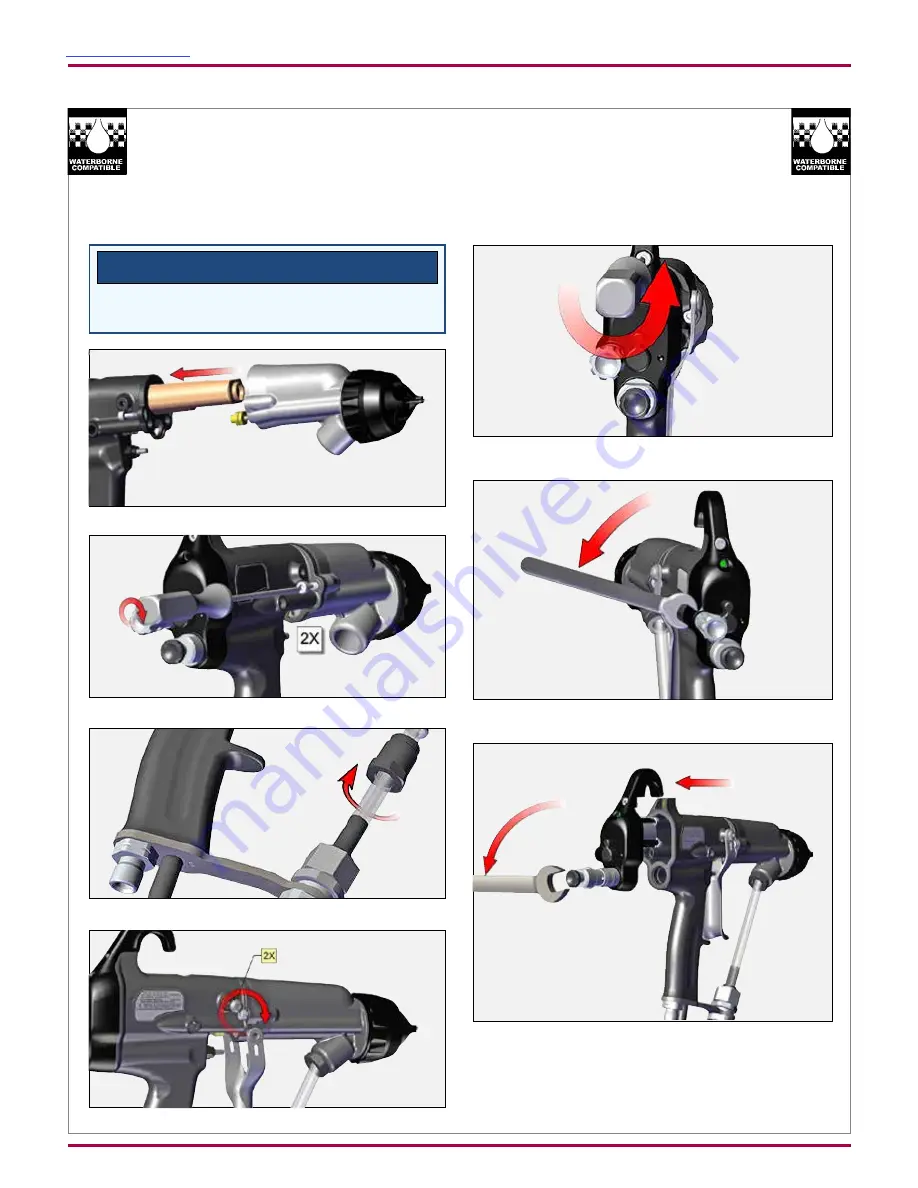
Re-Install Barrel
1. Install barrel over cascade.
2. Tighten barrel screws.
3. Re-install fluid tube.
4. Re-install trigger.
Rear Cover/Motor Module Repair
1. Loosen cover screw with 3mm driver.
2. Remove fan air cartridge with 10mm wrench.
3. Remove rear cover and cartridge with 15mm wrench.
4. Disconnect motor connector from handle wire harness
connector and remove rear cartridge.
NOTE
The gasket between the handle and barrel is reu-
seable. It should only be replaced if torn or damaged.
AH-17-04-R0.0 (11/2017)
35 / 59
www.carlisleft.com
MAINTENANCE