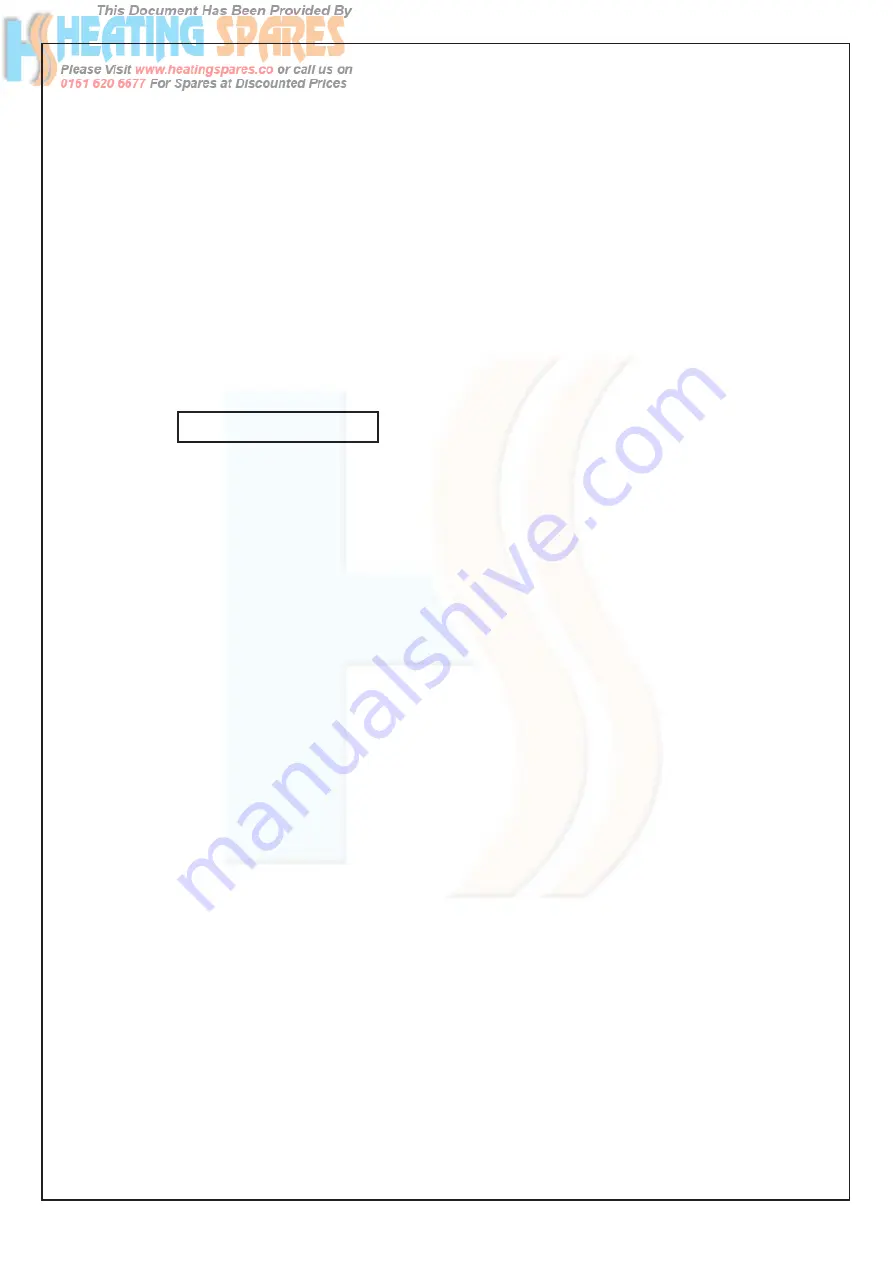
Supplied By www.heating spares.co Tel. 0161 620 6677
3
HIGH EFFICENCY
CONDENSING SYSTEM INNOVATION AUTOMATIC MODULATING BOILER
FOR CENTRAL HEATING AND DOMESTIC HOT WATER
This new super high effi cient turbo-modulating boiler is designed to meet domestic hot water and central heating requirements
at super high effi ciency, unheard of only a few years ago.
POSITION
The appliance is extremely versatile as it can be fi tted in almost any room. The appliance is room sealed, there is no contact
between combustion chamber and living accommodation. This guarantees maximum safety and effi ciency. Indeed, our
depression/combustion front cover has been designed to fi t, achieving maximum air tight seal using screw down fasteners at
15 cm. This should not hinder service of the appliance, but does ensure maximum effi ciency and safety - something which we
at Ravenheat take great pride in.
Each boiler has been designed and manufactured in our modern plant to exacting ISO 9001 discipline, all boilers carry full CE
marking of approval. Technical sales and commercial service are available throughout the UK. This product is guaranteed by
Ravenheat Manufacturing, Chartists Way, Morley, LEEDS, LS27 9ET. Telephone No (0113) 252 7007.
BASIC COMPONENTS - (See fi gure 1)
Guarantee is a full 12 months from date of purchase providing the appliance has been fi tted in accordance with these instructions
and relevant codes of practice.
- Gas
valve.
-
Variable head pump suitable for any type of central heating system.
- Burner
with
fl ame stabiliser designed to operate under all thermal conditions.
-
Primary heat exchanger constructed from stainless steel.
- Unique
patented condensing heat exchanger
for high thermal fl ue transfer gases to water.
-
Stainless steel plate heat exchanger for super high heat transfer to domestic hot water.
-
Highly reliable diverter valve with ethylene propylene diaphragm permitting primary fl ow circulation
in the boiler during domestic hot water supply.
-
Built in frost protection.
-
Printed circuit board designed to connect to room stat and/or timer/frost stat. Aesthetically pleasing
panels and controls.
-
On/Off ball valves for shutting off gas central heating and domestic hot water circuit Safety relief
valve (for safety discharge).
Programmable 7 day module with digital display (optional model).
All front panel controls not often used have been hidden. This achieves simplicity of operation with easy to clean
panels.
NOTE: Due to the high effi ciency of this boiler a plume of water vapour will form at the fl ue
terminal during operation.
COSHH - CONTROL OF SUBSTANCES HARMFUL TO HEALTH
IMPORTANT
This appliance contains materials that are indicated below.
It is the Users/Installers responsibility to ensure that the necessary personal protective clothing is-worn when han-
dling, where applicable, the pertinent parts that contain any materials that could be interpreted as being injurious to
health and safety.
WARNING When installing the appliance, care should be taken to avoid any possibility of injury when handling sheet
metal parts.
GENERAL INFORMATION:
GLUES AND SEALANTS - exercise caution - if these are still in liquid form.
INSULATION PADS, CERAMIC FIBRE - may be harmful if inhaled, may be irritating to skin, eyes, nose and throat.
When handling keep dust generation to a minimum, avoid inhaling and contact with skin or eyes.
When disposing of the product keep dust generation to a minimum and ensure that parts are securely wrapped.
When servicing avoid inhalation by using a vacuum cleaner or in conjunction with other tools. After handling wash
hands and other exposed parts.
RAVENHEAT use only high quality material for production of this product, in an effort to protect the environment
components should be re-cycled.
MAJOR COMPONENTS