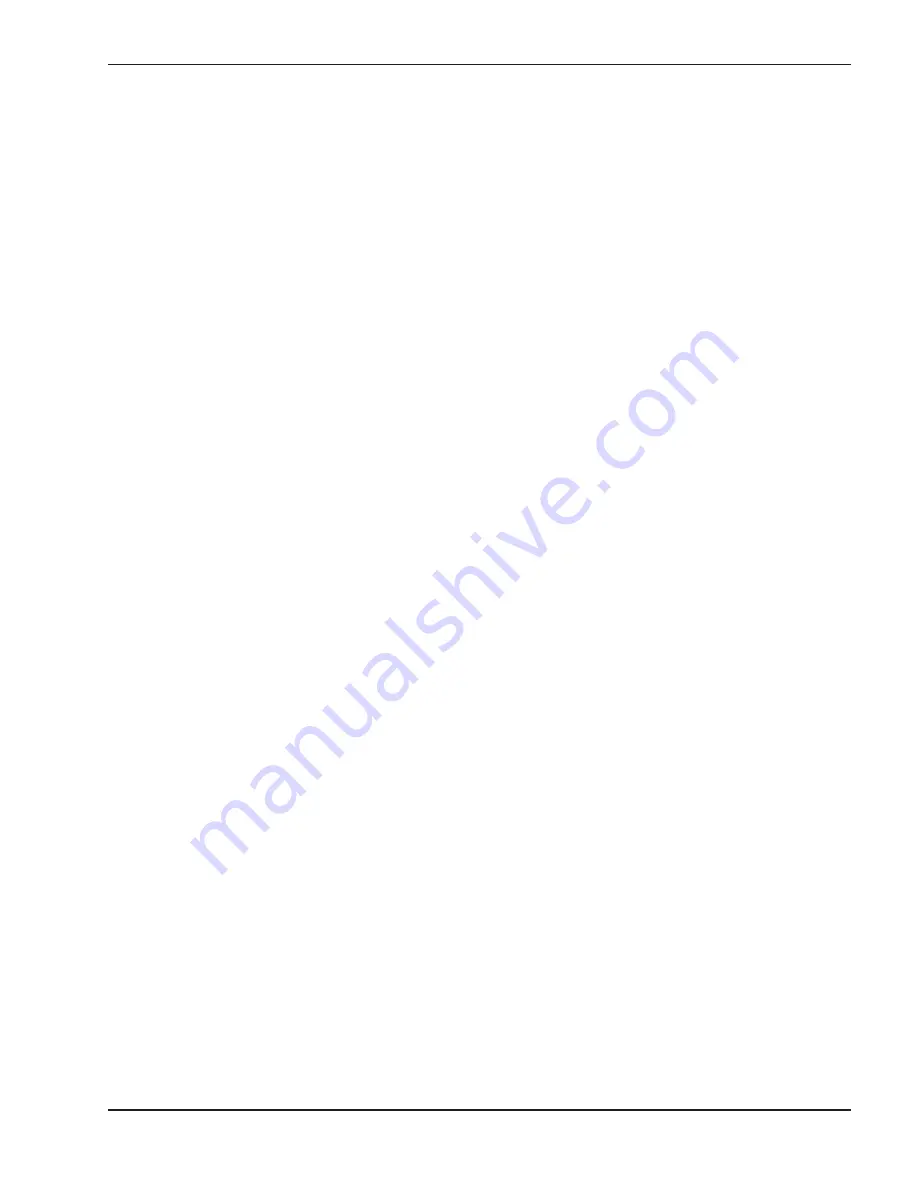
41
3. The PIM confirms the presence of a valid ID Card
which matches the configuration stored in memory
at the factory. If a valid ID Card is NOT present,
the PIM generates a diagnostic fault and will shut
down waiting for this fault to be addressed.
4. The PIM reads the DIP switch settings and config-
ures itself for the desired operation.
5. The PIM scans the Ft_bus communications for the
VERSA IC Control and if found, system operation
is controlled by the VERSA IC Control.
6. Non-volatile memory is checked for any active
lockout conditions. If any exist, they must be
addressed before the PIM will allow a new trial for
ignition to start.
7. The PIM continually monitors the flame status to
ensure that no flame is present during standby. If
an erroneous flame is detected, the PIM gener-
ates a False Flame error fault.
8. A Call-for-heat is initiated by the presence of any
one or more of the 4 sources below:
a. A heat demand (contact closure) on the TH
field wiring terminals.
b. A voltage greater than 0.5 VDC on the analog
0-10 VDC EMS signal input.
c. A heat demand present on the DHW field
wiring terminals.
d. A heat demand from the VERSA IC control
based on the DHW sensor temperature.
9. The PIM initiates a trial for ignition counter to the
programmed number of trials for ignition (1 or mul-
tiple) and proceeds to Pump Purge mode.
10. The VERSA IC Control will turn on the system,
boiler and/or DHW pump as necessary to address
the call-for-heat. This is dependent on the Mode of
operation selected. The pumps will proceed
through their purge period before the control will
move into a Trial for Ignition (TFI). For systems
with CWP enabled, the MIX output is sent to the
MIX MIN % value.
11. The VERSA Control Board and PIM check the
safety circuit and will stop from going into a trial for
ignition if any of the safety devices is in an
error/fault condition.
12. If no fault condition is found, the air pressure
switch (if present) is verified to be in the open
position before the blower is energized.
13. The blower(s) are energized.
14. The air pressure switches are verified closed with-
in 60 seconds to prove air flow.
15. Once the air pressure switches close, the blower
proceeds to pre-purge for the specified period.
16. The voltage level of the 24VAC supply input is
confirmed to be above 18.0VAC – if not, a Low
Voltage fault will be recorded and the heater will
go into a soft lockout condition until the voltage
rises above 18.0VAC consistently.
17. If all checks have passed, the system proceeds to
ignition.
18. The PIM re-initializes the ignition counter to the
configured number of trials (typically 1 or 3).
19. The Hi Limit sensor is confirmed to read below the
Hi Limit setpoint.
20. The gas valve relay contacts are verified open – if
closed, a fault code will be issued and the heater
will post-purge and go into a hard lockout condi-
tion.
21. The Hi-Delta units are equipped with a Hot
Surface Igniter:
a. The control turns on the HSI and the HSI prov-
ing current is verified to be above the
configured value.
b. The configured heat-up delay takes place to
allow the HSI element to reach ignition tem-
perature.
c. The gas valve output is energized for the trial-
for-ignition time to light the burner.
d. The HSI is de-energized during the last sec-
ond of the trial-for-ignition period to sense for
the burner flame.
e. The flame sense is checked for successful
lighting of the burner. If a valid flame is detect-
ed, the main gas valve, operating pumps and
blower relay remain energized and the PIM
proceeds to the Heating mode.
Summary of Contents for 992C
Page 54: ...54 Wiring Diagram Models 992C 1262C...
Page 55: ...55 Wiring Diagram Models 1532C 2342C...
Page 69: ...69...
Page 70: ...70...
Page 71: ...71...