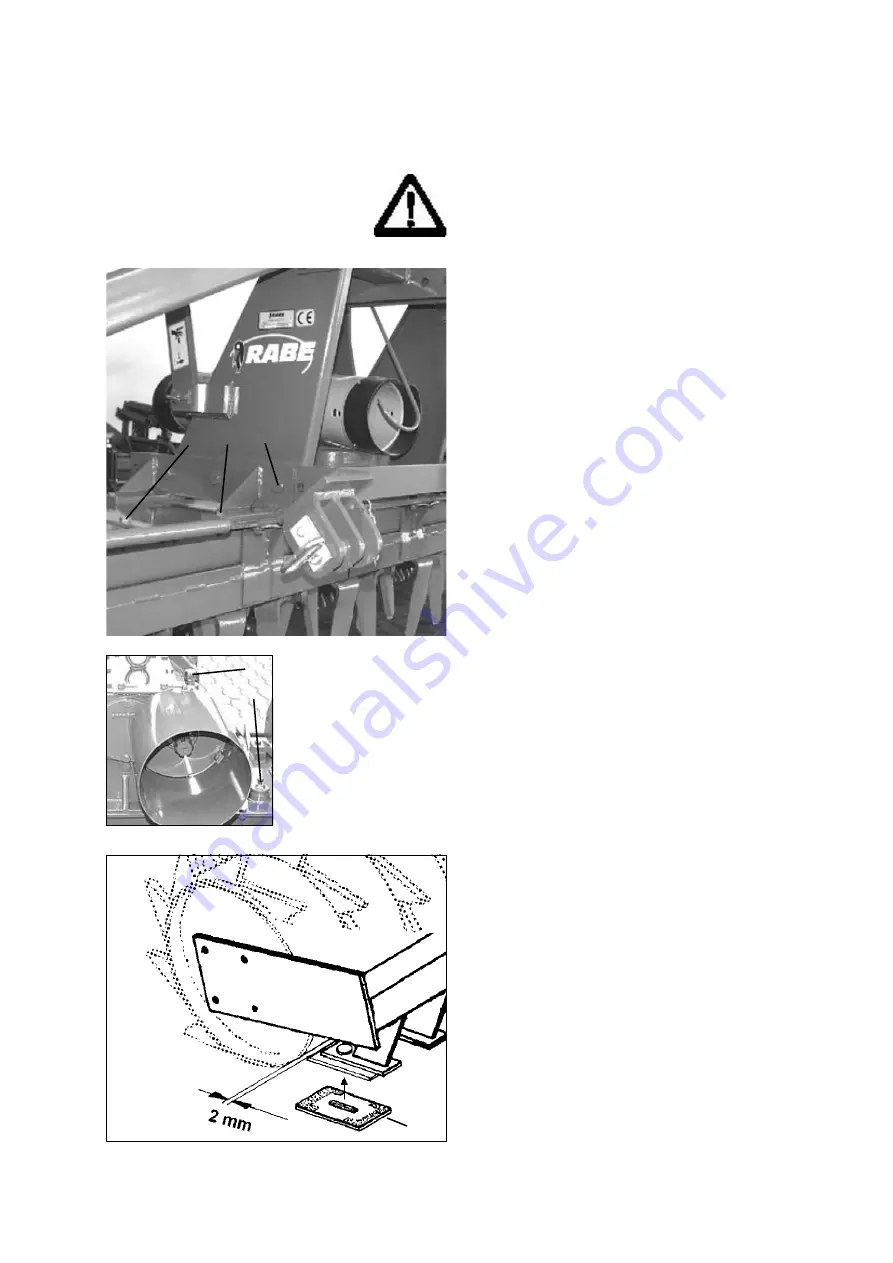
Maintenance
Before working on the attached implement, disengage the
power take-off shaft, switch off the engine and remove the
ignition key.
DO NOT work under a raised implement. If this is unavoid-
able, secure the implement to prevent it dropping by ac-
cident.
Use suitable tools and wear protective gloves when han-
dling cutting implements.
Before working on the hydraulic system (”Drill-Lift”), lower
the implement completely and release the hydraulic pres-
sure. Dispose of used oil and lubricants correctly (mineral-
based products only!).
After about eight hours of initial use, check all screws
and bolts for tightness. Repeat this check at regular
intervals and tighten using a torque wrench.
The knife tine fixing bolts should be tightened to 380
Nm,
and the hitch attachment (
21/1
; M 20x1.5) to 650 Nm,
(
21/2
; M 12 - 12.9) - to 145 Nm,
cover bolts: (
21/3
; M 12 - 10.9) - 120 Nm.
Daily:
Check the level of transmission oil by insert-
ing the dipstick (
22/1
) as far as the thread, but without
screwing it in.
Weekly:
Check the level of liquid lubricant grease in
spur gear casing at nozzle (
22/3
; see also section on oil
changes).
Lubricate the bearings regularly with a grease gun applied
to the greasing nipples;
daily:
packer-roller bearings, at
”Drill-Lift” three-point linkage and drive shaft (including slid-
ing profiles).
Oil all linkages, ensure free movement of spindles.
Touch up any chipped or damaged paintwork.
Check the propeller-shaft overload clutch; ”air” the fric-
tion clutch if the implement has not been in use for a
long period.
Avoid directing the hose at the bearings for any length
of time when cleaning the implement with high-pressure
water.
Check the hydraulic hose (Drill-Lift) regularly for signs
of damage or brittleness and replace as required (see
list of spare parts). These hoses are subject to a natural
ageing process and should in any case be replaced
after 5-6 years, regardless of their apparent condition.
Toothed roller:
Readjust the scraper at regular inter-
vals. Push the scraper into slight contact with the roller.
When tightening the nuts, ensure that the scraper lies
parallel along its entire length.
Fit hard-coated scrapers (
23/1
) with the coated surface
facing upwards relative to the roller, at a distance of
about 2 mm from the roller.
The toothed roller is easy to keep clean if it is washed
down after each use and protected from corrosion.
22
1
3
21
1
23
11
1
2
3