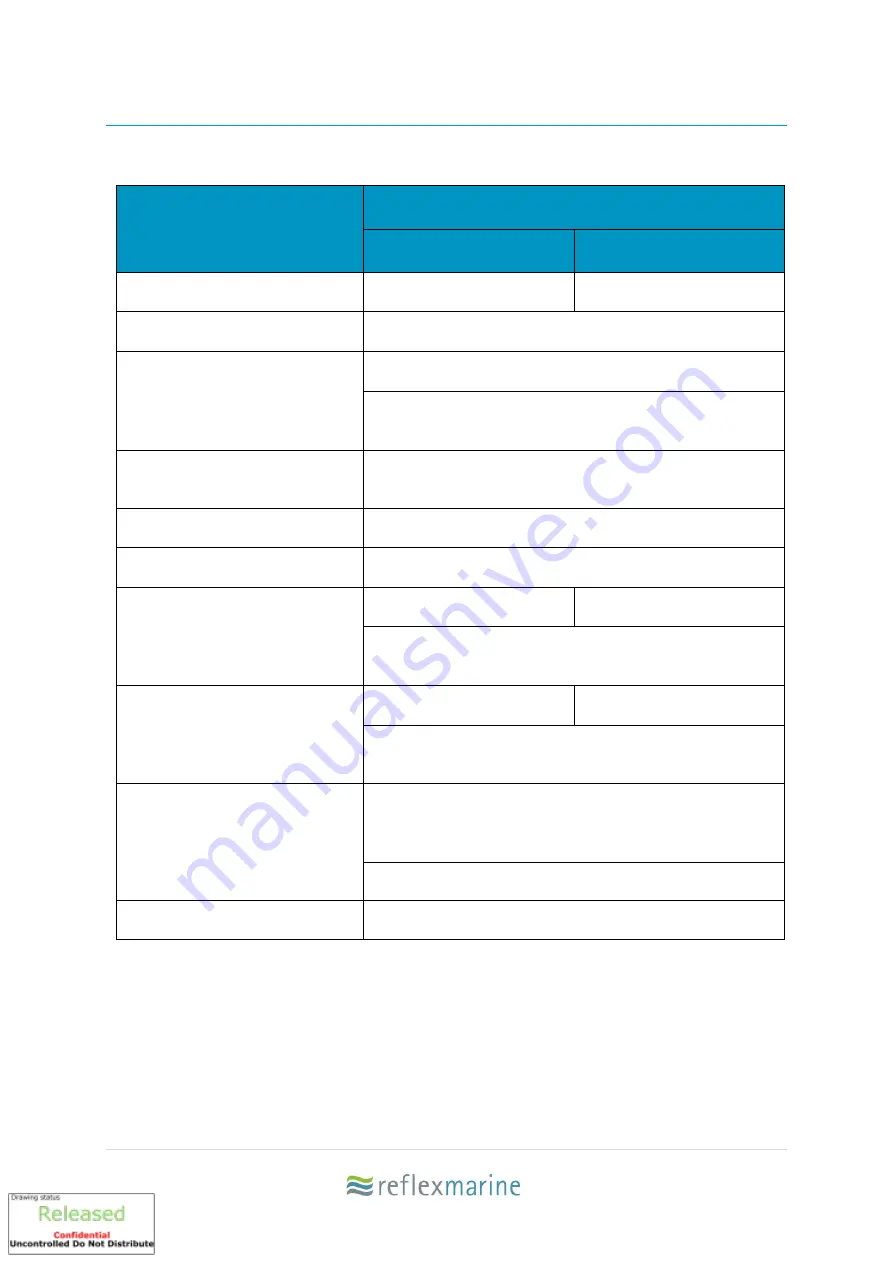
UM-0206(1)
7 | P a g e
2.2
Recommended Operating Parameters
Table 3 Recommended Operating Parameters
Parameter
Recommendation
XT4 + XT6
XT10
Vertical Impact Protection
4.5 m/s
:
14.8 ft/s
3.9 m/s
:
12.10 ft/s
Lateral Impact Protection
2 m/s
:
6.6 ft/s
Wind Speed
20 m/s
:
40 knots
Frog-XT is very stable in high winds. However, crane
limits must be observed
Visibility
Crane Operator should have a clear view of the pickup
and set down areas.
Vessel Motion
10
⁰ Pitch and Roll
Vessel Station-Keeping Radius
5 m
:
16 ft
Landing Area: Vessel
6m x 6m
:
20ft x 20ft
8m x 8m
:
26ft x 26ft
Landing area on vessel recommended equivalent to 2m
clearance all round.
Landing Area: Installation
4m x 4m
:
13ft x 13ft
6m x 6m
:
20ft x 20ft
Landing area on vessel recommended equivalent to 1m
clearance all round.
Landing Area: General
Smaller landing areas may be used provided a risk
assessment of factors such as deck hazards, weather,
sea state, vessel size, station-keeping is carried out.
Must be clear of any obstructions or hazards
Crane Requirements
Crane must be suitable for lifting personnel
Summary of Contents for FROG-XT Series
Page 1: ...USER MANUAL REV 1 UM 206 1 Issue date 13 Oct 2020 Original Instructions...
Page 31: ...UM 0206 1 30 P a g e Figure 12 FROG 10 Pre Operational Visual Check List...
Page 43: ...UM 0206 1 42 P a g e 7 Certificates 7 1 EC Attestation of Conformity Frog XT4...
Page 44: ...UM 0206 1 43 P a g e 7 2 EC Attestation of Conformity Frog XT6...
Page 45: ...UM 0206 1 44 P a g e 7 3 EC Attestation of Conformity Frog XT10...
Page 49: ...UM 0206 1 48 P a g e...