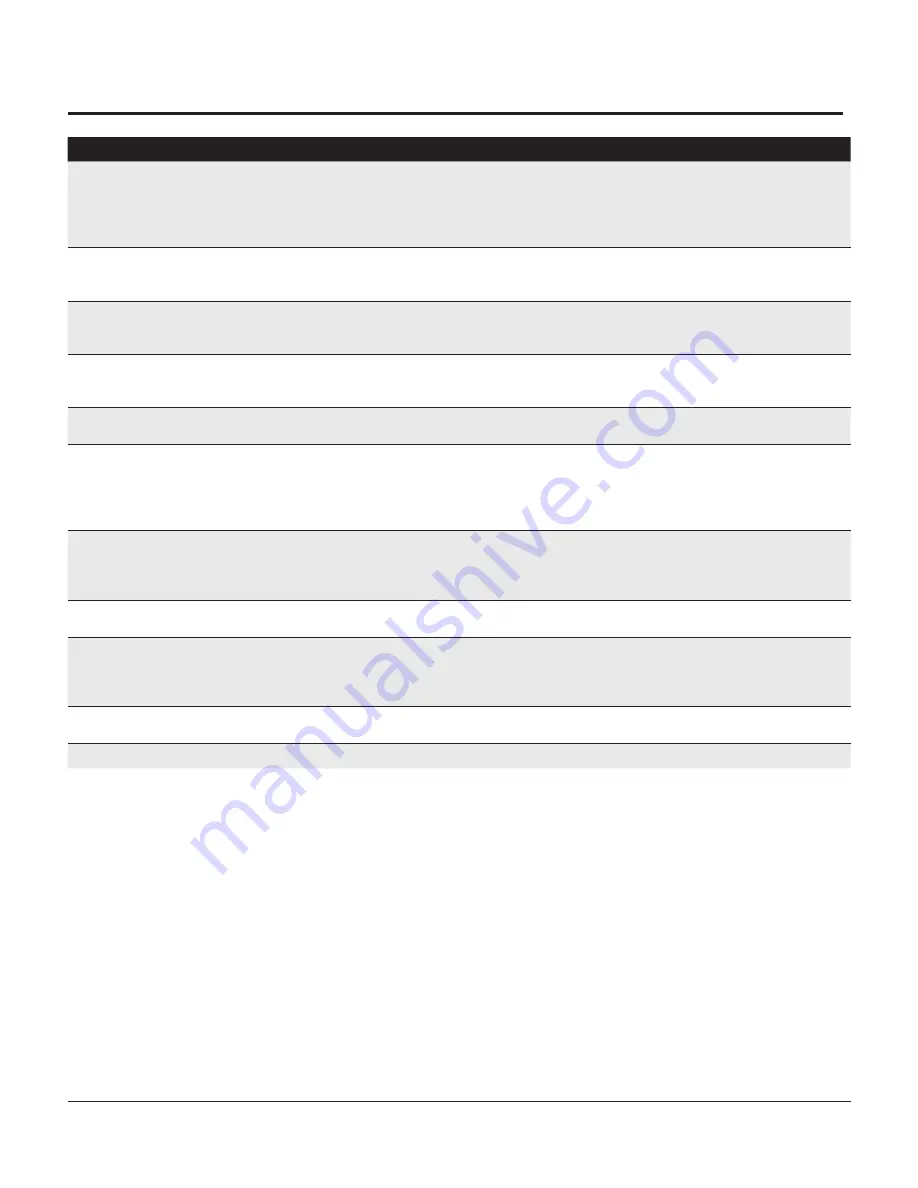
AS40-CD Conveyors | Installation & Maintenance Instructions
19
If you are unable to remedy the problem with these corrective actions, please contact QC Conveyors Customer Service at (513) 753-6000. Failure to correct the problem may
lead to abnormal use of the conveyor, thereby voiding the warranty.
Troubleshooting
Symptom
Possible Cause
Corrective Action
Belt is slipping or stops under load
Demand is more than the conveyor is rated for
Lubrication between drive pulley and belt
Belt is not tensioned properly
Verify conveyor capacity
Clean bottom of belt and drive pulley
Refer to section on tensioning the belt (page 26)
Belt does not move without load
Timing belt under drive guard is not connected
Belt is not tensioned properly
Contact factory
Refer to section on tensioning the belt (page 26)
Belt will not track at drive end
Accumulation or belt wear
Improper tension
Refer to Belt Tracking section of this manual (page 23)
Refer to Belt Tensioning section of this manual (page 26)
Belt will not track at tail end
Irregular product loading or belt wear
Improper tension
Refer to Belt Tracking section of this manual (page 23)
Refer to Belt Tensioning section of this manual (page 26)
Belt will not track at center idlers
Belt is brittle, delaminating or is discolored
Belt is being attacked by chemicals or excessive heat
Belt life has expired
Urethane belts can discolor when exposed to UV light
Contact factory to discuss belt application
Replace belt
No corrective action
Motor is hot
Motor can run with a skin temperature of 221ºF
Motor is not protected with overload protection and is
drawing too much current.
No corrective action
Install overload protection on motor
Speed reducer is getting hot
Speed reducer can run with skin temperature of 225ºF
No corrective action
Speed reducer is leaking oil
Speed reducer’s life has expired
Installation was performed incorrectly and input seal
was damaged
Replace speed reducer
Replace speed reducer
Bearing noise
Bearings are damaged or failing
Refer to Bearing Replacement section of this manual
(page 28)
Belt is traveling reverse of desired direction
Motor or speed reducer not wired properly
Check wiring and correct per wiring instructions
Conveyor belt has prematurely worn out
Correct belt not selected for application
Contact factory to discuss belt application
>