.
Low pressure switch has activated.
Possible loss of refrigerant.
Contact specialist dealer.
Unit is not correctly switched on.
Switch on again using the
remote control
Operational temperature range too
low or exceeded.
Observe operational tempera-
ture range 18 to 35 °C.
The outside temperature lies outside
the operating range (-15 to +50 °C).
Do not operate the unit out-
side the operating range.
The unit does not work or works at
reduced cooling capacity.
Exhaust duct is blocked or longer
than 2 metres.
Ensure that there is a clear
path for the exhaust air.
Shorten the exhaust duct.
Filter contamination, inlet or outlet
blower openings blocked by foreign
bodies.
Clean filter.
Minimum clearances too small.
Observe minimum clear-
ances.
Windows and doors open / heat load
was increased.
Close doors and windows /
reduce heat load.
"Cooling" operating mode is not
selected.
Select the correct operating
mode.
Unit will be switched by means of
the timer function.
Press "I / 0" key again.
Temperature setting too high.
Reduce temperature.
Overvoltage due to local lightning
strike.
Switch unit off and separate
from the power supply for 5
mins., then start anew.
The unit does not respond to the
infra-red remote control.
Batteries in the remote control are
empty or the distance to the receiver
is too great.
Insert new batteries / reduce
distance.
After battery exchange, incorrect
polarity of batteries.
Insert the batteries with the
correct polarity. Observe
marking.
Condensate discharge on unit.
Unit standing at an angle.
Stand vertically.
The stopper for the condensate
drain is not correctly inserted or is
damaged.
Insert stopper correctly or
replace if necessary.
REMKO KWT
22