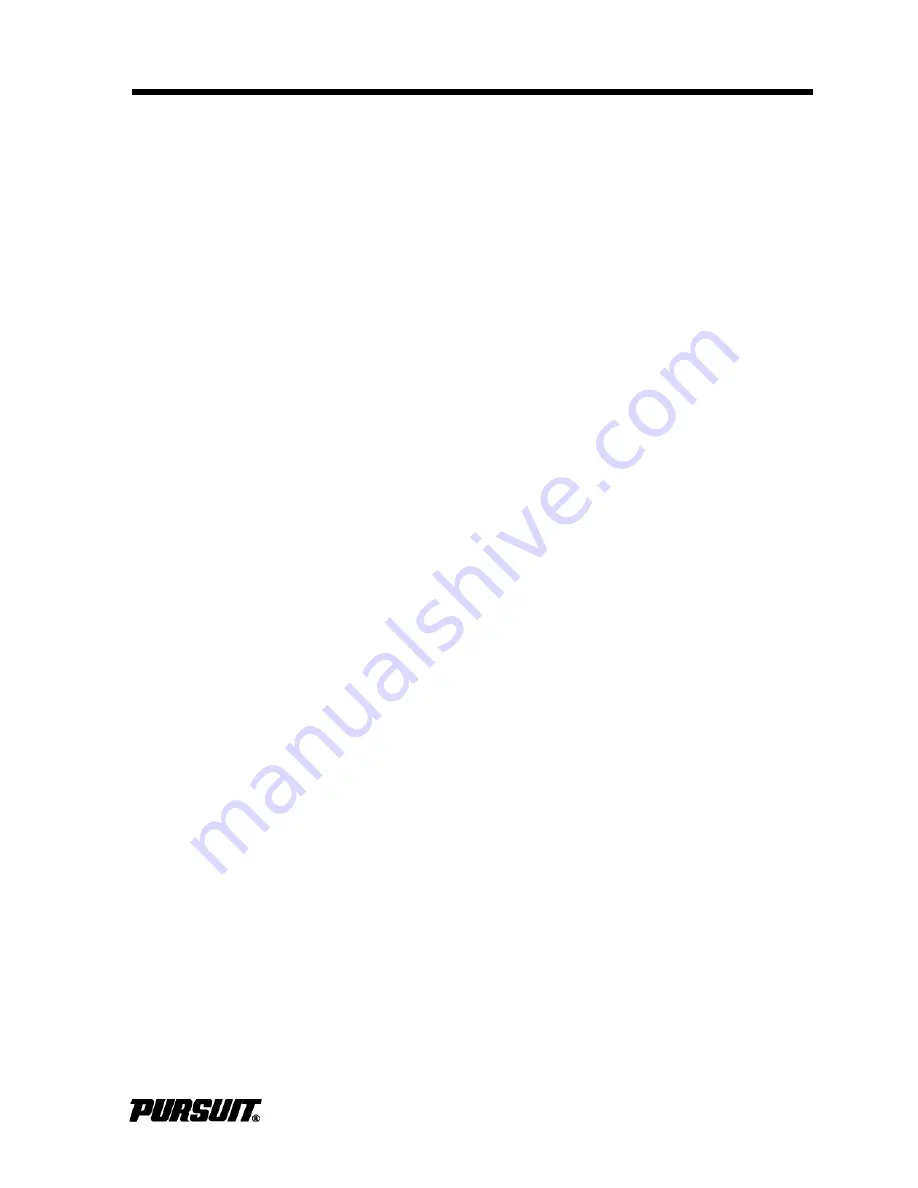
Seasonal Maintenance
12-3
Section 12
OS 385
washdown pump, will not remove the water
from the pump. Remove the outlet hose on
the pump, turn it on and allow it to pump out
any remaining water, approximately a cupful.
An alternate method is to use commercially
available nontoxic, potable water system
antifreeze. If antifreeze is used, pour the
mixture into a pail and put the raw water
intake lines into the solution. Run the pumps
one at a time until the antifreeze solution is
visible at all raw water faucets, discharge fit-
tings and drains. Make sure antifreeze has
flowed through all of the raw water drains.
Run the stern fishbox macerator pump until
all the water is removed from the fishbox
and the pump. To avoid damage to the
pump, DO NOT run pump dry for more than
ten seconds.
Generator Raw Water Systems
Drain sea strainer, heat exchangers and raw
water supply and discharge lines for the
optional generator raw water supply pumps.
Make sure all sea water has drained from
the exhaust system. Some generator engine
mufflers have a drain plug that must be
removed to properly drain the muffler. Once
this is accomplished, pour a nontoxic marine
engine antifreeze mixture into a large pail
and put the generator raw water intake lines
into the solution. Run the generator until the
antifreeze solution is visible at the exhaust
port, then shut the engine off.
Winterize the generator engine and fuel sys-
tem by following the generator manufac-
turer’s winterizing procedures. Refer to
generator’s owner’s manuals or contact a
Pursuit dealer.
Marine Toilet
Winterize the marine toilet following the
manufacturer’s winterizing procedures; fol-
low the procedures exactly. Refer to the toi-
let owner’s manual. Drain the intake and
discharge hoses completely using low air
pressure if necessary. The head holding
tank and macerator discharge pump must
be pumped dry and one gallon of potable
water antifreeze poured into the tank
through the deck waste pumpout fitting.
After the antifreeze has been added to the
holding tank, open the overboard discharge
valve and activate the macerator pump until
the antifreeze solution is visible at the dis-
charge thru-hull.
Air Conditioner
Disconnect and drain the air conditioner
intake and discharge hoses. Remove all
water from the sea strainer and thru-hull fit-
ting. Allow all water to drain from the system.
An alternate method is the use of commer-
cially available nontoxic, potable water sys-
tem antifreeze. If antifreeze is used, drain
the sea strainer and pour the mixture into a
pail and put the raw water intake line into the
solution. Run the air conditioner until the
antifreeze solution is visible at the discharge
fitting on the hull side.
Air conditioner components must be winter-
ized also; follow winterizing procedure in the
air conditioner owner’s manual.
The air conditioning, engine control system,
head, and steering systems have specific
lay-up requirements. Refer to the owner’s
manuals for recommended winterizing pro-
cedures.
Bilge
Coat all metal components, wire busses,
connector plugs (in the bilge), all strainers,
seacocks and steering components with a
protecting oil. The bilge pumps and bilge
pump lines must be completely free of water
and dried out when the boat is laid up for the
winter in climates where freezing occurs.
Compartments in the bilge that will not drain
completely should be pumped out and then
sponged until completely free of water. Dry
the hull bilge and self-bailing cockpit
troughs. Water freezing in these areas could
cause damage.
Hardtop
Makes sure all drain holes in the legs are
open and legs are completely free of water.
Remove the canvas and thoroughly clean
Summary of Contents for OS 345
Page 2: ......
Page 4: ...Operator Notes OS 375...
Page 16: ...12 Operator Notes OS 385...
Page 32: ...3 6 Operator Notes OS 385...
Page 34: ...4 2 Section 4 Electrical System OS 385 Main Distribution Panel MDP...
Page 54: ...5 8 Operator Notes OS 385...
Page 56: ...6 2 Operator Notes OS 385...
Page 98: ...12 6 Operator Notes OS 385...
Page 104: ...A 6 Operator Notes OS 385...
Page 106: ...B 2 Appendix B Maintenance Log OS 385 Date Hours Dealer Service Repairs Maintenance Log...
Page 107: ...Maintenance Log B 3 Appendix B OS 385 Date Hours Dealer Service Repairs...
Page 108: ...B 4 Appendix B Maintenance Log OS 385 Date Hours Dealer Service Repairs...
Page 109: ...Boating Accident Report C 1 Appendix C OS 385 Boating Accident Report...
Page 110: ...C 2 Appendix C Boating Accident Report OS 385...
Page 111: ...Float Plan D 1 Appendix D OS 385 Float Plan...
Page 112: ...D 2 Operator Notes OS 385...
Page 116: ...E 4 Operator Notes OS 385...
Page 117: ...Schematics F 1 Appendix F OS 385 Schematics...
Page 118: ...F 2 Appendix F Schematics OS 385...
Page 119: ...Schematics F 3 Appendix F OS 385...
Page 120: ...F 4 Appendix F Schematics OS 385...
Page 121: ...Schematics F 5 Appendix F OS 385...
Page 122: ...F 6 Appendix F Schematics OS 385...
Page 123: ...Schematics F 7 Appendix F OS 385...
Page 124: ...F 8 Appendix F Schematics OS 385...
Page 125: ...Schematics F 9 Appendix F OS 385...
Page 126: ...F 10 Appendix F Schematics OS 385...
Page 127: ...Schematics F 11 Appendix F OS 385...
Page 128: ...F 12 Appendix F Schematics OS 385...
Page 129: ...Schematics F 13 Appendix F OS 385...
Page 130: ...F 14 Appendix F Schematics OS 385...
Page 131: ...Schematics F 15 Appendix F OS 385...
Page 132: ...F 16 Appendix F Schematics OS 385...
Page 133: ...Schematics F 17 Appendix F OS 385...
Page 134: ...F 18 Appendix F Schematics OS 385...
Page 135: ...Schematics F 19 Appendix F OS 385...
Page 136: ...F 20 Appendix F Schematics OS 385...
Page 137: ...Schematics F 21 Appendix F OS 385...
Page 138: ...F 22 Appendix F Schematics OS 385...
Page 139: ...Schematics F 23 Appendix F OS 385...
Page 140: ...F 24 Appendix F Schematics OS 385...
Page 141: ...Schematics F 25 Appendix F OS 385...
Page 142: ...F 26 Operator Notes OS 385...
Page 143: ......
Page 144: ......