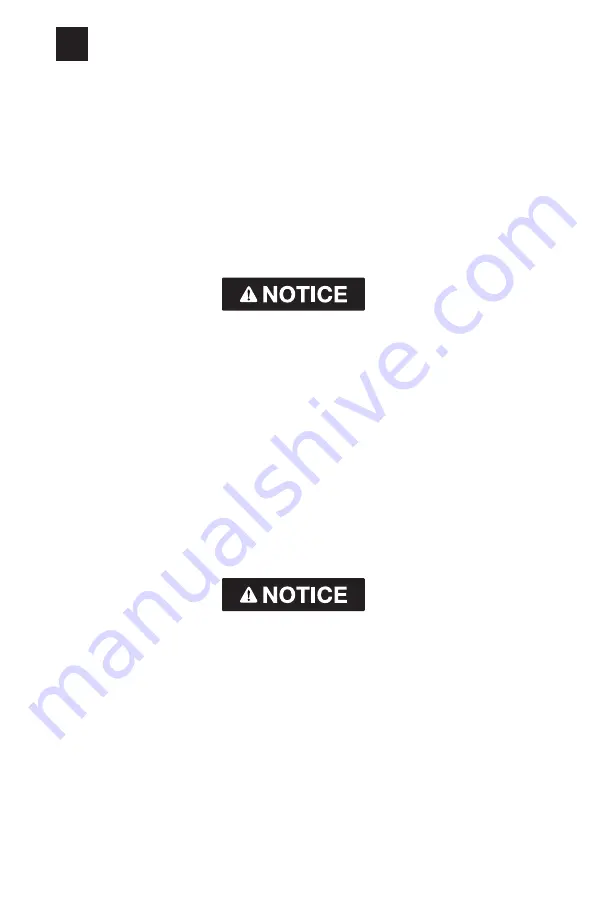
PowerLift by ReechCraft
52
All decals must be mounted to the machine as specified and clearly legible.
Please see Figure 5.0 and Table 5.0 for decal positions and ReechCraft part numbers.
To replace a damaged decal, first remove it completely without damaging the underlying
surface. Remove any remaining adhesive with a suitable solvent. Test the solvent on an
inconspicuous area first to ensure it does not mark or damage the surface finish.
SURFACE DAMAGE COULD RESULT IN CORROSION AND STRUCTURAL DAMAGE.
EACH MAST SECTION SHOULD BE INSPECTED EVERY THREE MONTHS OR MORE
FREQUENTLY DEPENDING ON THE ENVIRONMENT.
Each mast track section should be inspected more frequently if used in a harsh
environment or high duty cycle applications. Inspections should be more frequent as
the mast tracks approach the end of their useful lives. The periodic inspection shall cover
all mast tracks on the machine. Mast tracks sections must be replaced by an authorized
ReechCraft service center.
Conditions such as the following shall be a sufficient reason for questioning continued use
of the machine or increasing the frequency of inspection.
6.4
Decal Replacement
6.5
Mast Track Inspection Procedure
• Before applying the new decal, ensure the surface is clean and dry.
• Remove the backing paper, apply the decal along one edge, then seal it gently
and evenly.
• If there are any air bubbles, work them gently towards the edge with a clean cloth.
• Pressure sensitive adhesives reach full strength after several days.
S MAINTENANCE
SECTION
6