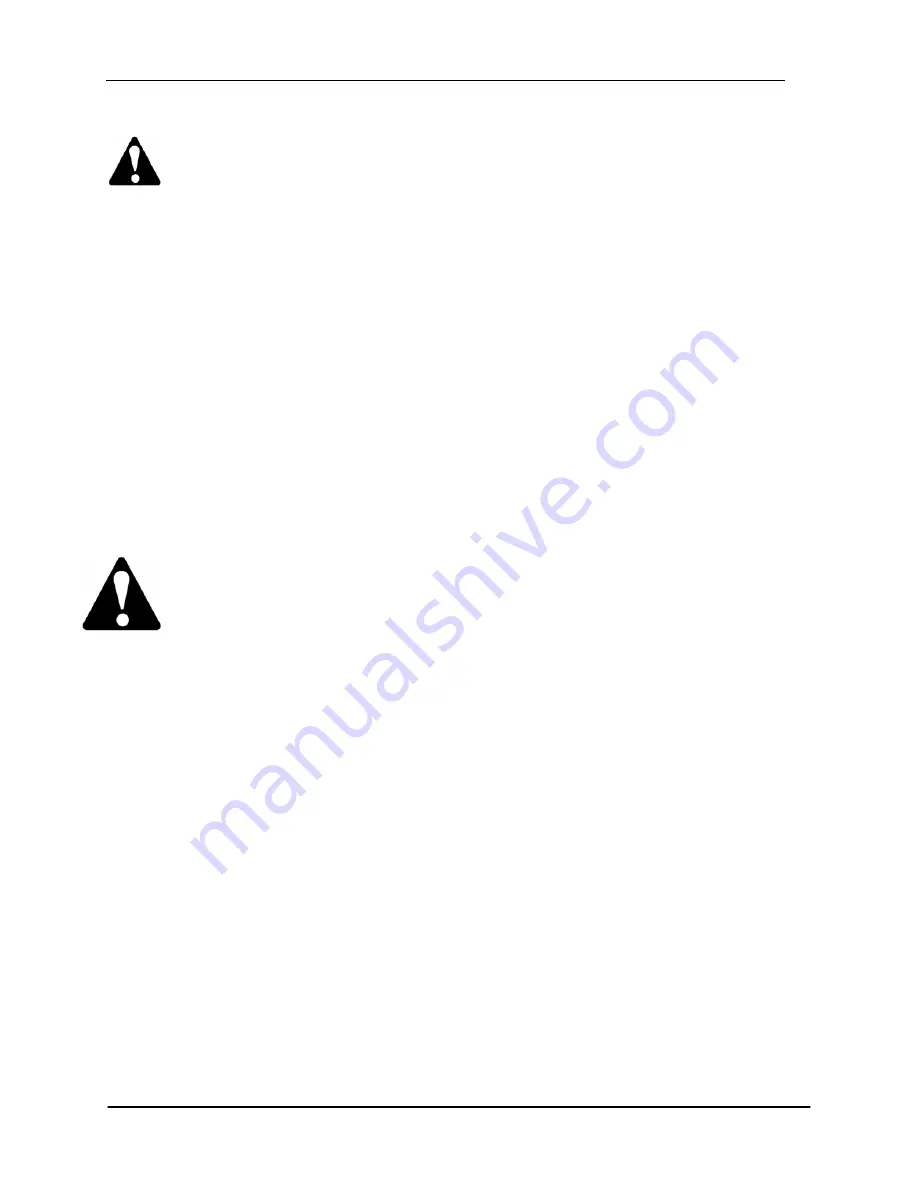
Quad Power Brush
Operators Manual – Version 06
1
SAFE OPERATION
1. GENERAL OPERATION
.1
Read the operating and service instruction manual
carefully
.
.2
Become thoroughly familiar with the controls and the
proper use of the equipment. Know how to stop the unit
and disengage the controls quickly.
.3
Allow only responsible adults, who are familiar with
the instructions, to operate this machine. Never allow
children to operate the equipment.
.4
Be sure the area is clear of bystanders, children and
pets before operating. Stop machine if anyone or
anything enters the area.
.5
NEVER CARRY PASSENGERS while sweeping with
the PB60
.6
Thoroughly inspect the area where the equipment is
to be used and remove all foreign objects.
.7
Disengage clutch on ATV and shift ATV into neutral
before starting the engine (motor). Refer to the safety
section in the ATV operators manual
.8
Never attempt to make adjustments while the engine
(motor) is running
.9
Always wear safety glasses or eye shields: during
operation, while performing an adjustment or repairs; to
protect eyes from foreign objects that may be thrown
from the machine.
.10
Maintain or replace safety and instruction labels, as
necessary. Never tamper with safety devices and check
their proper operation regularly.
2. GENERAL DEVICE OPERATION
.1
Do not put hands or feet near or under rotating parts.
.2
Exercise extreme caution when operating on or
crossing gravel drives, walks or roads. Stay alert for
hidden hazards and traffic.
.3
After striking a foreign object; stop the engine
(motor) remove the wire from the spark plug, thoroughly
inspect the brush for any damage, and repair damage
before restarting and operating the brush.
.4
If the unit should start to vibrate abnormally, stop the
engine (motor) and check immediately for the cause.
Vibration is generally a warning of trouble.
.5
Stop the engine (motor) whenever you leave the
operating position, before making any repairs,
adjustments or inspections.
.6
Take all possible precautions when leaving the
machine unattended. Disengage the drive, lower the
attachment, set the parking brake, stop the engine and
remove the key.
.7
Before cleaning, repairing or inspecting, make
certain all moving parts have stopped. Disconnect the
spark plug wire and place the wire away from the plug
to prevent accidental starting.
.9
Do not operate across the face of slopes. Exercise
extreme caution when changing direction on slopes. Do
not attempt to clear steep slopes.
.10
Never operate the brush without provided guards,
plates or other safety protective devices in place.
.11
Never operate the machine at high transport speed
and use care when backing up!
.12
Never allow anyone in front of the unit.
.13
Disengage power to the brush when transporting or
not in use.
.14
Never operate the power brush without good
visibility or good light.
While operating, ALWAYS attach
the clip end of the Tether Cord
to your belt, until you dismount
from the ATV. The switch the
cord is attached to will shut off
the engine if pulled deliberately
or by inadvertent dismount from
the ATV seat.
DANGER
Failure to observe the following safety instructions
could result in serious injury and or