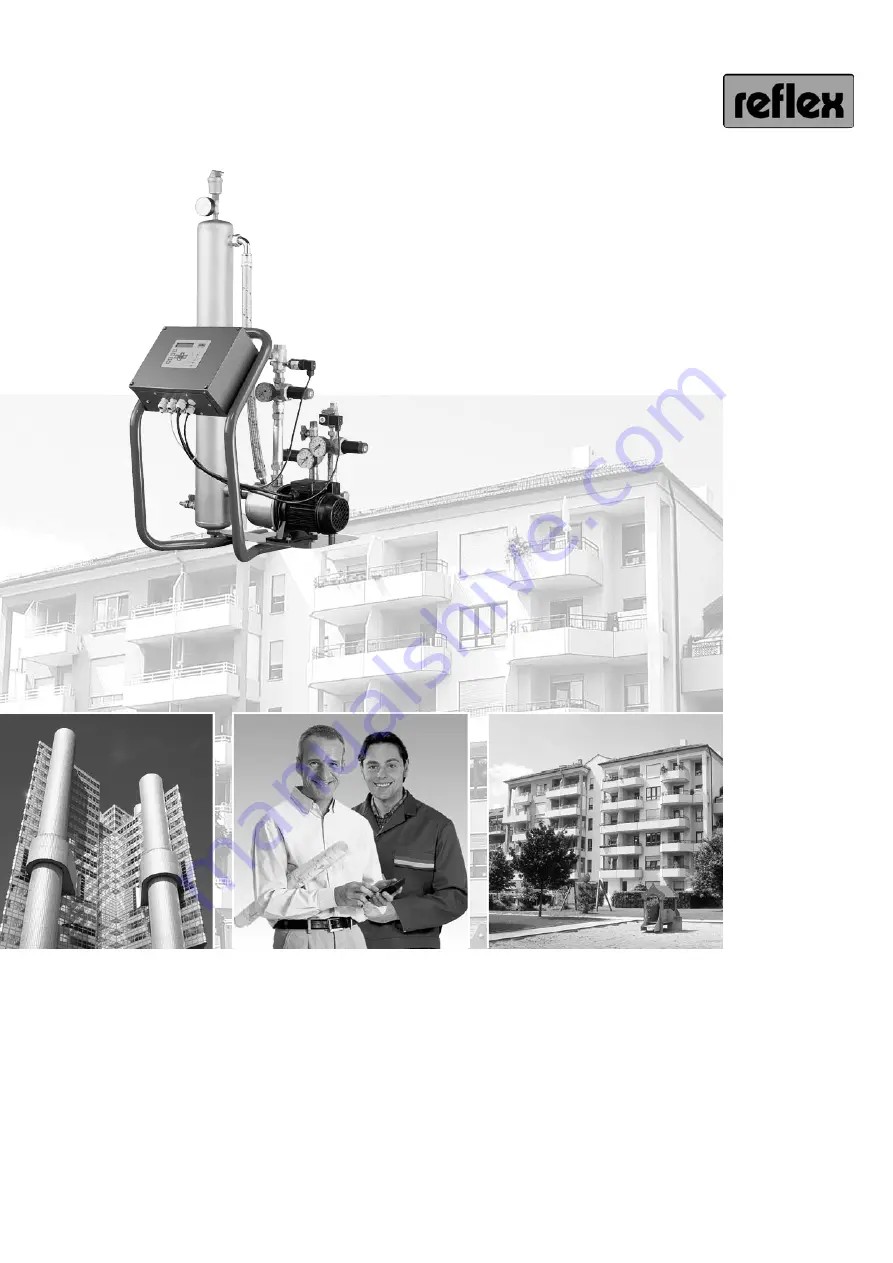
reflex ’servitec’
Vacuum spray-tube deaerator
Installation, operating and maintenance instructions
Status 09/04
General
Overview, type key
3
Operating panel
4
Safety instructions, regulations and standards
5
Installation
Scope of delivery
6
Place of installation
6
Installation
6
Installation diagrams
7 – 8
Electrical connection
9 – 10
Initial start-up
Prerequisite for start-up
10
Starting routine
11 – 12
Filling and bleeding the pump
12
Vacuum test
12
Hydraulic balancing
13
Automatic operation
13
Cleaning dirt traps
14
Operation
Automatic mode
15
Manual mode
15
Stop mode
15
Customer menu
16 – 17
Service menu
17
Summer operation
18
Default settings
18
Interface RS-485
18
Messages
19
Maintenance
Maintenance instrucitions
20
Disassembly
21
Periodic check-ups
21
Reflex service
21
General description
Operation
22 – 23
Operating parameters
23
Dimensions, weights
23
Applications
23
Electrical details
23
Declaration of conformity
24
Installation, maintenance and commissioning certificate
25