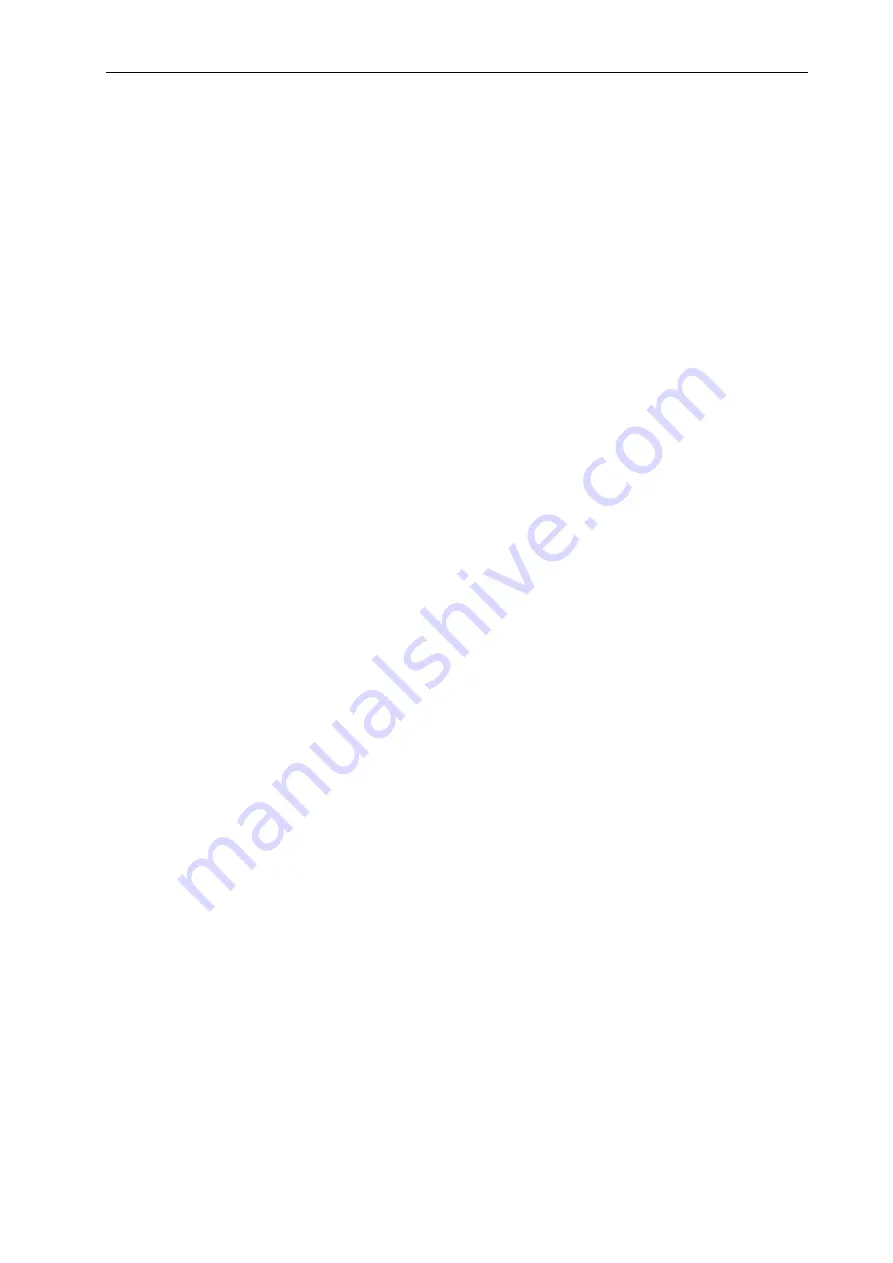
Safety
7
3
3.3
General information on the safety of the machine
The machine is constructed in accordance with the state of the art and the recog-
nized technical regulations. However, its usage and maintenance may cause
danger to the health and life of the operator or third parties and/or the impairment
of the machine and other material assets.
For this reason, the machine may only be operated
when it is in a proper and roadworthy condition,
in awareness of safety and dangers.
Therefore, it is imperative that you have read and understood the contents of the
operator’s manual. You must be familiar with the applicable accident protection
regulations and the generally accepted regulations for safety, occupational
health, and road traffic, and apply these rules as required.
3.4
Instructions for the operator
It is the operator's responsibility that the machine is used as intended.
3.4.1
Personnel qualifications
Before starting any work on or with the machine, all persons who are involved in
operation, maintenance or repair must have read and understood this operator’s
manual.
The machine may only be operated by instructed personnel authorized by the
owner.
Members of staff who are still in training or subject to coaching/instructions
may only work on the machine when an experienced person is present.
Only qualified maintenance staff may implement maintenance and service work.
3.4.2
Instruction
Distribution partners, works representatives or employees of RAUCH will instruct
the operator regarding the operation and maintenance of the machine.
The owner must ensure that newly recruited operating and maintenance person-
nel are instructed to the same extent and with the same care with regard to the
operation and repair of the machine in compliance with this operator’s manual.
Summary of Contents for AXIS H 30.2 EMC
Page 28: ...Safety 3 22...
Page 35: ...Technical data 29 4 Figure 4 6 Hydraulic motor for spreading disc drive 1 Hydraulic motor...
Page 46: ...Axle load calculation 5 40...
Page 48: ...Transportation without tractor 6 42...
Page 100: ...Spreading operation 8 94...
Page 132: ......