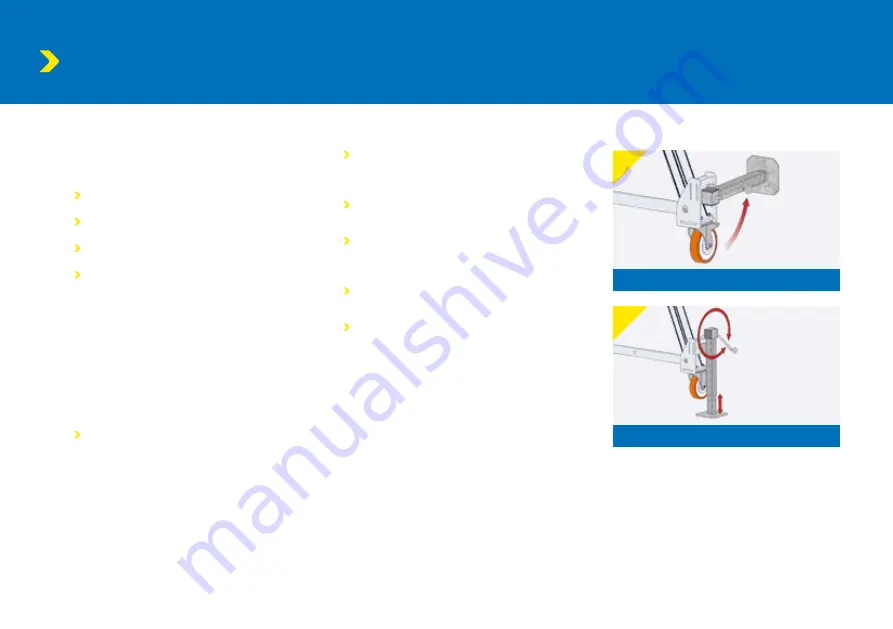
The list below outlines additional variants and
options available;
Wind Up Jack Legs
Ratchet Beam Elevation System
Conversion to Winched Configuration
Customised Configurations
Wind Up Jack Leg Option (WUJL)
WUJL’S can be fitted to the gantry. This provides
additional fine height adjustment (up to 250mm).
Each foot may be adjusted independently
providing a method of levelling the system on
uneven ground.
If wind up jack legs are fitted the following
points must be observed:
Check whether the castors fitted are Load
Rated or Pneumatic.
N.B. For pneumatic (non load bearing) castors
the WUJL system must always be applied prior
to performing any lift. If load rated castors are
fitted the operator can choose whether the
castors or WUJL take the load on each foot of
the gantry
When manoeuvring the gantry, always have
the jack legs in the ‘parked’ position as shown
in figure 1.
Position the gantry for the lift before setting
the height with the jack
Before lifting ensure all jacks are in the correct
lifting position and are secured with locking
pins and clips as shown in figure 2
Manually raise each leg in turn and set the
height by rotating jack handle clockwise
Having set the adjustment of all four legs,
ensure that the gantry uprights are vertical,
and the beam is horizontal
WUJL Inspection/Maintenance
The jack legs and brackets should be subjected
to periodic inspections by a competent person
in line with the products inspection and
maintenance guidelines. It is recommended
that when not in use the jack legs are removed
and stored in a clean and dry manner. The jack
leg should be lubricated with EP2 grease on the
internal thread and gears, at regular intervals (up
to 6 months maximum), depending on service
conditions.
Variants & Options
Wind Up Jack Leg in ‘parked’ position
Jacks secured with locking pins and clips
Fig 1
Fig 2