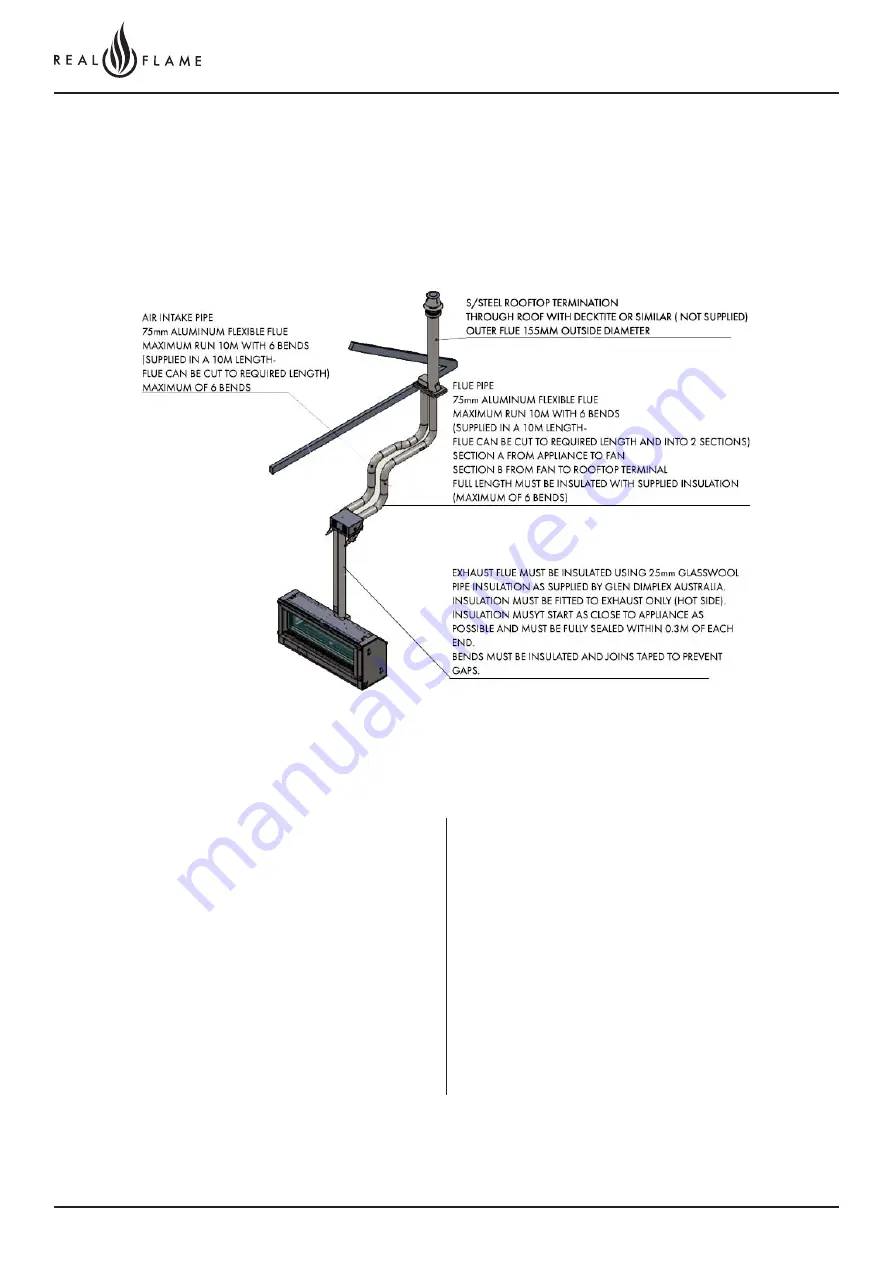
52
Page
FLUE TERMINATION LOCATIONS
This section is used to determine where your Balanced
Flue termination will be located.
Flue terminations shall not be recessed in walls or sidings.
EXTREMELY IMPORTANT
• In heavy snow areas take extra care to prevent
blocking flue termination with snow removal
equipment.
• Flue gases exiting flue terminals are very hot and must
not be restricted to assure fireplace combustion is not
affected.
• Do not place, build any obstruction, plant any
bushes or for any reason attempt to conceal the flue
termination. To do so will affect the operation of the
fireplace and may be hazardous.
• This unit must always vent directly to outdoors.
Flue runs 5m to 10m length roof top termination only
Vertical roof termination (S/Steel rooftop termination)
Summary of Contents for Element 1200 MARK 2
Page 6: ...6 Page OPERATION INSTRUCTIONS ...
Page 20: ...20 Page IN STALL ATION INSTRUCTIONS ...
Page 26: ...26 Page 0 5M FLUE CONFIGURATION ...
Page 30: ...30 Page Flue runs 0m to 5m length rooftop termination with external motor ...
Page 34: ...34 Page 0M 5M FLUE INTERNAL FAN AND WALL TERMINATION INSTALL ATION ...
Page 42: ...42 Page INTERNAL FAN ROOF TERMINATION ...
Page 46: ...46 Page ROOFTOP TERMINATION WITH EXTERNAL MOTOR ...
Page 49: ...49 Page 5 10M INSUL ATED FLUE CONFIGURATION ...
Page 77: ...77 Page 10 13 5M POLYPROPYLENE FLUE CONFIGURATION ...
Page 81: ...81 Page ...
Page 89: ...89 Page Connect power cable connector Fit cable clamp to cable Fit front cover ...
Page 98: ...98 Page 10 13 5M ROOFTOP POLYPROPYLENE FLUE CONFIGURATION ...
Page 102: ...102 Page ...
Page 103: ...103 Page SET UP WITH IN LINE OR APPLIANCE MOUNTED FAN ...