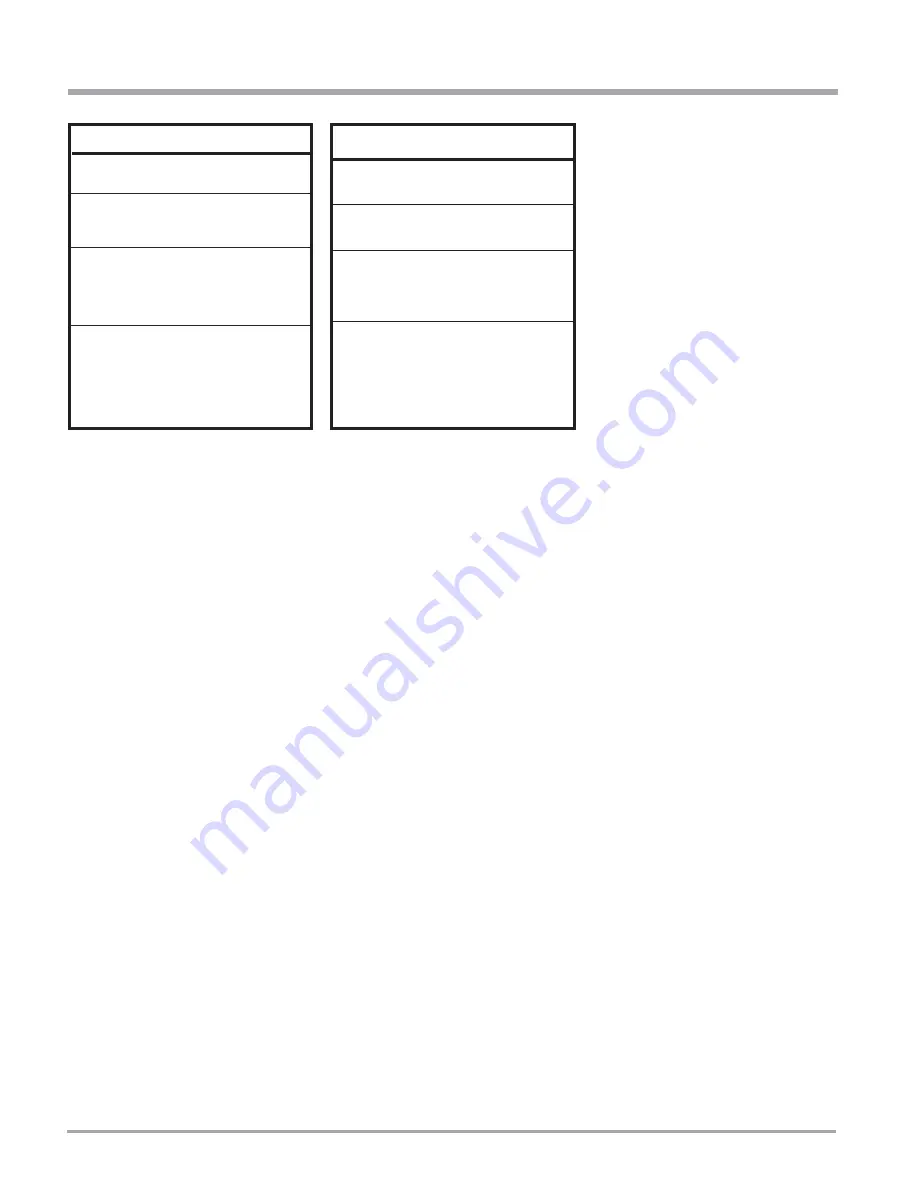
P36E-4 Zero Clearance Direct Vent Gas Fireplace
34
GAS LINE
INSTALLATION
The gas line is brought through the right of the
appliance. The gas valve is situated on the right
hand side of the unit and the gas inlet is on the
right hand side of the valve.
The gas line connection may be made of rigid
pipe, copper pipe or an approved
fl
ex connector.
(If you are using rigid pipe, ensure that the valve
can be removed for servicing.) Since some
municipalities have additional local codes it is
always best to consult with your local authorities
and the CAN/CGA B149 installation code.
For USA installations follow local codes and/or
the current National Fuel Gas Code, ANSI
Z223.1.
When using copper or
fl
ex connectors use only
approved
fi
ttings. Always provide a union so
that gas lines can be easily disconnected for
servicing. Flare nuts for copper lines and
fl
ex
connectors are usually considered to meet this
requirement.
Important: Always check for gas leaks with
a soap and water solution or gas leak detec-
tor. Do not use open
fl
ame for leak testing.
P36E-NG4 System Data
For 0 to 4500 feet altitude
Burner Inlet Ori
fi
ce Sizes:
#37
Max. Input Rating:
29,500 Btu/h
Min. Input Rating:
19,500 Btu/h
Supply Pressure:
min.5.0"
w.c.
Manifold Pressure
(High):
3.5"+/-
0.2"w.c.
Electrical
: 120 V A.C. System.
Circulation Fan
: variable speed 130 CFM.
Log Set
: Ceramic
fi
bre, 7 per set.
Vent System:
Simpson Dura-Vent Direct
Vent System or FPI Direct Vent System (Flex)
P36E-LP4 System Data
For 0 to 4500 feet altitude
Burner Inlet Ori
fi
ce Sizes:
#52
Max. Input Rating
28,500 Btu/h
Min. Input Rating
22,000 Btu/h
Supply Pressure
min.11.0"
w.c.
Manifold Pressure
(High)
10"+/- 0.2" w.c.
Electrical
: 120 V A.C. System.
Circulation Fan
: variable speed 130 CFM.
Log Set
: Ceramic
fi
bre, 7 per set.
Vent System:
Simpson Dura-Vent Direct
Vent System or FPI Direct Vent System (Flex)
INSTALLATION