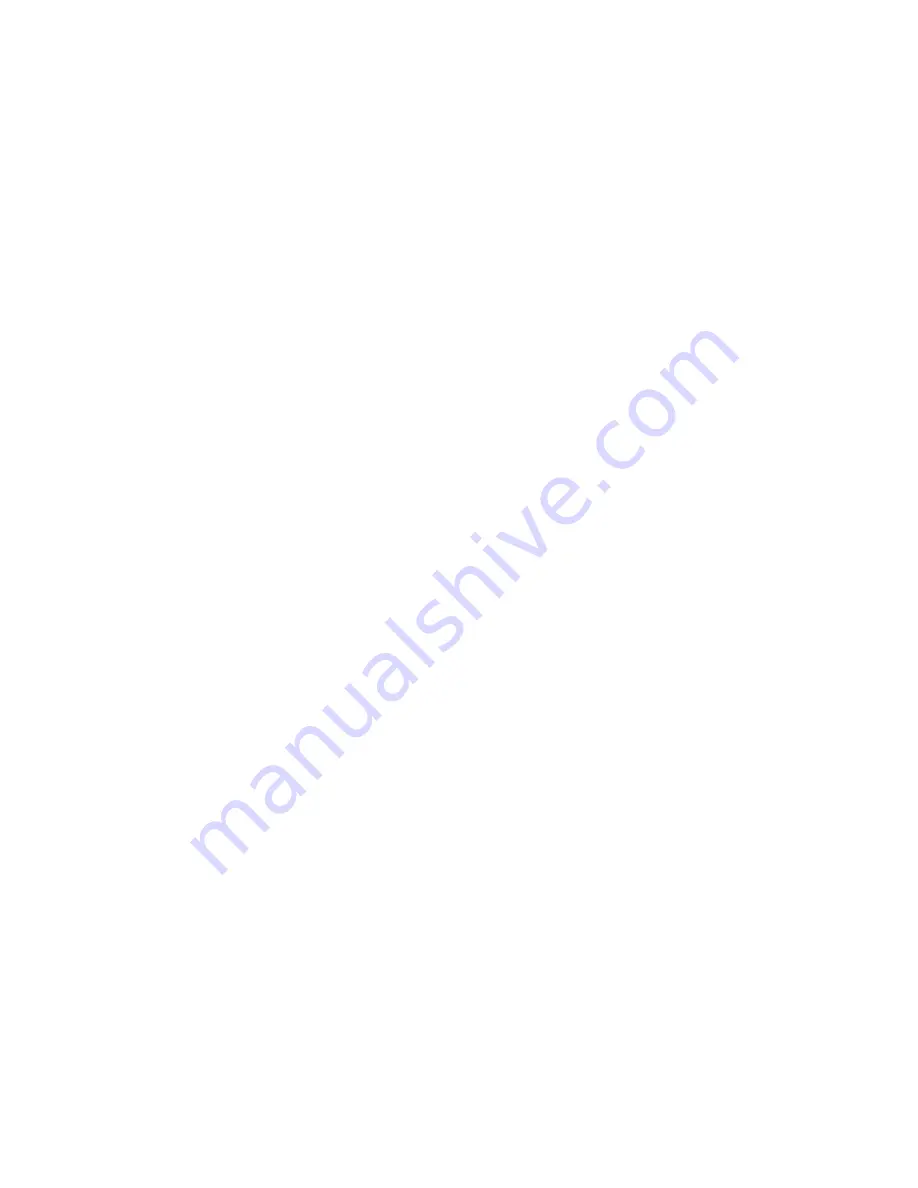
5
OPERATING INSTRUCTIONS
If the tool has been shipped recently, been in storage, or
repaired, or disassembled; it should be run (without spindle)
through a "tool crib check" of functions.
EMERGENCY STOP
—Depressing the red emergency stop
button
1
will stop the tool, except when the rapid advance mode
is being utilized. Releasing the rapid advance lever
2
will stop
the tool.
RAPID ADVANCE
—Depressing the rapid advance lever
2
will
advance the cutting tool to the work surface faster than the
regular feed rate and stops advancing forward automatically
until the green drill button
4
is depressed. Note: When the rapid
advance lever is depressed, the exhaust deflector
3
will move
forward (toward the head) approximately 3/8" and return to its
original position when the lever is released.
DRILLING
—Press the green drill button
4
firmly and release
it to start the drilling cycle. The cutter will feed to a predeter-
mined depth, dwell, and then retract. The drill motor will shut
off automatically at the end of the retract stroke. The cutter may
be manually retracted at any time by raising the retract lever
5
.
IMPORTANT: The spindle retracts at a much faster rate than
it feeds. Care should be taken to avoid entrapment.
Do not hold the drill button down during the end of the retract
stroke—this prevents "motor stop".
DEPTH ADJUSTMENT:
DEPTH COLLAR
—Has four (4) holes for adjusting depth in
increments of .005". Going from one hole to the next and using
the same slot in the spindle will either increase (clockwise) or
decrease (counterclockwise) the depth by .005". Using the
same hole and rotating the collar 90° will give an adjustment of
.020" and 360° will give an adjustment of .080". Tighten lock
screw after each depth adjustment. Tip of lock screw must go
into a spindle slot. IMPORTANT NOTE: To insure maximum
repeatability, the work surface, fixtures, and depth stop must
be cleared of any chips or foreign material before beginning the
next hole. Always replace the rear spindle guard after making
a depth adjustment.
TOOL CRIB CHECK
1.
With air supply shut off, remove rear spindle guard.
2.
Remove depth stop
6
(left hand threads).
WARNING: Keep hands and clothing clear of rotating spindle,
turn air supply on and use rapid advance to remove spindle.
3.
Shut off air supply pressure.
4.
Depress 5/16" diameter steel end of throttle piston
9
. The
throttle piston must spring return quickly when released.
5.
With air supply on, move rapid advance lever
2
all the way.
Motor runs and spindle feed gear (threaded I.D.) must not
rotate. Spindle drive gear (splined l.D.) rotates. Shear pin
is whole and intact.
6.
Release rapid advance lever
2
and press green drill button
4
all the way in. Motor starts. Release drill button
4
. Motor
continues to run. Both gears (splined and threaded) rotate.
7.
Lift manual retract lever
5
and release. An audible "snap"
indicates the retract valve 382333 is shifting as desired.
Spindle feed gear (threaded l.D.) stops rotating.
8.
Depress signal valve
8
with screwdriver and release.
Motor stops and retract valve 382333 must reset (manual
retract lever
5
should drop). Depress red stop button
1
slowly. There should be no venting of air as the stop button
1
is depressed.
9.
The lift arm assembly 382665 must be intact, undamaged,
and in place in the upper block. The lift arm assembly is
factory adjusted (new tool) for little or no play.
10. Press green drill button
4
and release. Motor starts. Press
stop button
1
. Motor stops. Do not proceed with test if
steps 1 through 10 indicate malfunction.
11. WARNING: Keep hands and clothing clear of rotating
spindle. Using tool 382593, install spindle (with retract
stop collar
7
locked in place). The spindle will retract fully
into the head and the motor will stop automatically. The
retract valve 382333 must reset (manual retract lever
5
should drop) and there should be no venting of air when
the stop button
1
is depressed.
12. Screw depth stop
6
(left hand threads) onto the rear end
of the spindle and lock in place. Rapid advance until depth
stop
6
bears against back of drill head. Rapid advance
clutch will "chatter". Manual retract lever
5
must not rise as
clutch "chatters". Release rapid advance lever.
13. Depress green drill button
4
and release. Motor starts.
Retract lever
5
rises and spindle retracts automatically to
full retract position. Motor will stop automatically.
14. Replace rear spindle guard.