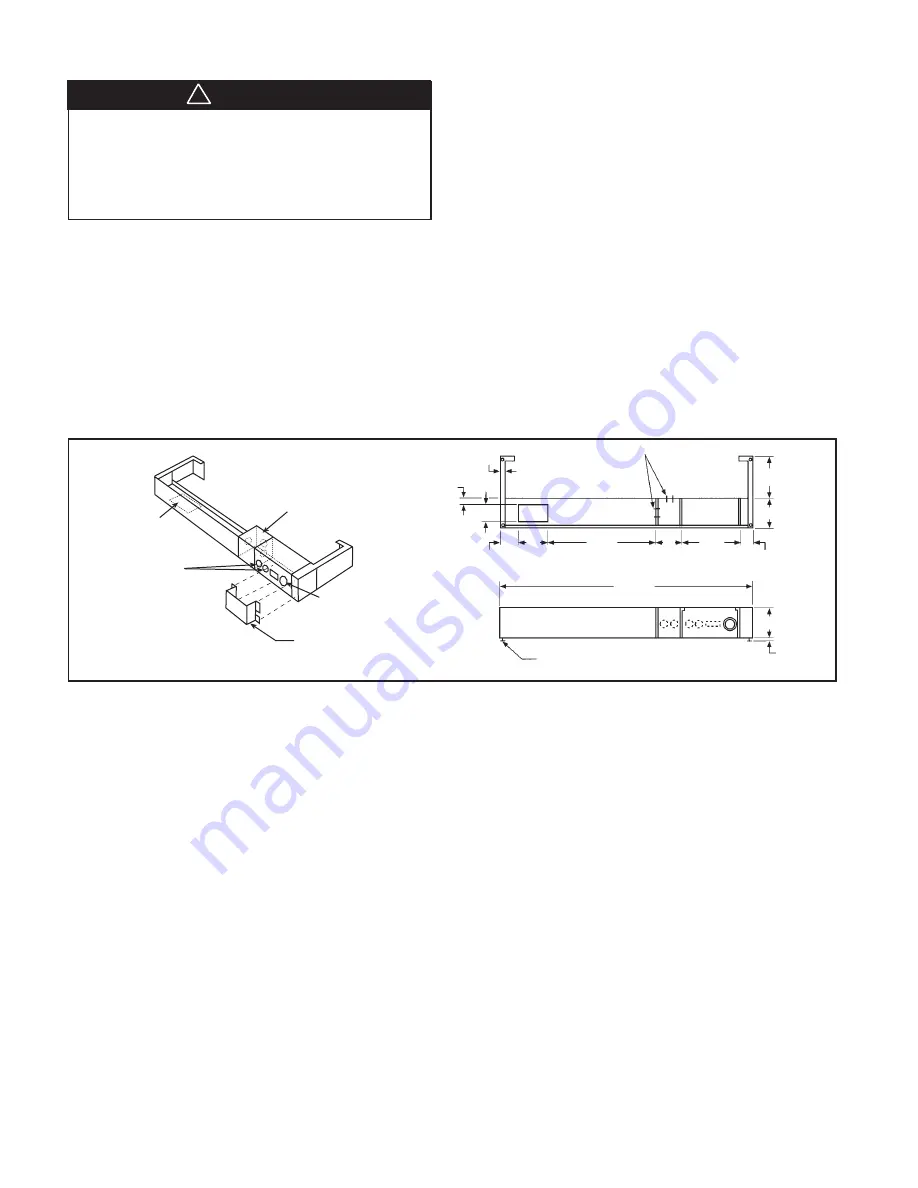
IM 812 / Page 8 of 28
Electric Subbase
An electrical subbase is optional for 208V and 230V units, but
is standard for 265V units. It is available in two sizes: 3˝ or 4˝.
The subbase contains leveling legs for adjustment of up to 1˝
additional height. Install the wall sleeve and subbase at the
same time.
Note: A minimum of 4
3
⁄
8
˝ of the wall sleeve must project
into the room when using a subbase.
Installation
1.
If the minimum depth subbase is required (4
3
⁄
8
˝ ), discard
the side extension pieces. The subbase always mounts
flush with the front of the wall sleeve.
2.
If more than the minimum depth subbase is required, de-
termine the depth of the side extension pieces desired
and break at the proper score-line. Insert the side exten-
sion pieces into the front assembly and secure with two
short black screws at each side.
3.
Insert leveling legs into subbase bottom flanges. Four (4)
legs will be needed if side extensions are used. Only two
(2) will be required if side extensions are not used.
4.
Place the subbase on the floor and align its center line
with the center line of the wall opening. Do not fasten the
subbases to the floor. After the wall sleeve has been in-
stalled, attach the subbase to it using the two clips
provided. Adjust the subbase height so it rests tight against
the bottom of the wall sleeve.
5.
The wiring should be roughed in and the conduit connected
to the electrical junction box. Complete the installation by
wiring the receptacle to the incoming power supply.
Subbase Installation
Figure 5. Electric Subbase
Electrical
Junction
Box for Main
Power Connection
Receptacle
Mounting Location
Plug/Cord Cover
(Required on 265V Units Only)
Knockouts for
Optional Fuse &
Disconnect Switch
Electrical Knockouts
3" or 4"
0" to 1"
41
1
⁄
2
"
Leveling Leg
17"
12"
5"
2
1
⁄
2
"
0" to 9
3
⁄
8
"
4
3
⁄
8
"
1
1
⁄
2
"
7
⁄
8
"
5
⁄
8
"
3"
Plan
Front Elevation (Three Front Panels in Place)
3
" x 5"
Opening for
Electrical and/or
Drain Rough-In
Side
Extension
Piece
3
1
⁄
2
"
All wiring must be done in accordance with local and National
Electrical Code requirements. Some units have a multitap
heater, so the Kw is determined by the field-installed power
cord, and some have factory installed cords with fixed heat-
ers. Refer to the data plate for proper overcurrent protection.
Time delay fuses or HACR circuit breakers are required to avoid
nuisance tripping.
Power Supply Wiring
208V and 230V units use a power cord that exits from beneath
the conditioner on the control (R.H.) side. The cord has a usable
length of 60˝ from where it exits the conditioner. (Do not use
extension cords.) When a subbase is not used, the receptacle
is generally mounted beneath the conditioner or on the wall
beside it (208-230V only). An electrical subbase is available
and contains a junction box for a field-mounted receptacle.
All electrical connections are made within the subbase, thus
eliminating the need for a wall-mounted receptacle (see Fig-
ure 5). The subbase is available in 3˝ or 4˝ height and can be
furnished with a factory-mounted fused disconnect and re-
ceptacle as an option. The subbase is optional for 208V and
230V, but mandatory for 265V. The 265V chassis uses a “short
cord,” which is just long enough to plug into the subbase. A
plug/cord cover is also required on 265V to make the power
cord inaccessible without the use of tools, (see Figure 5).
Power Supply and Control Wiring
Control Wiring
If the unit control pad will be wall mounted, rough in the 35´ or
50´ low-voltage wire harness at this time. The end of the har-
ness, with exposed terminals (the larger black connector), will
plug into the control box at the unit. The other end (smaller
white connector), with concealed terminals, will connect to
the PC board in the control pad on the wall. At the unit, exit
the wall with enough wire harness to reach the CN5 recep-
tacle behind the access cover on the control box front. At the
control pad mounting location on the wall, exit with only a few
inches of wire harness. Route the wire harness through the
opening in the control pad mounting plate and secure the plate
to the wall. Unplug the short cord from the PC board in the
control pad and discard. Plug in the new wire harness from
the wall and snap the control pad onto the mounting plate.
The harness should all be concealed behind the control pad
when finished. If an optional 24V wall stat will be used rather
than the control pad, rough in the 4 to 7 low voltage wires as
required by the stat. If remote ON/OFF control will be used,
rough in 2 low voltage wires (22 ga. min.) to a maximum of
325´ from the unit, (see page 4.) If unit will be connected to a
motion sensor and door switch, rough in the 4 low voltage
wires for the motion sensor and the 2 low voltage wires for the
door switch. Leave enough wire at the unit to reach the recep-
tacles behind the access cover on front of control box.
WARNING
!
All electrical work must be done by trained, experienced
electricians in accordance with applicable codes and stan-
dards. Kinked, bent or chaffed cords; improper ground-
ing or fusing; improper current or voltage; or improper
installation can cause fire or electric hazards that can re-
sult in property damage, personal injury or death.