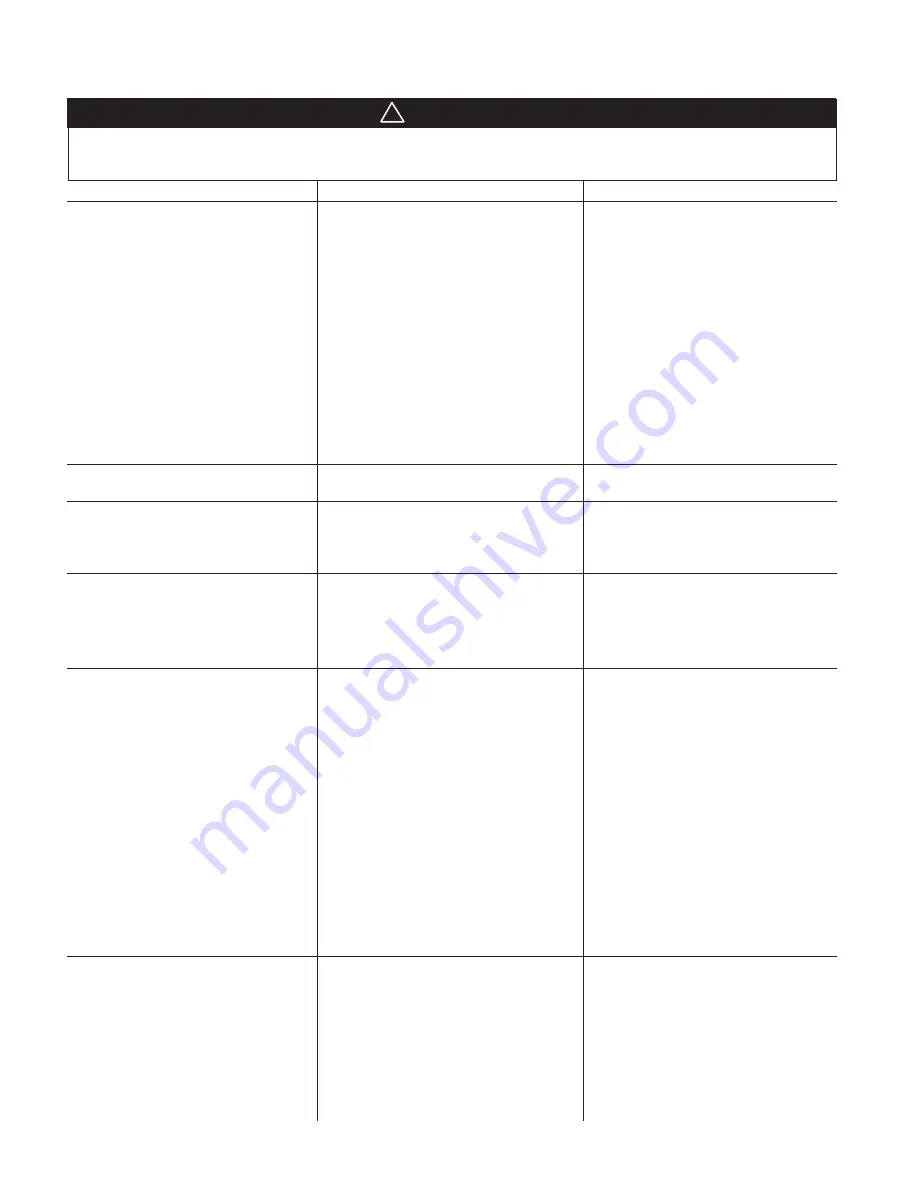
IM 812 / Page 24 of 28
8.
Insufficient cooling capacity.
9.
Too much cooling.
10. “Sweating.”
11. Blowers won’t operate on Heat.
12. Equipment is noisy.
13. Insufficient or no heat.
c.
Insufficient airflow through evaporator due to:
1) Dirty evaporator.
2) Ice on evaporator coils.
3) Dirty air filter.
4) Obstructed discharge grilles.
5) Indoor blower motor not running.
6) Indoor blower motor not up to speed.
7) Indoor fan wheel slipping on motor shaft.
d.
Heat load in room exceeds capacity of
equipment.
e.
Windows and doors in room are open
f.
Compressor not pumping, indicated by:
1) Low wattage.
2) Condenser not warm.
g.
Restricted capillary or strainer.
1) Frost on capillary or strainer
2) Low wattage.
3) Condenser not warm.
4) Evaporator partially frosted, only partially
cool or not at all.
a.
Temperature set too low.
b.
Defective control pad or control box PC board.
a.
Condensate drain from evaporator plugged.
b.
Insulating seals on equipment damaged.
c.
Indoor blower motor not up to speed.
d.
Indoor blower incorrectly positioned.
a.
No power.
b.
Temperature setting too low (control is set on
“cycle fan”)
c.
Faulty control pad or PC boards
d.
Loose connections at control pad or PC
boards.
e.
Defective blower motor
a.
Fan rubbing against enclosure.
b.
Fan motor bearings dry.
c.
Loose fan motor hold-down nuts.
d.
Refrigerant absorbed in compressor oil after
extended shutdown.
e.
Equipment improperly installed.
f.
Loose terminal box cover on compressor.
g.
Loose electrical components.
h.
Copper tubing vibrating.
a.
No power.
b.
Faulty control pad or PC boards.
c.
Loose connection control pad or PC boards.
d.
Temperature setting too low.
e.
HP heating capacity drops with outdoor
temperature.
f.
Faulty electric heater or compressor.
g.
Low air flow (indoors or outdoors).
c.
1) Clean.
2) Low charge or low air flow.
3) Clean or replace.
4) Remove obstructions.
5) Check motor.
6) Check for correct voltage.
7) Adjust blower wheel position and tighten set
screw
d.
Refer to original load calculations, recalculate
heat load.
e.
Close them.
f.
Replace.
g.
Replace.
a.
Adjust.
b.
Replace.
a.
Remove obstructions to water flow.
b.
Repair or replace.
c.
Check for correct voltage. Replace motor or
capacitor.
d.
Adjust.
a.
See No. 1.
b.
Raise the temperature set point.
c.
Replace.
d.
Tighten.
e.
Replace
a.
Adjust fan position on motor shaft or
reposition fan motor bracket assembly.
b.
Replace motor.
c.
Align blower assembly and tighten nuts.
d.
Noise will disappear after equipment runs
awhile.
e.
Make necessary changes.
f.
Tighten.
g.
Fasten securely.
h.
Occasionally equipment will have noise for no
apparent reason. Inspection has revealed no
loose components that might be the source of
the noise. Due to the action of the compressor,
it is possible to have internal noise develop if
the refrigerant tubing has become bent even
slightly. To distinguish this condition from the
simple rattle producing vibration caused by loose
screws, nuts and other components, grasp the
refrigerant tubing at various points throughout
the system until a point is found where the noise
is eliminated or reduced. Bend the copper
tubing very gently until the noise disappears.
a.
Check power supply line fuse, circuit breakers.
Blown fuses would indicate circuit overloading,
a short circuit, or a grounded condition in the
circuit.
b.
Replace.
c.
Replace wire or tighten.
d.
Raise the temperature set point.
e.
Switch to electric heat. (sw. #7 on control
box front)
f.
Repair or replace.
g.
Repair or replace fan/motor.
Troubleshooting can present hazards of electricity, rotating parts, sharp edges and weight. Troubleshooting must be done by trained,
experienced technicians only. Improper troubleshooting can result in equipment damage, severe personal injury or death.
Trouble
Possible Causes
Treatment
Troubleshooting Chart
WARNING
!