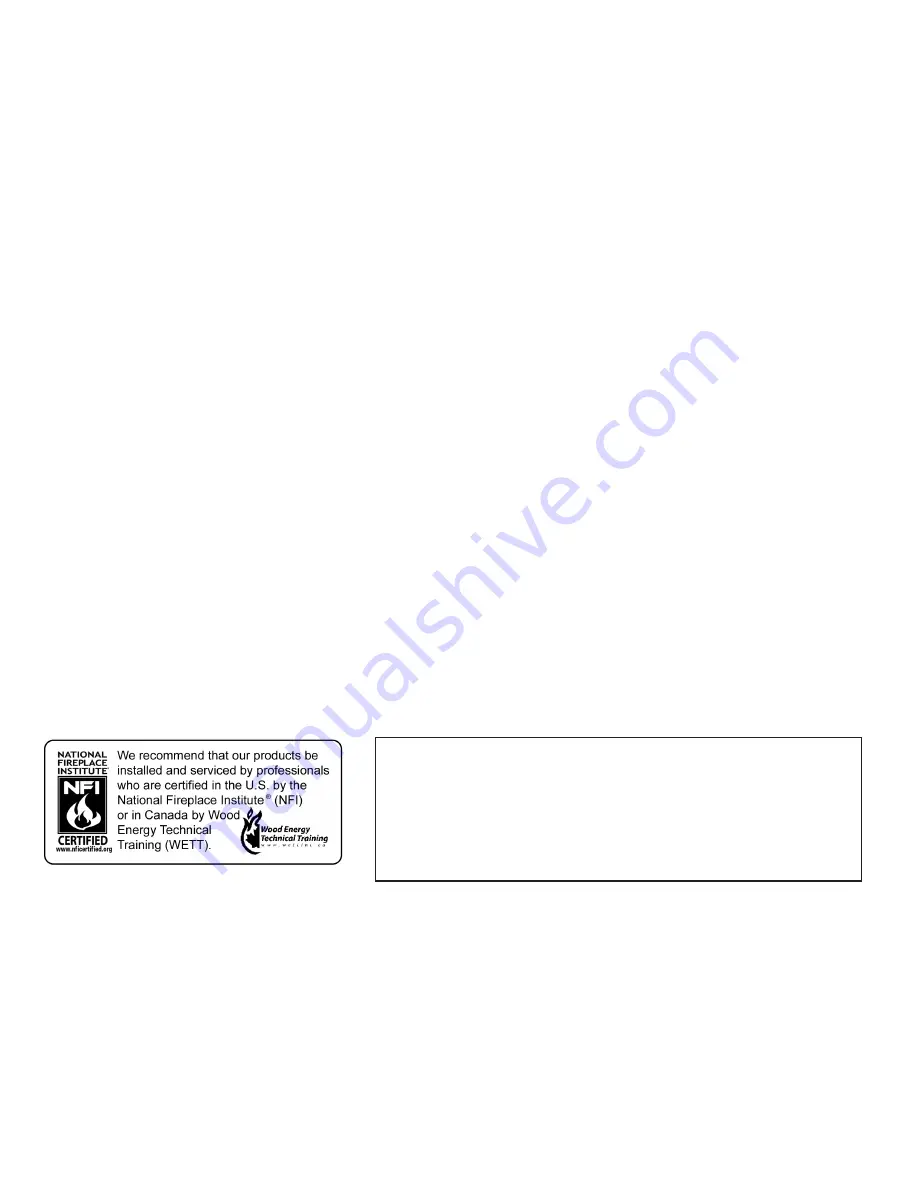
Grandview® G600EC Gas Fireplace
| 3
MANUFACTURED MOBILE HOME REQUIREMENTS
INFORMATION FOR MOBILE/MANUFACTURED HOMES AFTER FIRST SALE
This Regency
®
product has been tested and listed by Intertek as a Direct Vent Wall Furnace to the following
standards: to Vented Gas Fireplace Heaters ANSI Z21.88-2017 • CSA 2.33-2017 and Gas-fired Appliances for Use
at High Altitudes CSA 2.17-2017.
This Direct Vent System Appliance must be installed in accordance with the manufacturer's installation instructions
and the Manufactured Home Construction and Safety Standard, Title 24 CFR, Part 3280, or the current Standard
of Fire Safety Criteria for Manufactured Home Installations, Sites, and Communities ANSI/NFPA 501A, and with
CAN/CSA Z240-MH Mobile Home Standard in Canada.
This appliance installation must comply with the manufacturer's installation instructions and local codes, if any.
In the absence of local codes follow the current National Fuel Gas Code, ANSI Z223.1 and the current National
Electrical Code ANSI/NFPA 70 in the U.S.A., and the current CAN/CGA B149 Gas Installation Code and the current
Canadian Electrical Code CSA C22.1 in Canada.
This appliance comes equipped with a dedicated #8 Ground Lug for attachment of the ground wire to the steel
chassis as applicable to local codes.
The appliance, when installed, must be electrically grounded in accordance with local codes or, in the absence of
local codes, with the National Electrical Code, ANSI/NFPA 70, or the Canadian Electrical Code, CSA C22.1.
This appliance may only be installed in an aftermarket permanently located, manufactured (U.S.A only) or mobile
home, where not prohibited by local codes.
This appliance can only be used with the type of gas indicated on the rating plate. This appliance is not convertible
for use with other gases.
Ensure that structural members are not cut or weakened during installation.
This appliance may be installed in an aftermarket permanently
located, manufactured (U.S.A. only) or mobile home, where
not prohibited by local codes.
This appliance is only for use with the type of gas indicated on
the rating plate. A conversion kit is supplied with the appliance.