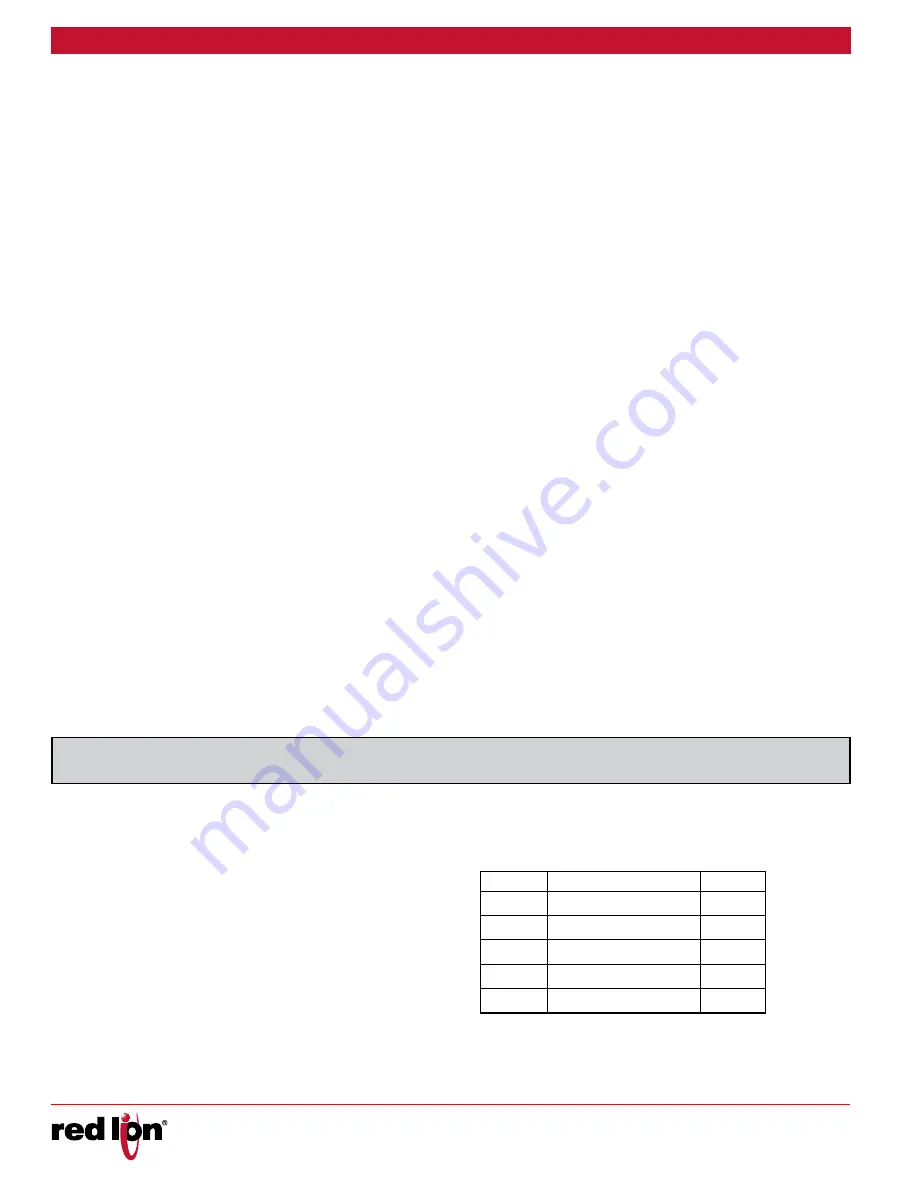
-36-
Drawing No. LP0932
Released 2018-01-12
TIME PROPORTIONAL PID CONTROL
In Time Proportional applications, the output power is converted into
output On time using the Cycle Time. For example, with a four second
cycle time and 75% power, the output will be on for three seconds (4 ×
0.75) and off for one second.
The Cycle Time should be no greater than 1/10 of the natural period
of oscillation for the process. The natural period is the time it takes for
one complete oscillation when the process is in a continuously oscillating
state.
LINEAR PID CONTROL
In Linear PID Control applications, OP1 provides a linear output signal
that is proportional to the calculated OP1 value (% Output Power). The
PXU allows the user to program the %OP value at which the analog low
(
An1L
) and high (
An1
) output signal will be produced. The Analog Output
will then be proportional to the PID calculated % output power. For
example, with 0 to 10 VDC output configured as 0 (
An1L
) to 100 (
An1
) an
OP1 value of 75% provides an analog output of 7.5 VDC. Cycle Time will
determine the update time of the linear ouput signal.
PID GROUP
The PXU allows for use of up to 6 different groups of PID parameters.
These are designated as PID Groups 1-6, as selected by the PID Group
Selection parameter,
PId
.
PId
=
1-6
: The desired PID set is explicitly selected by the PID Group
Selection parameter via a Line 2 menu entry.
PId
=
Auo
: In this mode of operation, the PID Group is automatically
selected. PID Groups 1-6 are linked to the Reference Setpoints SP1-
SP6. The setpoints are used as reference values in order to determine
which PID set is to be used. When the Actual Setpoint Line 2
parameter (
P
) is changed (keyed in or by a running Profile), the PXU
will calculate which Reference Setpoint value is closest to the Actual
Setpoint, and will use the corresponding PID Group constants and
perform a bump-less transfer to the new PID constants.
If for example, a user wants to utilize two sets of PID parameters, one
for low PV values, and one for high PV values,
P1
would be set to a low
process value, and
P2
set to the higher process value. The PXU would
be auto-tuned at both of these setpoints to calculate the PID Group 1 &
2 settings. As the actual setpoint (
P
) is changed, the controller will
identify the Reference Setpoint with the closest setpoint, and use its PID
constants.
AUTOMATIC CONTROL MODE
In Automatic Control Mode, the percentage of output power is
automatically determined by PID or On/Off calculations based on the
setpoint and process feedback. For this reason, PID Control and On/Off
Control always imply Automatic Control Mode.
MANUAL CONTROL MODE
In
r
Control Mode, the controller operates as an open loop system,
and does not use the setpoint or process feedback. The user adjusts the
percentage of power through the OP1 or OP2 parameter to control the
power for each Output. The Low and High Output Power limits are
ignored when the controller is in Manual.
MODE TRANSFER
When transferring the controller mode between Automatic and User/
Manual, the controlling outputs remain constant, exercising true
“bumpless” transfer. When transferring from Manual to Automatic, the
power initially remains steady, but Integral Action corrects (if necessary)
the closed loop power demand at a rate proportional to the Integral Time.
PID Tuning Explanations
AUTO-TUNE
Auto-Tune is a user-initiated function that allows the controller to
automatically determine the Proportional Band, Integral Time, Derivative
Time, Integration Default, and Relative Gain (Heat/Cool) values based
upon the process characteristics. The Auto-Tune operation cycles the
controlling output(s) at the setpoint. The nature of these oscillations
determines the settings for the controller’s parameters.
Prior to initiating Auto-Tune, it is important that the controller and
system be first tested. This can be accomplished in On/Off Control or
Manual Control Mode. If there is a wiring, system or controller problem,
Auto-Tune may give incorrect tuning or may never finish. Auto-Tune may
be initiated at start-up, from setpoint or at any other process point.
However, ensure normal process conditions (example: minimize unusual
external load disturbances) as they will have an effect on the PID
calculations.
Start Auto-Tune
Below are the parameters that affect Auto-Tune. Minimally, these
settings should be configured before initiating Auto-Tune. In order to
initiate Auto-Tune,
N
must be configured as
Id
in Module
3-LC
.
DISPLAY
PARAMETER
MODULE
YP
Input Type
1-IN
OPAC
Control Action
2-OP
CY
On/Off Control Hysteresis
2-OP
N
Auto-Tune Access
3-LC
P
Setpoint
3-LC
1. Enter the Setpoint value in the Display Loop.
2. Set the On/Off Control Hysteresis (
CY
) to a value that is appropriate
for the process.
3. Initiate Auto-Tune by changing
N
to
Y
in the Hidden Loop, and then
press
:
.