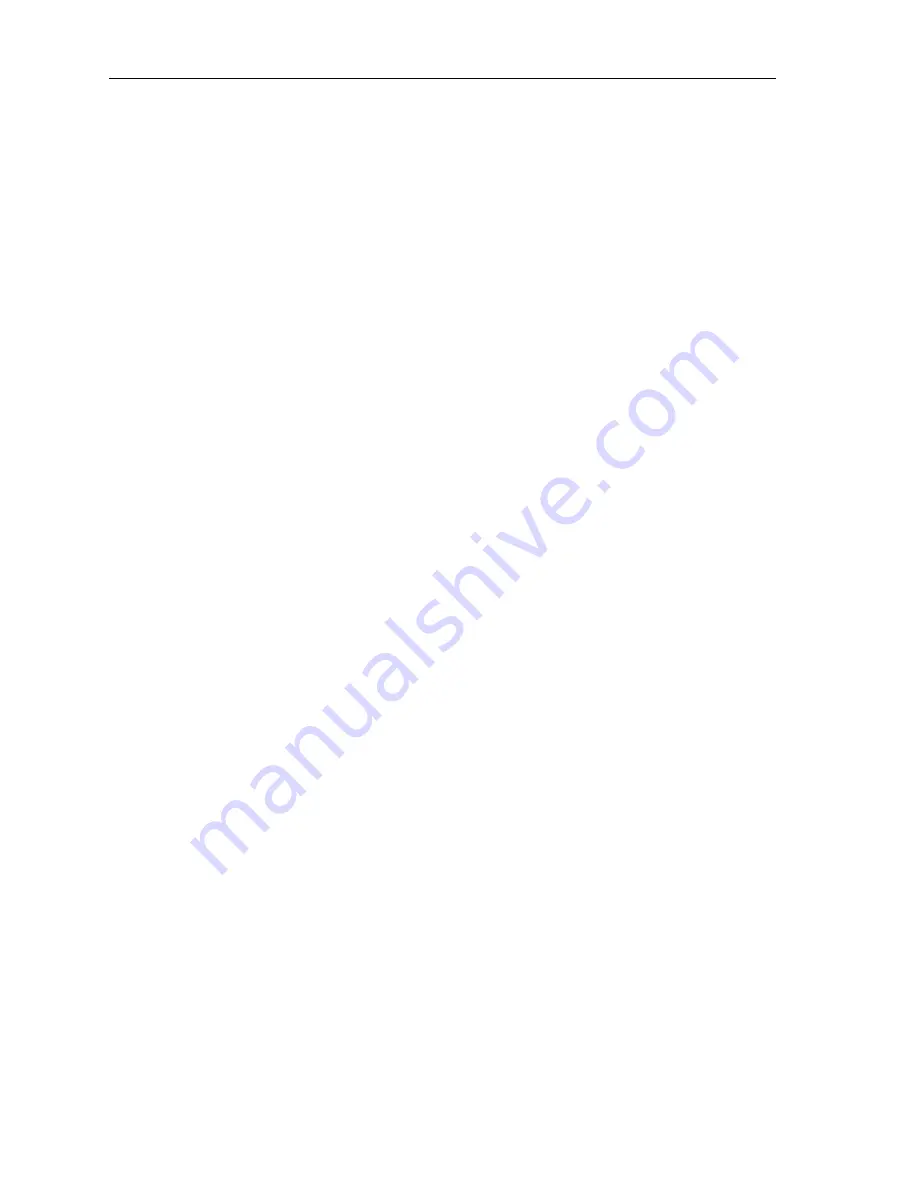
48
DSM300 Installation Manual
Installation in a Cored Fiberglass Hull
The core (wood or foam) must be cut and sealed carefully. The core must be
protected from water seepage and the hull must be reinforced to prevent it from
crushing under the hull nut, allowing the housing to become loose.
CAUTION:
Always wear safety goggles and a dust mask when drilling.
1. Drill a 1/8" (3 mm) pilot hole perpendicular to the waterline from inside the
hull. If there is a rib or strut near the selected mounting location, drill from the
outside (see Figure 2-16 ). If the hole is drilled in the wrong location, drill a sec-
ond hole in a better location. Apply masking tape to the outside of the hull
over the incorrect hole and fill it with epoxy.
2. Using a 2" (51 mm) hole saw, cut a hole from outside the hull through the
outer skin only.
3. Using the 2 3/8" (60 mm) hole saw, cut through the inner skin and most of the
core from inside the hull. The core material can be very soft. Apply only light
pressure to the hole saw after cutting through the inner skin to avoid acciden-
tally cutting the outer skin
Note:
The optimal interior hole diameter is affected by the hull’s thickness and deadrise
angle. It must be large enough in diameter to allow the core to be completely sealed.
4. Remove the plug of core material so the inside of the outer skin and inner core
of the hull is fully exposed. Clean and/or sand the inner skin, core, and the
outer skin around the hole.
CAUTION:
Completely seal the hull to prevent water seepage into the core.
5. Coat a hollow or solid cylinder of the correct diameter with wax and tape it in
place. Fill the gap between the cylinder and hull with casting epoxy. After the
epoxy has set, remove the cylinder (see Figure 2-17 ).