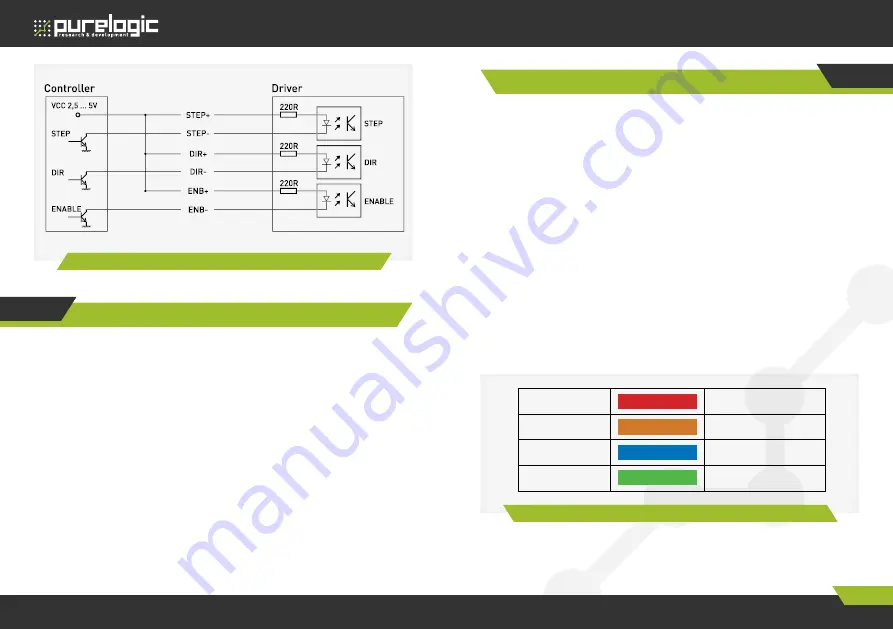
Edition from 28.08.2015
11
PLD86.
New generation stepper motor driver
www.purelogic.ru
8 (800) 555 63 74
06. Control Signal Connections to the driver
Fig. 4.
Purelogic R&D stepper motor connection to the driver
PLD86 driver is optimal for control of bipolar and unipolar stepper
motors Purelogic R&D series PL86.
Stepper motor connection to the driver is performed as it is shown in
fig. 5 (clips PH1.1[+A], PH1.2[-A] and PH2.1[+B], PH2.2[-B]).
The driver has protection against wrong stepper motor coil connection
and coils linked together / ‘+’ power supply.
Purelogic R&D stepper motor’s connection to the driver is performed
according to fig. 4.
Please note in case of changing phases PH1.x<>PH2.x, the motor
will start rotating in the opposite direction (inversion analogue of DIR
signal).
The length of wires leading to the stepper motor from the driver must
not exceed 10 meters. Longer wires can lead to driver’s work failures
(because of strong electromagnetic interference created during stepper
motor coil switching).
It is strongly recommended to interlace the stepper motor wires per
phase, then put this braid to the screened metal sheath. Sheathes and
stepper motor frame must be grounded.
PH1.1 [+А]
Red (RED)
PH1.2 [-А]
Orange (ORG)
PH2.1 [+B]
Blue (BLU)
PH2.2 [-B]
Green (GRN)
Max supply voltage driver option depends on the applied stepper motor
and desired max rotation speed. Optimal supply voltage calculation
for the stepper motor is carried out according to the formula U=32*v
(stepper motor phase inductance mH), but not more than 80V.
Supply current must be chosen 50...70% from the claimed stepper
motor coil current.
Working current setting is performed by trimming resistor WORK
CURRENT and DIP-switch SW4.
When there is no STEP signal for more than 1 sec, the driver goes to
AUTO-SLEEP mode and reduces the coil current to the value identified
by DIP-switch SW3 (according to the scheme on the driver case, fig.5).
This allows to reduce heating when the stepper motor is in standstill
and to reduce current consumption. Hold current setting must be
performed only when driver voltage is off.
FULL is for full current, HALF is for half current (for SW3, SW4).
POWER OFF DEVICE BEFORE MAKING ANY CONNECTIONS.
Fig. 2.
Differential input device
Stepper motor connection to the driver
08
07
Current and power option