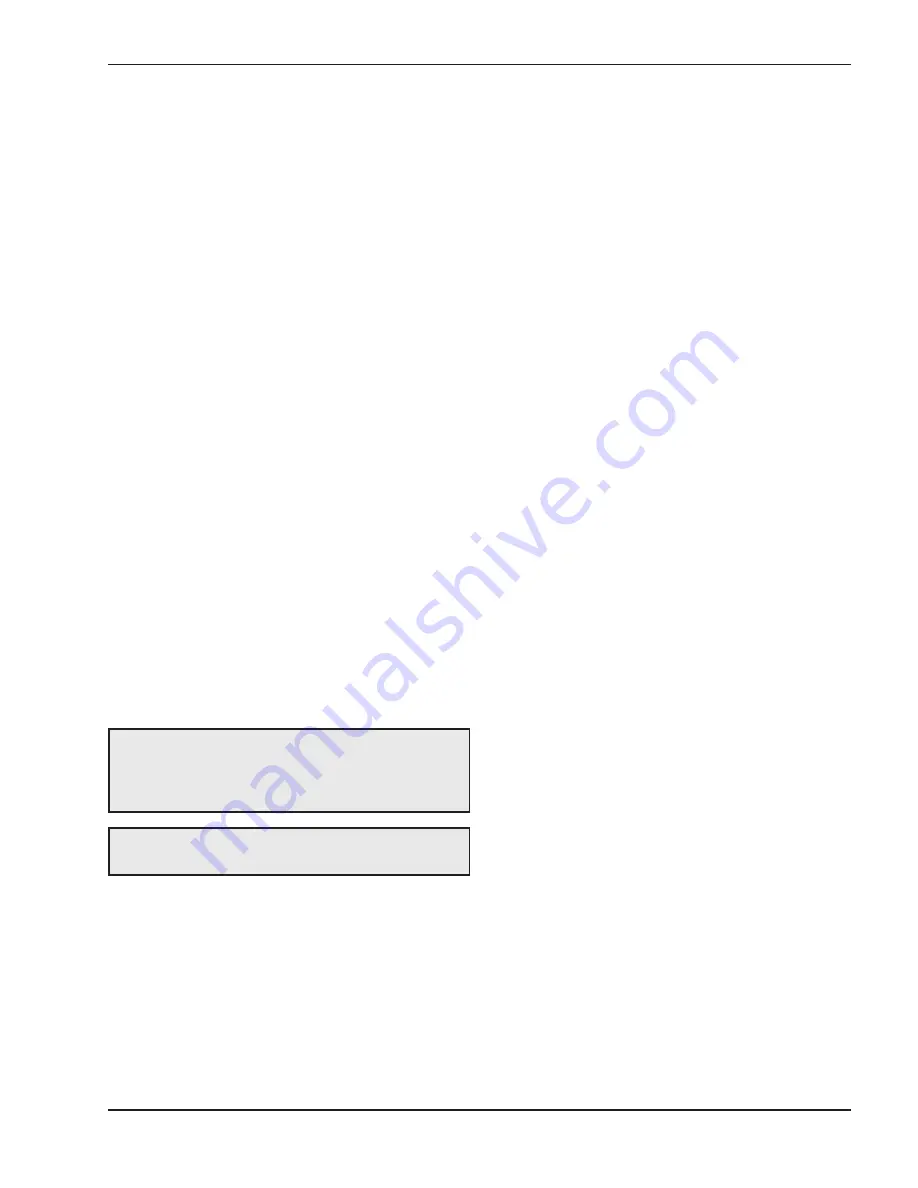
29
Wiring the Indirect Sensor
1. An indirect sensor connection is not required if an
indirect water heater is not used in the installation.
2. When the Indirect DHW call for heat is active, the
PIM communicates this to the VERSA. The
VERSA calculates the optimal operation and
sends the firing rate and pump output requests to
the PIM so it can activate the Indirect DHW pump
and Boiler pump as needed. If an optional Indirect
DHW sensor is connected, the PIM will pass this
signal to the VERSA. This allows the VERSA to
optimize the Indirect DHW demand to maintain the
Indirect DHW setpoint. The Indirect DHW thermo-
stat switch closure is still required when using the
Indirect DHW sensor. If a VERSA is not present
the PIM shall activate the Indirect DHW pump
whenever the Indirect DHW call is active. The
Boiler pump will also be activated based on the
Indirect DHW piping configuration setting. Consult
the VERSA IC manual (Cat. 5000.72) for addition-
al configurations.
3. Connect the indirect tank sensor to the terminals
marked INDIRECT DHW SENSOR (see wiring
diagram). Caution should be used to ensure nei-
ther of these terminals becomes connected to
ground. When using an indirect DHW sensor to
control tank temperature contact closure is
required across the indirect override connections
for proper operation during “limp along” mode set
PIM operator dial to be equal to DHW Target tem-
perature to prevent an over temperature condition
from occuring.
Wiring the Optional 0–10 Volt
Building Control Signal
1. A signal from an energy management system may
be connected to the Hi Delta boiler. This signal
should be a 0-10 volt positive DC signal, and an
energy management system can be used to con-
trol either the setpoint temperature of a single Hi
Delta or a cascade of up to 4 boilers, or the firing
rate of a single Hi Delta boiler.
NOTE:
Alternately, a thermostat contact closure can
be used in lieu of the sensor for indirect operation.
Connect the thermostat to the terminals marked
INDIRECT DHW OVERIDE.
CAUTION:
Sensor and control wiring must
NOT
be
run in conduit or chases with line voltage.
2. To enable this remote control function, set dip
switch 5 to the UP position on the PIM. DIP switch
5 Toggles between an EMS (UP) signal or a
demand signal from the VERSA (DOWN). DIP
switch 2 on the PIM toggles between a Direct
Drive (UP) input and a Target Temperature
(DOWN) setpoint.
3. For a 4-20mA application, refer to the VERSA IC
manual (Cat. 5000.72).
4. Connect an Energy Management system or other
auxiliary control signal to the terminals marked 0-
10V (+ /-) on the field wiring terminals (see
Fig. 30). Caution should be used to ensure that the
+0-10V connection does not create a short to
ground.
Wiring the Cascade System
Communication Bus
1. Designate the primary boiler as the master
boiler/boiler1 by leaving DIP switch 2 on the
VERSA in the ON position. All other VERSA con-
trols require DIP switch 2 to be toggled OFF,
designating them as followers. Follower VERSA
boards are ignored by their corresponding PIM
modules. Use strandard 18 AWG wire to connect
the master VERSA to the PIM on the followers. A
total of 3 followers can be connected to the
VERSA on the master. For systems requiring more
than 4 connected boilers, an external sequencer
such as the Raypak Temp Tracker Mod+ Hybrid
can be used.
2. It is recommended that the shortest length cable
possible be used to reach between the boilers. Do
not run unprotected cables across the floor or
where they will become wet or damaged. Do not
run communication cables parallel with, or close to
or against, high voltage (120 volt or greater)
wiring. Raypak recommends that the total maxi-
mum length of each set of communication bus
cables not exceed 200 feet.
3. Connect the FT_BUS wires to the PIM by pressing
down on the slots with a small screwdriver and
then inserting the wires into the holes. See
Fig. 33.
Summary of Contents for 992C
Page 54: ...54 Wiring Diagram Models 992C 1262C...
Page 55: ...55 Wiring Diagram Models 1532C 2342C...
Page 69: ...69...
Page 70: ...70...
Page 71: ...71...