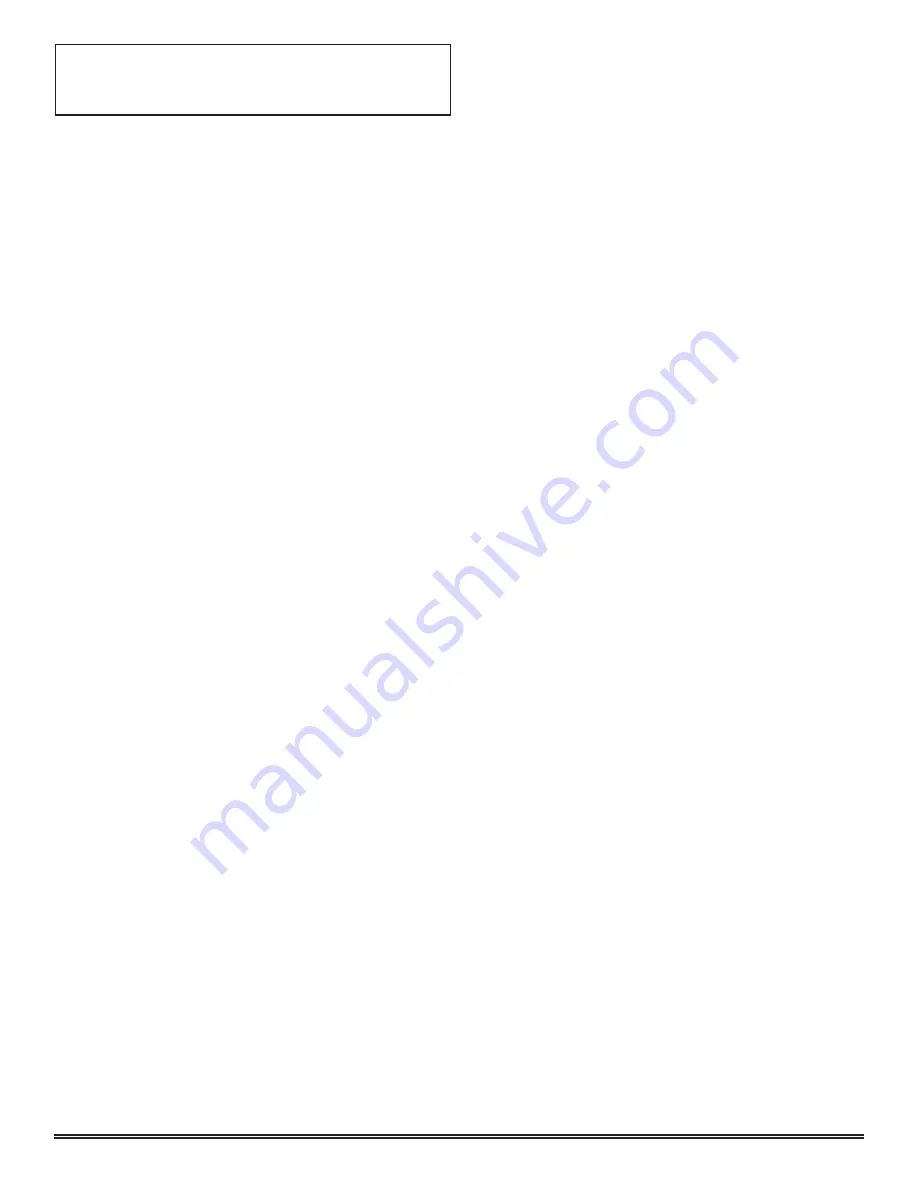
10/08
Page 5
Quadra-Fire • Hudson Bay • 7003-121 Rev. i
NOTE:
The following requirements reference various
Massachusetts and national codes not contained in this
document.
For all side wall horizontally vented gas fueled equipment
installed in every dwelling, building or structure used in whole
or in part for residential purposes, including those owned or
operated by the Commonwealth and where the side wall
exhaust vent termination is less than seven (7) feet above
fi nished grade in the area of the venting, including but not
limited to decks and porches, the following requirements
shall be satisfi ed:
Installation of Carbon Monoxide Detectors
At the time of installation of the side wall horizontal vented
gas fueled equipment, the installing plumber or gas fi tter shall
observe that a hard wired carbon monoxide detector with an
alarm and battery back-up is installed on the fl oor level where
the gas equipment is to be installed. In addition, the installing
plumber or gas fi tter shall observe that a battery operated or
hard wired carbon monoxide detector with an alarm is installed
on each additional level of the dwelling, building or structure
served by the side wall horizontal vented gas fueled equip-
ment. It shall be the responsibility of the property owner to
secure the services of qualifi ed licensed professionals for the
installation of hard wired carbon monoxide detectors.
In the event that the side wall horizontally vented gas fueled
equipment is installed in a crawl space or an attic, the hard
wired carbon monoxide detector with alarm and battery back-
up may be installed on the next adjacent fl oor level.
In the event that the requirements of this subdivision can not
be met at the time of completion of installation, the owner shall
have a period of thirty (30) days to comply with the above
requirements; provided, however, that during said thirty (30)
day period, a battery operated carbon monoxide detector with
an alarm shall be installed.
Approved Carbon Monoxide Detectors
Each carbon monoxide detector as required in accordance
with the above provisions shall comply with NFPA 720 and
be ANSI/UL 2034 listed and IAS certifi ed.
Signage
A metal or plastic identifi cation plate shall be permanently
mounted to the exterior of the building at a minimum height
of eight (8) feet above grade directly in line with the exhaust
vent terminal for the horizontally vented gas fueled heating
appliance or equipment. The sign shall read, in print size no
less than one-half (1/2) inch in size,
“GAS VENT DIRECTLY
BELOW. KEEP CLEAR OF ALL OBSTRUCTIONS.”
H. Requirements for the Commonwealth of
Massachusetts
Inspection
The state or local gas inspector of the side wall horizontally
vented gas fueled equipment shall not approve the installa-
tion unless, upon inspection, the inspector observes carbon
monoxide detectors and signage installed in accordance with
the provisions of 248 CMR 5.08(2)(a) 1 through 4.
Exemptions
The following equipment is exempt from 248 CMR 5.08(2)(a)
1 through 4:
•
•
The equipment listed in Chapter 10 entitled “Equipment
Not Required To Be Vented” in the most current edition of
NFPA 54 as adopted by the Board; and
Product Approved side wall horizontally vented gas fueled
equipment installed in a room or structure separated from
the dwelling, building or structure used in whole or in part
for residential purposes.
MANUFACTURER REQUIREMENTS
Gas Equipment Venting System Provided
When the manufacturer of Product Approved side wall
horizontally vented gas fueled equipment provides a vent-
ing system design or venting system components with the
equipment, the instructions provided by the manufacturer for
installation of the equipment and the venting system shall
include:
•
•
Detailed instructions for the installation of the venting sys-
tem design or the venting system components; and
A complete parts list for the venting system design or
venting system.
Gas Equipment Venting System NOT Provided
When the manufacturer of a Product Approved side wall hor-
izontally vented gas fueled equipment does not provide the
parts for venting the fl ue gases, but identifi es “special vent-
ing systems”, the following requirements shall be satisfi ed by
the manufacturer:
•
•
The referenced “special venting system” instructions shall
be included with the appliance or equipment installation
instructions; and
The “special venting system” shall be Product Approved
by the Board, and the instructions for that system shall
include a parts list and detailed installation instructions.
A copy of all installation instructions for all Product Approved
side wall horizontally vented gas fueled equipment, all vent-
ing instructions, all parts lists for venting instructions, and/or
all venting design instructions shall remain with the appli-
ance or equipment at the completion of the installation.
See Gas Connection section for additional Common-
wealth of Massachusetts requirements.