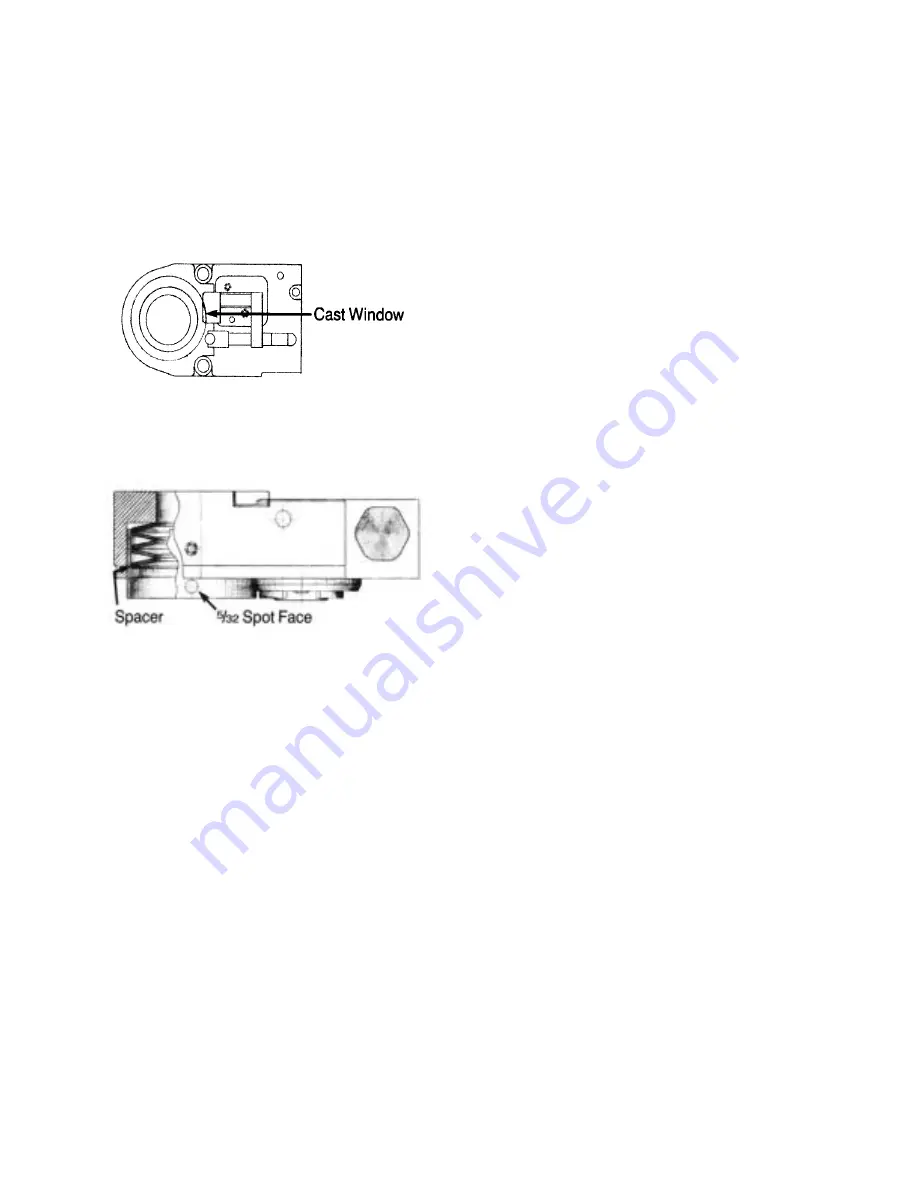
7
REASSEMBLY:
Turn the two (2) set screws 382637 in until the tips are nearly
flush with the bore (must clear spring case). Place one bead of
thread locking liquid on outer thread of each set screw. Using
a vise (or similar device), align the spring case (with Belleville
washers inside) and compress somewhat, until the 5/32" dia.
spotface is in the position shown. Tighten each set screw 1 &
1/2 turns, and remove from vise. Set screws should retain
spring case; but allow spring stack to compress and "spring
back".
Note: Milled slot on top rim of spring case must be visible thru
cast window in the upper block.
Note: Spring washers must be stacked exactly as shown. A
spacer may be included in the spring stack and must be
installed under the bottom washer against the spring case.
Align the bore of the spring washers to clear the 7/8" O.D. of
the spindle.
LUBRICATION:
An automatic in-line filter-lubricator is highly recommended.
This will supply the tool with clean, lubricated air; keep it in
sustained operation; and increase tool life.
The in-line lubricator should be regularly checked and filled
with a good grade of 10W machine oil. In the event an in-line
lubricator is not used, the tool should be disconnected from the
air supply several times daily and several drops of oil poured
into the tool's air inlet bushing.
The right angle drill head should receive a generous amount of
"Lubriplate #907" grease every fifteen (15) to twenty-five (25)
hours of "actual motor running" time through the two (2) flush
type grease fittings in the right angle housing. "Lubriplate
#907" may be purchased in a 5 gallon can using Part No.
107210.
GENERAL MAINTENANCE:
Tool Maintenance and Pressure Test Equipment Kit 381273
is available and can be used for some trouble shooting.
Air control system filter 382505 located in the handle 382480
should be replaced every 2000 drilling cycles or when low air
control system pressure is suspected.
Spindle threads should be blown clean and lubricated every
100 drilling cycles.
DISASSEMBLY—DRILL HEAD:
Remove the side hose assembly. Clamp the drill head in vise
and loosen lockring 619421. Unscrew and remove power unit.
Remove shear pin. Unscrew one (1) 6-32 x 1 (7/64" hex)
socket head cap screw 382539 and two (2) 1/4-20 x 2 1/4
(3/6" hex) socket head screws 867839. Clamp drill head in
upright position in vise. Insert finger in spindle feed gear to
prevent the eighteen (18) 7/32" balls 842160 from being lost
when removing upper block assembly. Remove upper block
assembly. Remove gear holder 382557. Unscrew the two (2)
1/4-20 x 7/8 (3/1 6" hex) socket head cap screws 865123 and
remove the housing cover 382582 or 382591. Gears will come
out with housing cover.
DISASSEMBLY—GEAR TRAIN:
SINGLE REDUCTION
—Unscrew and remove the lock ring
619421. Clamp the flats of the internal gear case 382590 in the
vise and unscrew the motor housing 382509. Remove the
spider assembly from the gear case. Remove the rear ball
bearing 613281. Remove the three (3) idler gear pins and
gears. Hold a large hex wrench or similar tool on the side of the
spider and clamp in the vise. Heat the spider and pinion to
approximately 300°F. Insert a suitable pin thru the hole in the
pinion 629045 and unscrew the pinion. Use Tool Maintenance
and Pressure Test Equipment Kit 381273 for easier disassem-
bly.
DOUBLE REDUCTION
—Unscrew and remove the lock ring
619421. Clamp the flats of the internal gear case 382590 in the
vise and unscrew the motor housing 382509. Unscrew and
remove the internal gear and housing 617369. Remove the
rear ball bearing 613281 from both spiders. Remove the six (6)
idler gear pins and gears. Hold a large hex wrench or similar
tool on the side of the second reduction spider and clamp in the
vise. Heat the spider and pinion to approximately 300°F. Insert
a suitable pin thru the hole in the pinion 629045 and unscrew
the pinion. Use Tool Maintenance and Pressure Test Equip-
ment Kit 381273 for easier disassembly.
FOR VARIABLE SPEED TOOLS,
SEE PAGES 10 AND 11