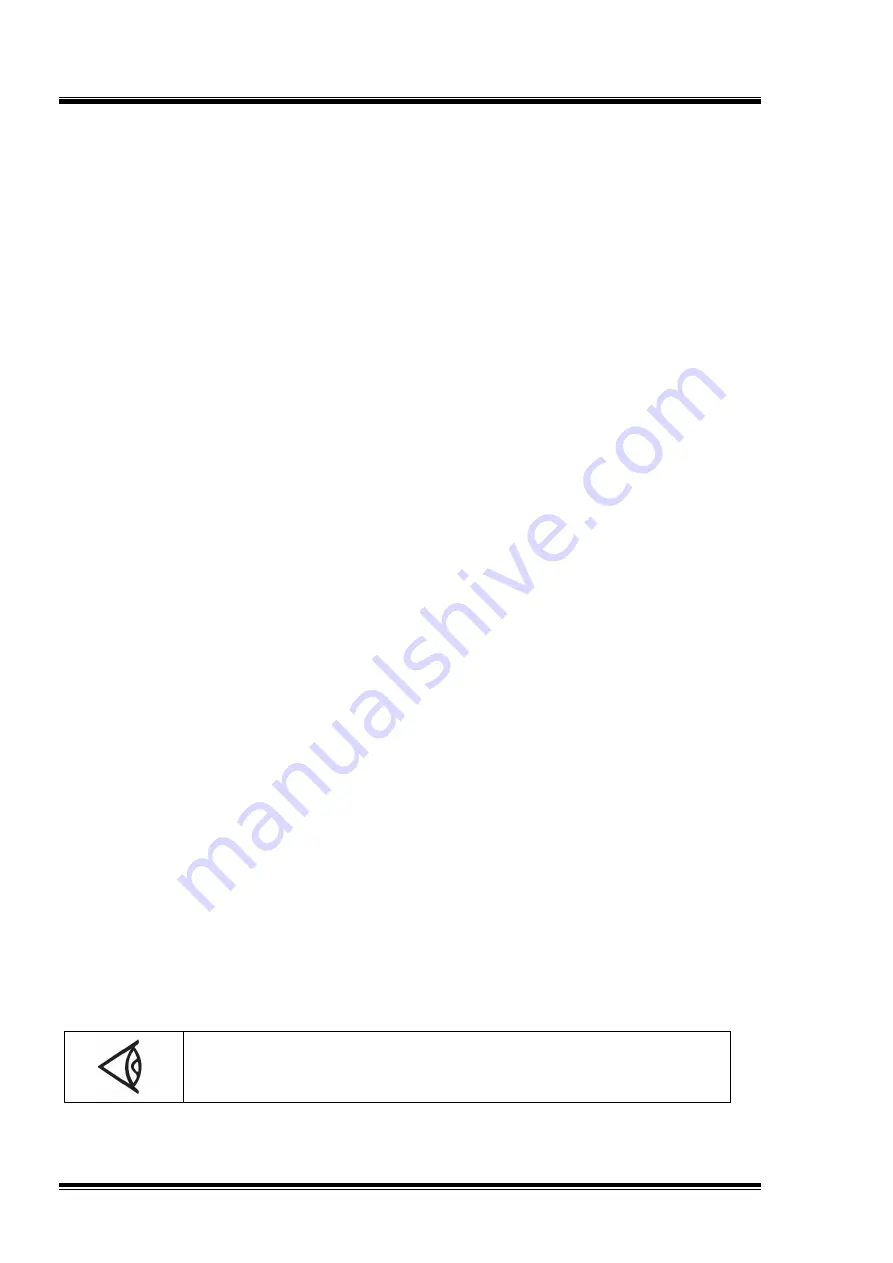
Section III - Installation
28
Location:
Locate the pump horizontally on a level surface. Ensure surface must be clean, well lit,
well ventilated and capable of taking the weight of the pump. The entire length of the
frame base must be supported. Insert shim, where necessary (Do not use wood).
Anchoring to the ground is not necessary but essential if mounted on a frame or a
structure that may result in the pump moving. Always consider using anti-vibration
mounts.
Ambient temperature should not exceed temperatures listed in chapter “Technical data”.
All models are intended for indoor installation. Outdoor installations will require
additional weather protection. Do not locate the unit where the hot air from other pumps
or heat generating equipment may be drawn in to the unit. Never restrict the flow of
exhaust air from the pump. The hot exhaust air must be exhausted to the outside to
prevent high ambient conditions in the room. The limiting ambient conditions are 0°C to
40°C (32°F to 104°F) and atmospheric pressure. Please consult the manufacturer, if
operating outside of the criteria.
The pump is designed to be located and operated in safe environment areas where
there this is no risk of explosion. Environmental conditions must comply with the
protection class of the motor as depicted on its name plate. Consideration must be
given to the safety and welfare of personnel. Thermal insulation should be provided to
offer protection against the intense heat which can
be generated around the exhaust of the
pump.
Piping connections:
Process connection, exhaust pipework and associated component must be installed in
line with general engineering practices and abide by local by-laws and regulations.
Good installation practice include the correct sizing of the process pipework to reduce a
loss of performance and to prevent damage to the pump. Ideally all pipework, filters and
accessories should be fully supported to reduce physical stress on the pump.
Vibration transmittal through the pipework must be minimized. Pipework should slope
away from the pump to reduce the risk of condensate liquid running back in the pump.
The filtration equipment should be fitted if there is a chance of particulate carry-over. 5
micron or less is ideal.
Pipework should be straight as possible with no tight bends and convoluted runs. It
should be sized correctly to reduce losses. Use the same diameter of pipe for pump
process connection. Pipe runs that are convoluted or lengthy (beyond 10 meters) need
careful consideration and proper sizing.
Make sure all piping connections from the pump to the point of use are leak tight and
secure. Use easy to release and flexible connection at the point of final connection to
the pump.
Process isolation valves are also essential but in the case of vacuum pump, never
isolate the exhaust that may lead to high back-pressure. Drip-leg drains or low position
drain point is also good installation practice. The exhaust silencer is fitted with a drain
plug or drain tab and consideration should be given to adequately dealing with
condensate drain off.
A variety of pipe material are available for installation but they must be compatible with
the process medium. The discharge air can run up to 250 °C (482 °F), so piping should
be suitable to handle this temperature.
At 2.5 bar (g) pressure, overpressure pump can generate hot air
up to 250°C, the pipe must be rated accordingly.
Summary of Contents for QCV 045
Page 2: ...This page intentionally left blank...
Page 21: ...Section III Installation 21 Dimension drawing QCV 045 QCV 90 vacuum pump...
Page 22: ...Section III Installation 22 Dimension drawing QCV 220 vacuum pump...
Page 23: ...Section III Installation 23 Dimension drawing QCLP 90 Overpressure pumps...
Page 24: ...Section III Installation 24 Dimension drawing QCLP 220 Overpressure pump...
Page 55: ...Notes 55...