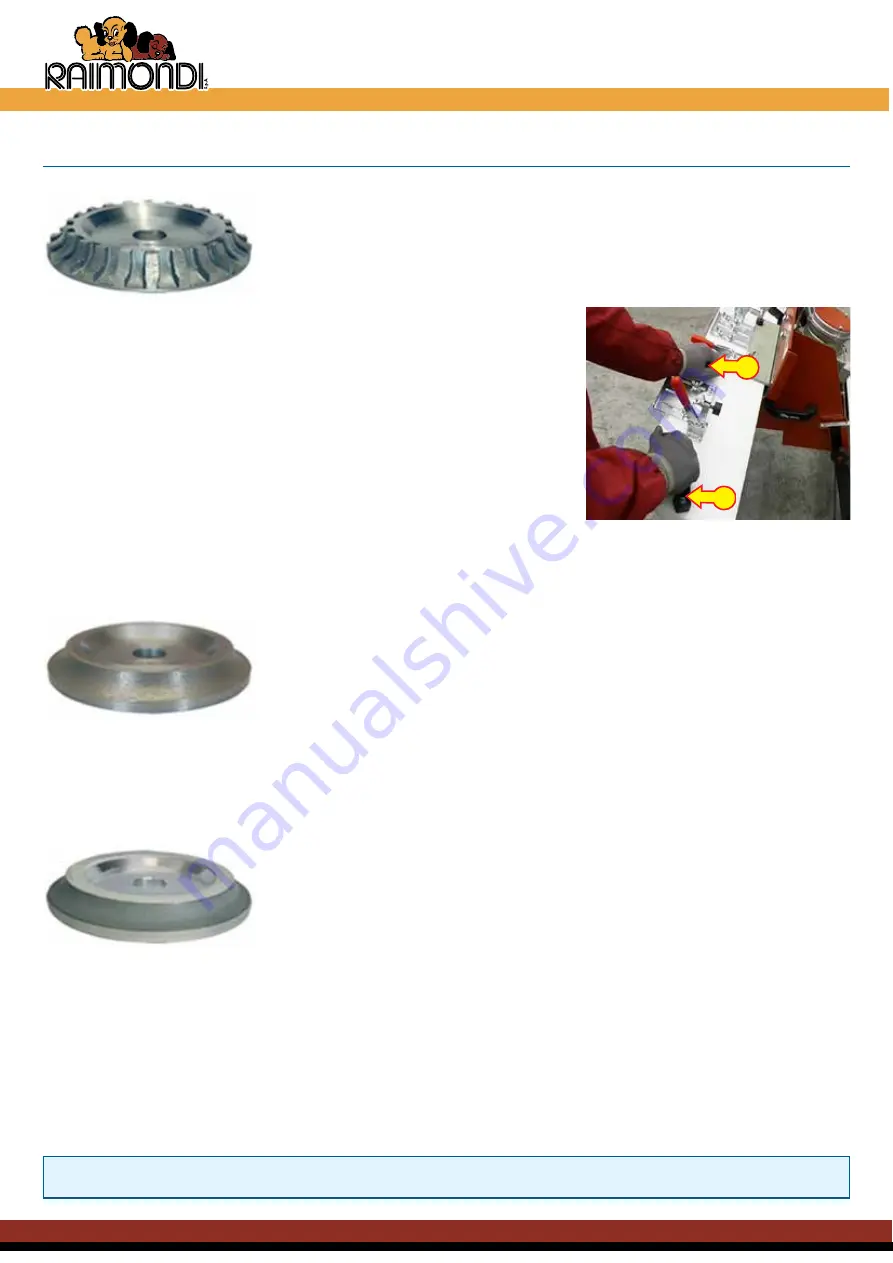
mod. BULLDOG ADV - eD. 03/2014 - s. 04
© Raimondi S.p.a.
Chapter 4
Use of the commands
Page 26/44-4
machines & tools for the tile & stone professional
4.5 half-bullnose shaping
Shaping phase (removal of the 90° angle and creation of the quarter round profile)
Suitable to cut bullnose up to 30 mm (1
3/16”
) of maximum thickness.
1)
Press the switch to turn on the machine.
2)
Wait for cooling water.
3)
Start your work grasping knob (
A
) with your left hand and handle (
B
)
on the carriage with your right.
4)
Proceed with shaping by pushing the carriage slowly forward towards
the grinding wheel.
5)
Continue the cut maintaining a constant speed.
6)
Slow down towards the end of the cut.
7)
If the materials is very hard or thick, repeat the shaping in 2 or 3 passes.
8)
Every 50 linear metres
(164’)
shaped, check condition of the grinding
wheel profile.
9)
Wear may alter the profile of the grinding wheel and lead to incorrect
Grinding / Finishing phase
To grind / finish the profile previously created with the grinding wheel:
1)
Use a grinding wheel with the same radius as that of the grinding wheel used for removal.
2)
Perfect positioning of the grinding wheel so that it copies the shape previously created.
3)
The amount of material removed should not exceed 2/10 of mm (0,008 inches).
B
Polishing phase
Before polishing, it is essential to perform the grinding / finishing operations
In order to maintain the grinding wheels in good working condition:
1)
Use a grinding wheel with the same radius as that of the grinding wheel used previously for grinding / finishing.
2)
Perfect positioning of the grinding wheel so that it copies the shape previously created.
3)
The grinding wheel must maintain minimum contact with the material. The amount of material removed should not exceed
1/100 of mm (0,00004 inches).
4)
Cooling water must be clean. Suspended dust resulting from the operations previously performed may damage the
diamond rib.
5)
The grinding wheel operating cycle is the following: 400 grain, 800 grain, 1500 grain, 1800 grain, 3500 grain.
ThE PASSAGE FrOM A GrAIN TO ANOThEr ShALL BE GrADUAL AND COMPLY WITh ThE rECOMMENDED
PrOCEDUrE.
A
shaping.This will prevent correct execution of the subsequent stages of operation, namely grinding and polishing. To
regenerate the grinding wheel profile, contact an authorised dealer.