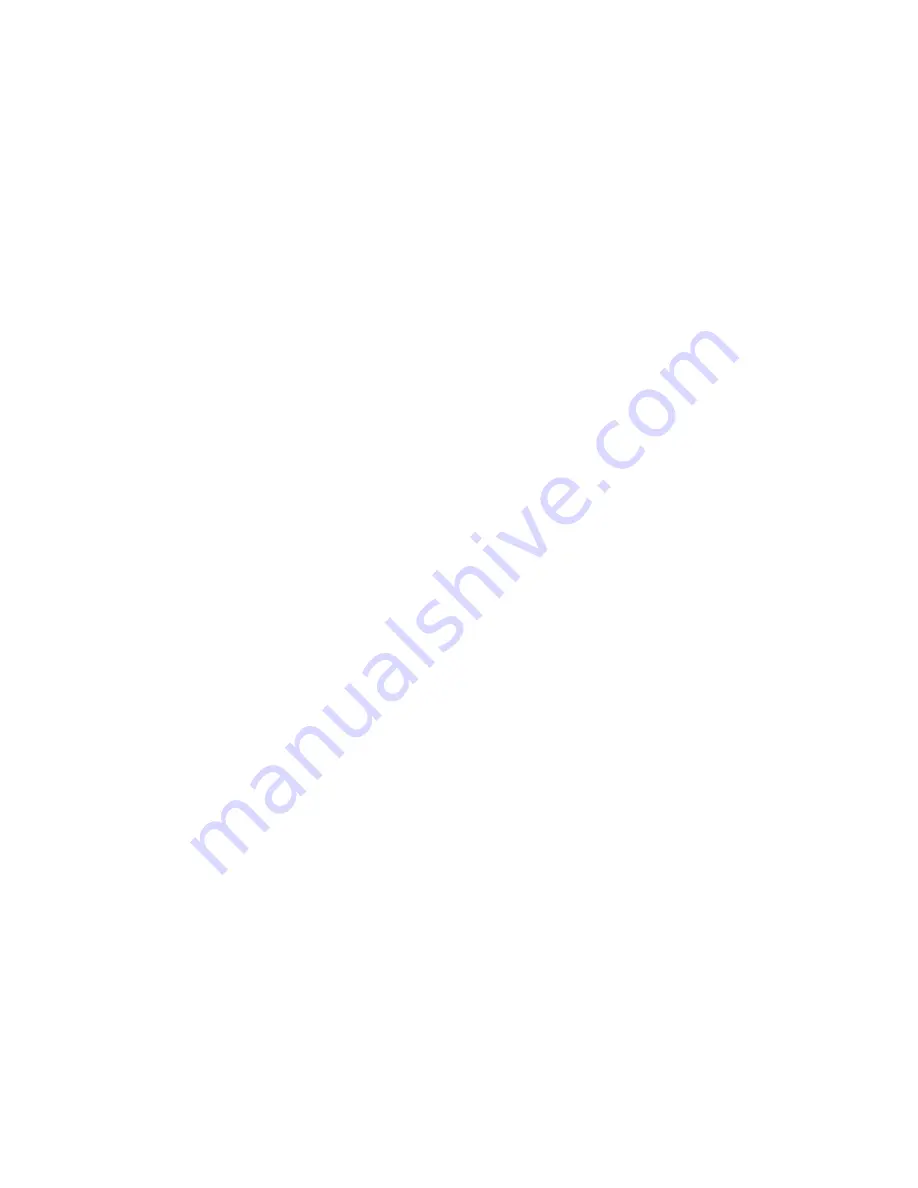
41
INTRODUCTION
Controller Area Network, or CAN, is a high-integrity serial data communications bus for real-time control
applications. CAN messaging within the agriculture industry operates at a data rate of 250 kilobits per
second. The CAN protocol also has excellent error detection and error confinement capabilities, making
it very suitable and reliable for agriculture applications.
CAN applications allow for additional products to easily be added to a control system at any time. The
SCS 4600 allows for up to three products in the control system (two additional via the CAN bus). The
products may be any combination of liquid, granular, chemical injection, or spinner control applications.
Two CAN terminators are required as means of terminating the CAN bus lines to provide optimal signal
integrity. The terminators should be located at each end of the CAN bus. CAN power, obtained from
switched power, runs throughout the bus to act as a shield.
To add products to the system, simply remove the terminator from the end of the CAN bus, tie into the
CAN bus using a “T” extension cable (Raven P/N 115-0171-326 [6’], 115-0171-362 [12’], 115-0171-363
[24’], or 115-0171-364 [6”]), provide high current power (if applicable) and logic power to the control node
using the control node cable, connect to the appropriate sensors and valves (if applicable), and replace
the terminator on the end of the CAN bus. Power to the CAN node(s) should be obtained from a switched
power source capable of handling the required current for the given node(s). The required current can be
approximated from the fuse rating of the fuse within the power leads. Relay, Raven P/N 415-1001-009
can provide up to 40 Amps and should be wired as seen in the following diagrams. The node(s) will
automatically be recognized upon reboot of the console.
Although the control algorithm, or “brains”, is located within the CAN node, all of the same troubleshoot-
ing techniques as used in a traditional hard-wired system still apply. CAN allows for modularization of the
control system, but the behavior of the system remains the same. Flow and speed sensors, as well as the
control valve and boom valves are used in the same fashion.
The following diagrams show individual control modules that can be added to a CAN system. For con-
necting multiple CAN modules, connect the modules in series and place a terminator at the end of the
CAN bus.
PROCEDURE TO READDRESS CAN PRODUCT CONTROL NODES
From CAN submenu of DATA MENU, select “PRESS ENTER TO READDRESS PROD NODES” and
press ENTER. Console will display “REBOOT NODES IN SEQNC, PRESS ENTER WHEN DONE.” At
this point, CAN product control nodes should be rebooted, or repowered, in the order they are to be
addressed. For instance, to assign Product Control Node 1, reboot the desired node first, Product Con-
trol Node 1 should be rebooted second, etc. To reboot a control node, either disconnect the power
connector to the node or pull the fuse on the logic power wire (typically the 5 Amp fuse), wait a few
seconds, then reconnect. When finished rebooting all product control nodes, press ENTER on the con-
sole to resume operation.
Summary of Contents for SCS 4600
Page 1: ...Operators Manual SCS 4600 SCS 4600 SCS 4600 SCS 4600 SCS 4600...
Page 10: ...5 THIS PAGE INTENTIONALLY LEFT BLANK...
Page 11: ...6 SECTION 1 LIQUID AND GRANULAR APPLICATIONS LIQUID AND GRANULAR APPLICATIONS...
Page 15: ...10 FIGURE 3 BATTERY CONNECTIONS LIQUID AND GRANULAR APPLICATIONS...
Page 34: ...29 FIGURE 6...
Page 37: ...32 GRANULAR APPLICATIONS SECTION 2 GRANULAR APPLICATIONS...
Page 38: ...33 FIGURE 7...
Page 44: ...39 THIS PAGE INTENTIONALLY LEFT BLANK...
Page 45: ...40 CAN APPLICATIONS SECTION 3 CONTROLLER AREA NETWORK CAN...
Page 47: ...42 CAN APPLICATIONS FIGURE 13 FIGURE 14...
Page 48: ...43 FIGURE 15...