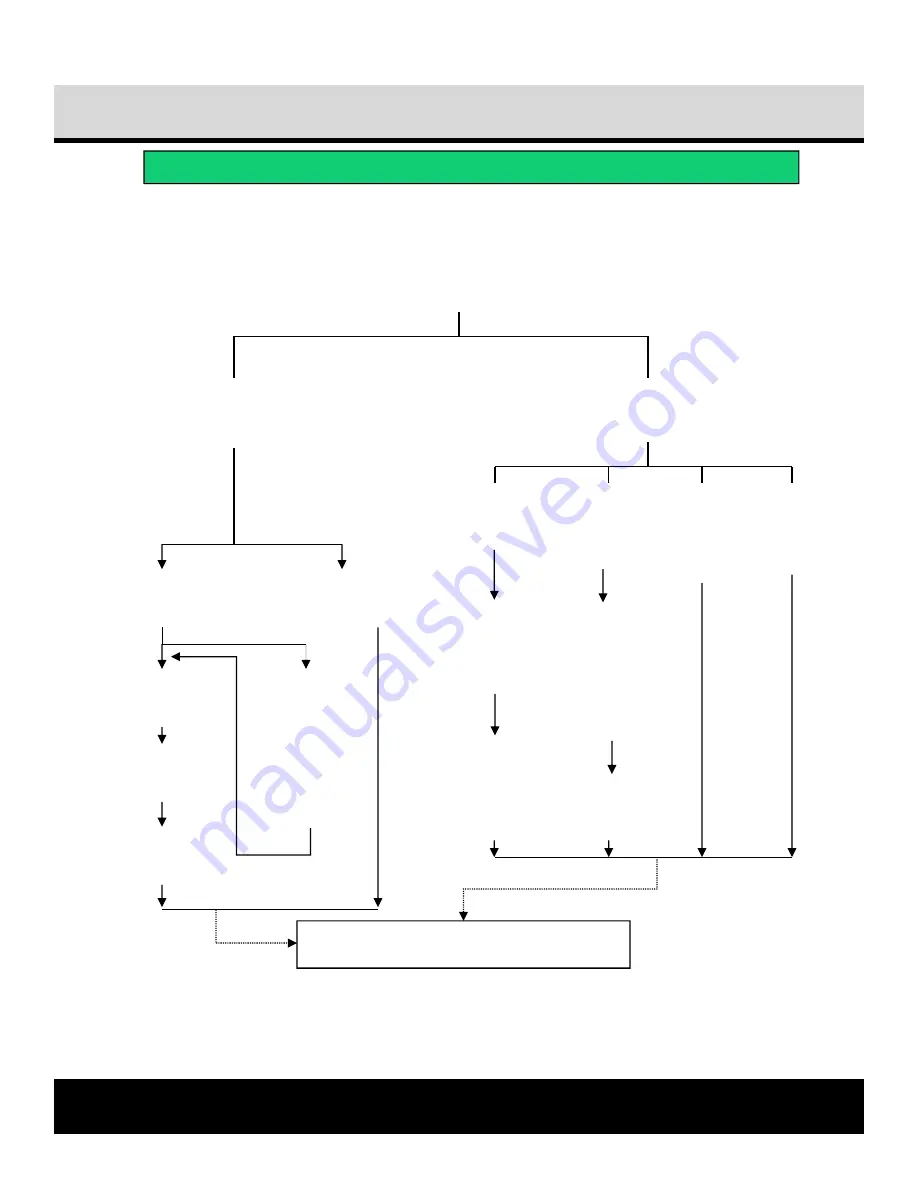
CONTINUOUS OR TOO FREQUENT BACKFLUSHES
PRESSURE BELOW THE MINIMUM
REQUIRED.
See section “Technical Data”
from the Filtration Equipment Manual
PRESSURE EQUAL OR ABOVE THE
MINIMUM REQUIRED.
See section “Technical Data”
INCORRECT
PROGRAMMING
OF THE
CONTROLLER
ACTIVATE A
BACKFLUSH AND
CHECK THE PRESSURE
IN THE OUTLET
MANIFOLD
TOO SHORT TIME
BETWEEN
BACKFLUSHES. Rise
the value. See section
“Time between
backflushes phases”
from the Control Unit
Manual
INFLUENT
WATER QUALITY
LOWER THAN
THE ESTIMATED
RUNNING FLOW
HIGHRER THAN
DESIGN
TOO SHORT OF
BACKFLUSH
DURATION. Raise the
value. See section
“Backflushing time of
each station” from the.
PROBLEM
WITH THE
DIFFERENTIAL
PRESSURE
GAUGE
CHECK THE
REGULATED
VALUE IN THE
DIFFERENTIAL
PRESSURE
GAUGE. See
section “Differential
Pressure Gauge
Delay” from the
Control Unit Manual
CHECK
CONNECTIONS OF
THE DIFFERENTIAL
PRESSURE GAUGE
If the problem persists or you have any
doubt, contact your distributor.
DOES IT HAVE A
MASTER VALVE?
CHECK THE PUMP
SYSTEM WHEN
BACKFLUSHING
THE MASTER VALVE
DOES NOT WORK
PROPERLY Check the
components of the
sustaining valve
according to section
Maintenance
Instructions
from the
Manual and the
regulation of the Relief
Pilot according to
section
Operating
Instructions
from the
Manual
CHECK THE
INSTALLATION
(POSSIBLE LEAKS)
INAPPROPRIATE
MEASURE OF THE
FEEDING PUMP
INLET FLOW
SUPERIOR TO THE
ONE ESTIMATED IN
DESIGN
YES
NO
YES
NO
19
Summary of Contents for HDF 1X2
Page 1: ...1X2...