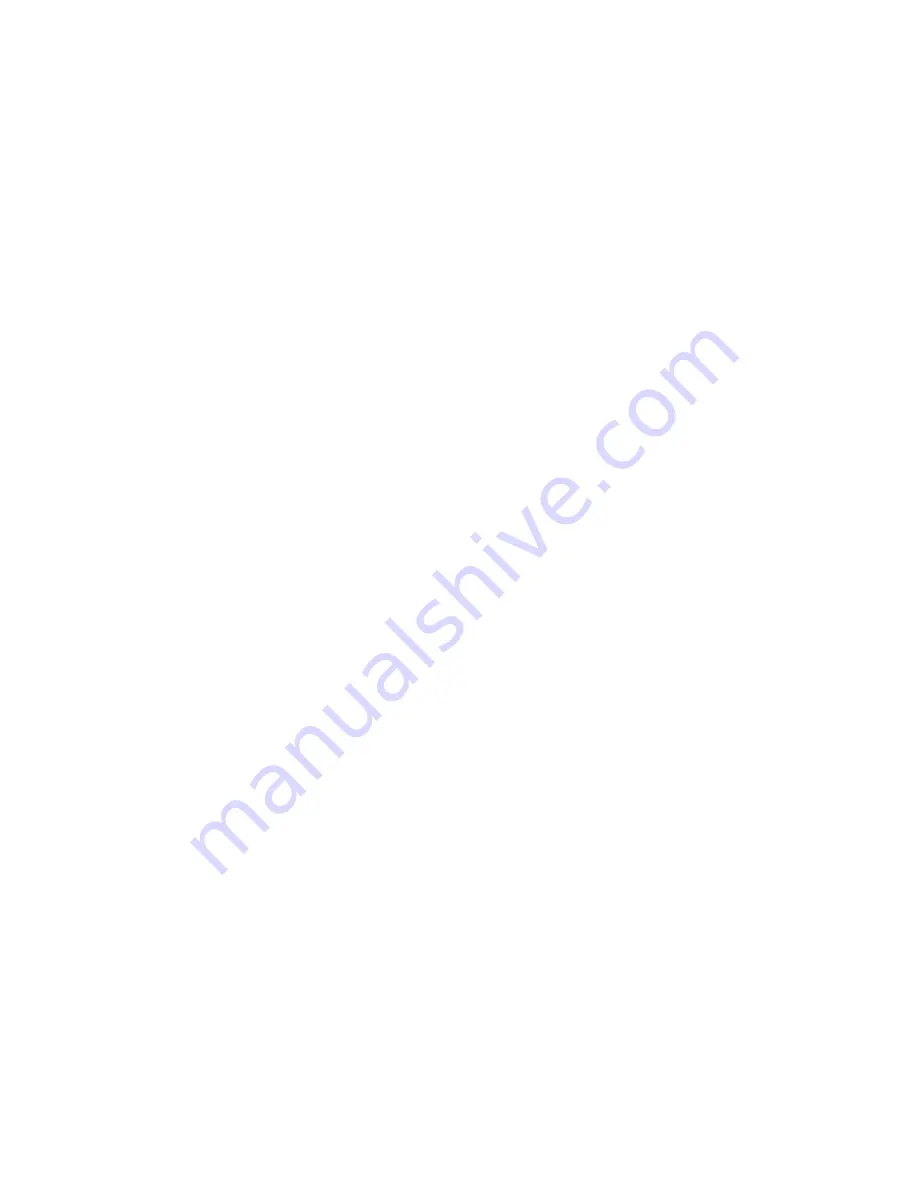
21
If the pressure is 0-60 psig it would indicate a very substantial leak in the air
control system; a damaged side air hose or fitting, a damaged stop button
assembly, check valve, or a leaking feed piston. On "B" model tools this could
indicate a badly leaking signal valve. Also a severely clogged A.C.S. filter
might be the problem or a clogged metering seat (382491).
Excess Leakage (A.C.S.)
Turn on the air supply and press the "drill" button. Press the rapid advance
lever and return the lever fully. This places the tool into the "air-lock mode" with
the throttle open, the motor stalled, and the air control system (A.C.S.)
pressurized.
Plug the air gauge alternately into each small quick disconnect fitting. The
difference in pressure should be no more than 7 psi. A difference of more than
7 psi means excessive leakage in the A.C.S. See Appendix ll. Lift the retract
lever. The retract valve will move with and audible snap. Again, the difference
in pressure should be no more than 7 psi when plugging the air gauge
alternately into each quick disconnect fitting.
Press the stop button. Exhaust deflector and retract lever reset.
Throttle Closing Test
The throttle unlatches and closes as the air control system pressure drops.
With the air gauge plugged into the A.C.S., place the tool back into the "air-
lock mode". Now, very gradually press the stop button. The throttle should
close when the A.C.S. pressure drops to between 42-50 psi. If the throttle
doesn't close, the throttle piston may be sticking, or the latch piston 382490
is not functioning properly.
Signal Valve Venting
Use the highest air supply pressure available (110 psig maximum). With the
air gauge plugged into the air control system, place the tool back into the "air-
lock mode". Lift the retract lever. (The retract valve will move with an audible
snap). Depress the plunger of the venting signal valve (assembly 381117).
The A.C.S. pressure will drop and the throttle should close. If the A.C.S.
pressure does not drop below 38 psig, the A.C.S. system is receiving an
oversupply of air or does not vent properly.
An oversupply of air to the A.C.S. system may be caused by leakage around
the O.D. of the metering seat (382491), or leakage past the lower "O"ring
(869712) on the drill button shaft.
APPENDIX I
Unusual Drilling Conditions
: If the air supply conditions (valves, hoses,
fittings, etc.) can not be improved to meet the tool inlet pressure operating
conditions in the chart, or if the supply pressure (static) must be below 90
psig, the tool may operate adequately at the work site if the pressure at the
inlet tee while drilling and cutting chips does not drop below 70 psi. This would
require monitoring the particular tool at the job site while in use to ensure the
pressure at the inlet tee does not drop below 70 psig.
APPENDIX II
Locating Excessive Leakage In The A.C.S.
Most air leaks create a hissing noise that is easily heard if background noise
is not too loud.
With the air supply on, place a small punch against the bottom end of the
throttle piston (place the punch through the throttle cylinder slot or the throttle
cylinder end cap). This will prevent the throttle from opening if you push
firmly. Now push the drill button a small amount until the A.C.S. is holding
pressure. Remove the punch. You will now be able to locate leaking air
audibly. Some leakage at the retract valve is normal. By lifting the retract
lever you can detect excess leakage at the signal valve, or in the retract
piston air circuit.
Missing "O"-rings or a damaged signal valve are the most common sources
of excessive leakage.