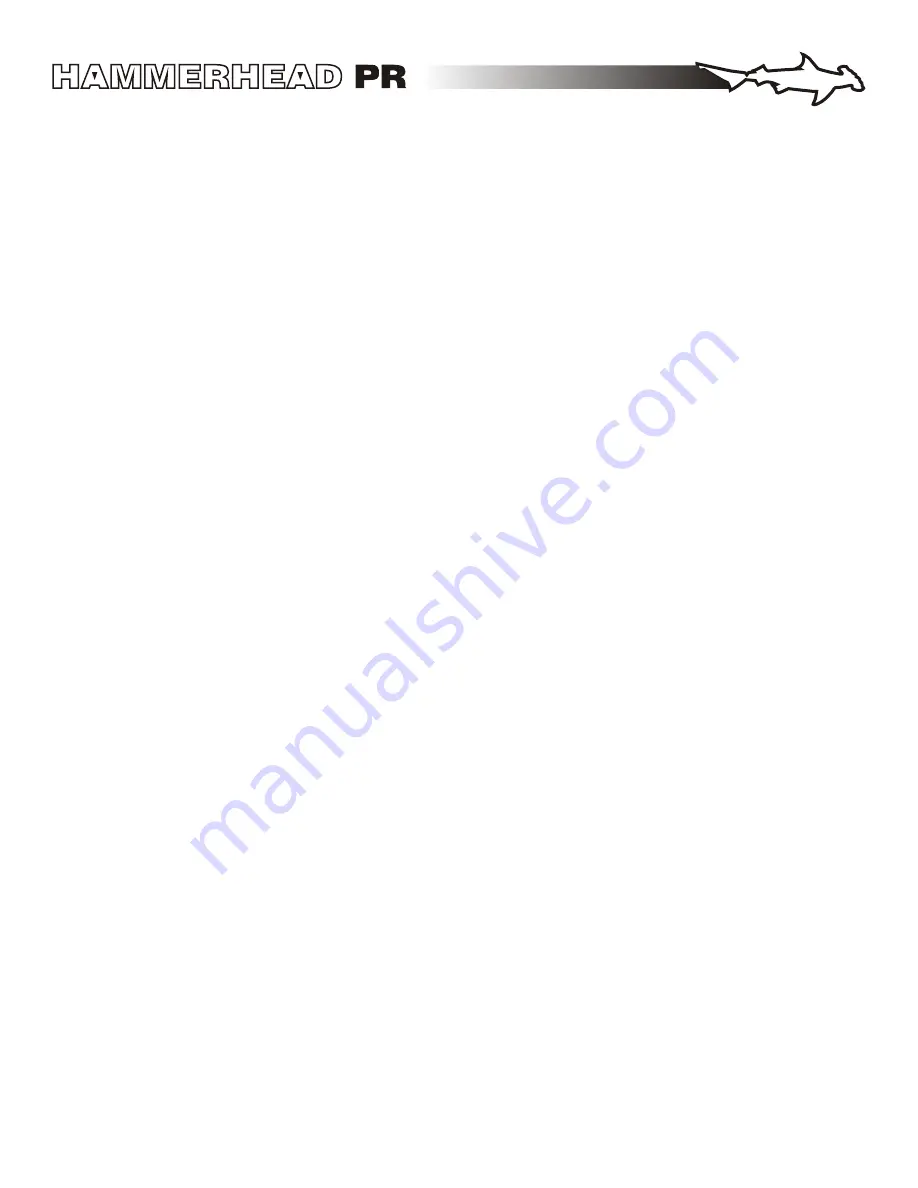
O
Pump Installation
2
1. Cover the pump tubing/hose ends with tape if they are to be pulled through trenches or laid on the
ground. This is to prevent debris from entering the lines.
2. Blow out all water and particles from compressed air conduits (including downwell pump air supply
lines) and fluid lines for at least 10 seconds after the water and particles exit before connecting
them to the system.
3. Slip clamps over appropriate tubing/hose prior to connecting the tubing/hose to the pump barbs.
4. Push tubing/hose down flush with the fitting's nut if possible; cover at least three barbs if three or
more are present (
Note:
when installing tubing in freezing weather, tubing can be dipped in warm
water for a few seconds to soften the nylon).
5. Attach pump support rope/cable to the pump.
6. Attach pump air supply and liquid discharge lines to the well cap. Attach the air exhaust line to the
well cap if the pump air is to exhaust outside the well (Note: the liquid discharge line is always the
largest diameter of the three lines, and the air supply line is always the smallest diameter).
7. Connect the pump air supply and liquid discharge lines to the appropriate surface lines/headers.
8. Turn on the air pressure to the pump (minimum of 0.5 psi per foot of vertical static head).
Note:
Submerging the pump before supplying it with air can also result in fluid entering the air supply
line. This fluid from the well can contain particles, which could interfere with operation of the pump's
air valve.
9. Lower the pump to the desired depth in the well.
10. Secure the pump by tying off the pump support line or by placing the well cap (or flange) on the
well.
11. Increase the air pressure to the pump until the pump is pushing the fluid out at the desired rate.
With sufficient air pressure (at least 10 to 15 psi higher than the vertical static head), the pump will
gradually draw down the fluid level in the well to the level of the pump. The time required for this
draw down varies with the yield of the well as compared to the flow rate of the pump. The maxi-
mum recommended pump operating pressure is 120 psi.
Caution:
Submerging the pump before supplying it with air will result in fluid entering the
exhaust tubing/hose. Those fluids will be discharged from the exhaust tubing/hose during the
first few cycles of the pump. If this discharge will not be confined to the well; i.e., if the air
exhaust line is routed outside the well*, it is important to make sure that the air exhaust line is
not directed such that equipment/ personnel could be splashed by the discharged fluid when
air is turned on to the pump.