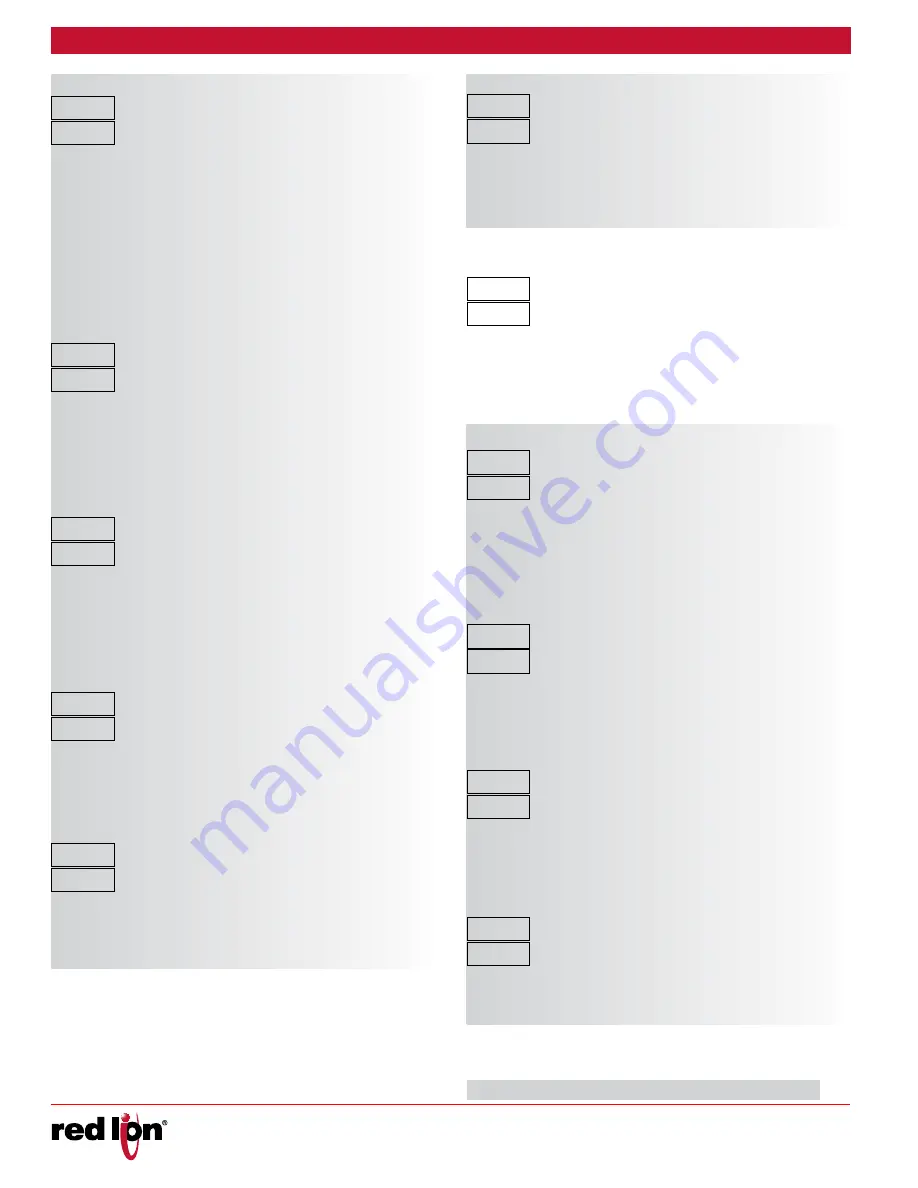
-22-
Drawing No. LP0932
Released 2018-01-12
RELATIVE GAIN
0.01
to
99.99
This defines the gain of
OP2
relative to
OP1
. It is generally set to balance
the effects of cooling to that of heating(
r1d2
) or vice versa (
d1r2
). This is
illustrated in the Heat/Cool Relative Gain Figures below. After completion
of Auto-Tune, this parameter will be changed.
DEADBAND/OVERLAP
-99.9
to
999.9
This defines the deadband area between the bands (positive value)
or the overlap area in which both heating and cooling are active
(negative value). If a heat/cool overlap is specified, the percent output
power is the sum of the heat power and the cool power. The function of
Deadband/Overlap is illustrated in the Control Mode Explanations.
1.00
gAN2
2.0
db-2
OUTPUT 2 POWER LOWER LIMIT
0.0
to
100.0
%
This parameter may be used to limit controller power at the lower end
due to process disturbances or setpoint changes. Enter the safe output
2 low power limit for the process. When the controller is in
r
or
OnOF
Control Mode, this limit does not apply.
OUTPUT 2 POWER UPPER LIMIT
0.0
to
100.0
%
This parameter may be used to limit controller power at the upper end
due to process disturbances or setpoint changes. Enter the safe output
2 high power limit for the process. When the controller is in
r
or
OnOF
Control Mode, this limit does not apply.
INPUT FAIL OP2 POWER LEVEL
This parameter sets the power level in the event of an input failure
(open TC/RTD or shorted RTD). Manual (
r
) Control overrides the
input fail preset.
0.0
to
100.0
%
ON/OFF CONTROL HYSTERESIS
2
to
250
The On/Off Control Hysteresis (balanced around the setpoint)
eliminates output chatter. The control hysteresis value affects both OP1
and OP2 control. The hysteresis band has no effect on PID Control. On/
Off Control Hysteresis is illustrated in the Control Mode explanations.
0.0
OP2L
100.0
OP2
0.0
IF02
2.0
CY
Shaded parameters are programming/model dependent.
OP2 CYCLE TIME
0.0
to
250.0
seconds
The Cycle Time is entered in seconds with one tenth of a second
resolution. It is the total time for one on and one off period of an OP2 time
proportioning control output. With time proportional control, the percentage
of power is converted into an output on-time relative to the cycle time
value set. (If the controller calculates that 65% power is required and a
cycle time of 10.0 seconds is set, the output is on for 6.5 seconds and off
for 3.5 seconds.) For best control, a cycle time equal to one-tenth or less,
of the natural period of oscillation of the process is recommended. When
OP2 is an analog output, the Cycle Time is the analog output update time.
A Cycle Time selection of 0.0 disables the output.
2.0
CYC2
ANALOG OUTPUT (RETRANS) ASSIGNMENT
This setting selects the parameter that the Analog Output retransmits
or tracks.
INP
ANA
ANALOG UPDATE TIME
0
to
250
seconds
The update time of the Analog Output reduces excess valve actuator
or pen recorder activity.
1.0
AN
ANALOG LOW SCALING
-99.9
to
999.9
The Analog Output assignment value that corresponds to 4 mA
output.
0.0
ANLO
ANALOG HIGH SCALING
-99.9
to
999.9
The Analog Output assignment value that corresponds to 20 mA
output. An inverse acting output can be achieved by reversing the low
and high scaling points.
100.0
ANI
OP1
%Power of Control Output 1
OP2
%Power of Control Output 2
P
Active Setpoint value
INP
Input value