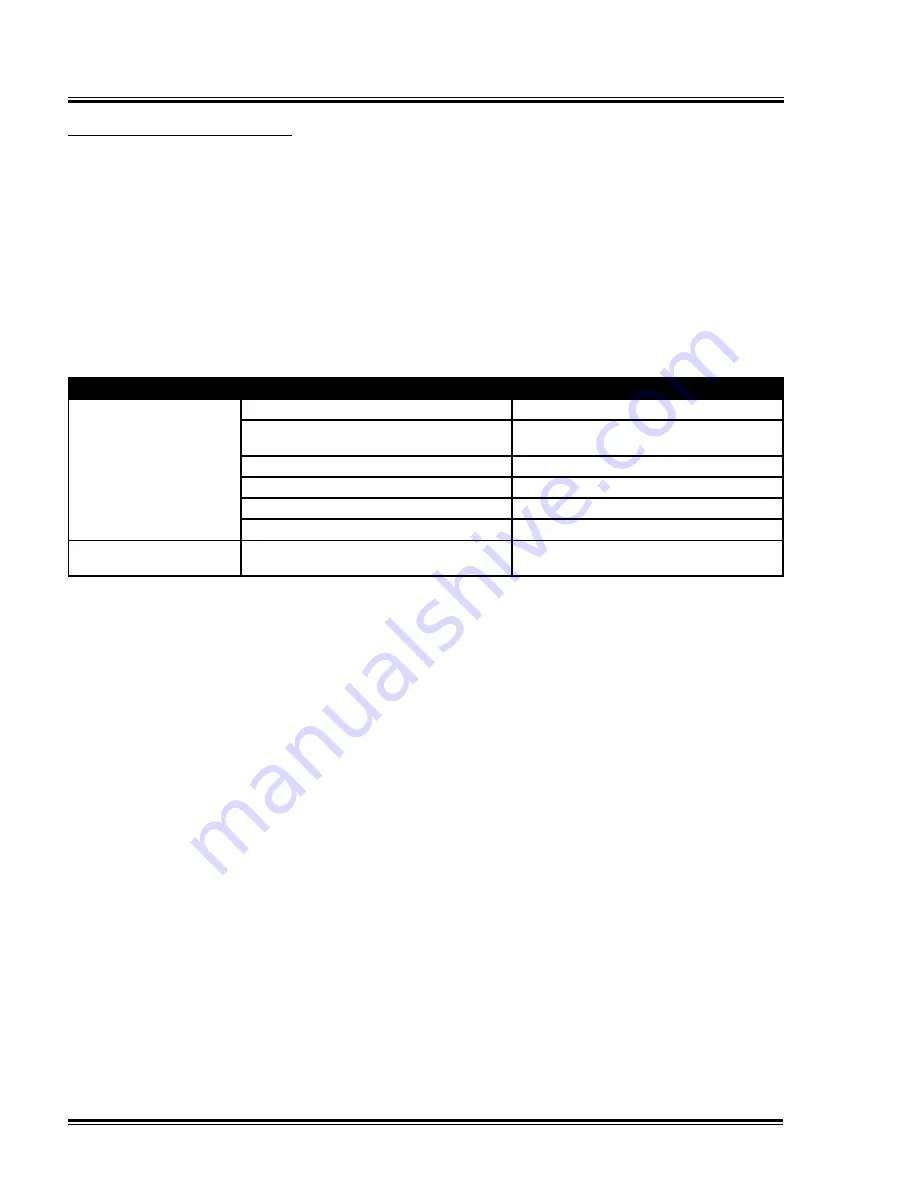
Section VI - Troubleshooting
General Troubleshooting
Before specific identification of any fault
is looked for, the following general points
must be verified:
Has the unit been damaged externally
or are any parts missing?
Is power being supplied to the unit?
Was startup carried out in accordance
with the instructions in this manual?
•
•
•
Are all external valves correctly set for
operation?
Do the operational conditions meet
those specified at time of ordering and
used for product selection?
The table below gives possible causes and
corrective actions to faults that may occur
on the dryer:
•
•
P
roBlem
P
oSSiBle
cAuSe
A
ction
p
oor
deWpoint
l
iquid
WAter
At
dryer
inlet
c
HecK
pre
-
filtrAtion
And
drAins
e
xcessive
floW
c
HecK
ActuAl
floW
AgAinst
mAximum
specified
l
oW
inlet
pressure
c
HecK
AgAinst
specificAtion
H
igH
inlet
temperAture
c
HecK
AgAinst
specificAtion
s
ilencer
BlocKed
or
dAmAged
r
eplAce
silencer
A
ir
leAKs
t
igHten
joints
or
fit
neW
seAls
i
ncorrect
dryer
operAtion
j
Ammed
sHuttle
vAlves
or
fAulted
electricAl
components
s
ee
electricAl
trouBlesHooting
Quincy Compressor-QMOD