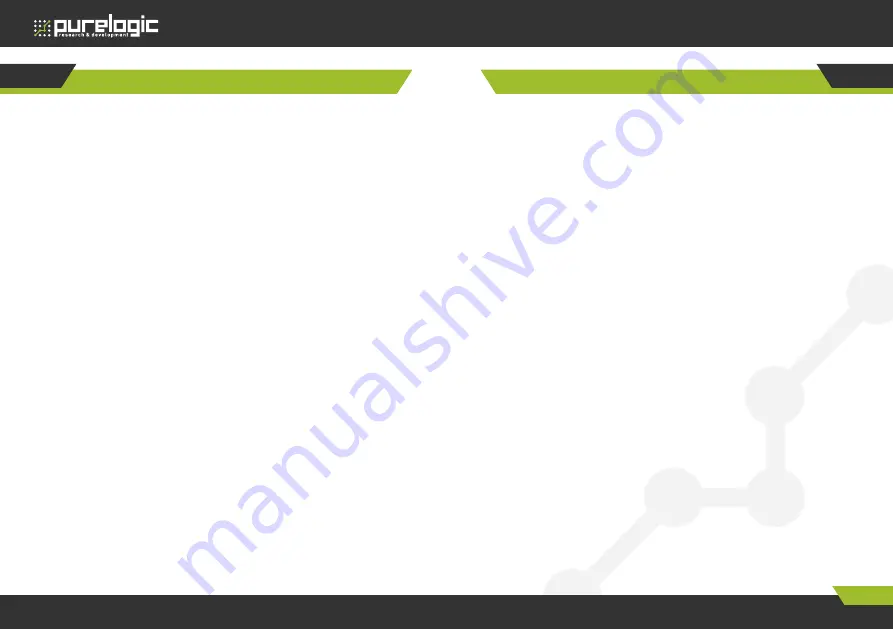
Edition from 28.08.2015
7
PLD86.
New generation stepper motor driver
www.purelogic.ru
8 (800) 555 63 74
06. Driver functional capabilities
The driver operates with standard signals STEP/DIR/ENABLE.
The signals are transmitted to differential optoisolated inputs.
Differential scheme is used to increase noise immunity and gives an
opportunity to connect the module to any driver controlling system
(controller). With STEP signal, STEP LED intensity changes.
The scheme of differential input device and connection method to the
controller with outputs ‘open collector’ type is shown in fig. 2. Control
signals connection is performed according to fig. 2.
Controlling signals connection to the module is carried out according to
the scheme which is depicted on driver’s case (fig. 5).
STEP signal characteristics
— working voltage 2.5V, 3.3V, 5V (you may
need extra current-limiting resistor connection), current consumption
up to 20mА, min signal duration is 2ms. The step is carried out on the
signal leading edge.
DIR signal characteristics
— working voltage 2.5V, 3.3V, 5V (you may
need extra current-limiting resistor connection), current consumption
up to 20mА, action time is 200 nsec before/after front edge STEP.
ENABLE signal characteristics
— working voltage 2.5V, 3.3V, 5V
(you may need extra current-limiting resistor connection), current
consumption up to 20mА, action time is 100 ms. Logic unit (voltage is
applied to the input) – stepper motor driver is off and coils are cut off
the current, zero – stepper motor driver is on and stepper motor coils
are supplied.
05
Driver functional capabilities
• Optoisolation of module control signals STEP/DIR/ENABLE.
• Expanded adjustment of working current of stepper motor phases
with divider.
• Stepper motor softstarter. After turning on the power or ENABLE
signal, current is increasing gradually in stepper motor coils. This
allows to exclude typical bump when turning stepper motor on.
• AUTO-SLEEP mode, driver after 1 sec standstill (lack of STEP signal)
automatically enters rotor hold mode (full/half operating current) for
heating reduction.
• Coil short-circuit module protection, wrong stepper motor connection
protection.
• Protection against back EMF effect.
• Polarity reversal power protection (the driver will not be switched on).
• Protection against overheating (temperature sensor).
• Inbuilt automatic compensator of normal speed stepper motor
resonance.
• Phase current adjustment for vibrations exclusion at low revs.
• Modifications scheme of phase current form with frequency increase
(morphing, transfer from microstep to step mode with with frequency
increase).
• Inbuilt dumper (back EMF compensation device from stepper motor).
• Convenient dismountable clip connectors to step motor, power source
and control signals.
• Alarm indication supplied by STEP/ENABLE frequency, inbuilt dumper
operation.
• Driver mounting on stepper motor case is available (PL86. Type).
• Possibility of cooling fan ( 50х50mm) mounting on driver’s radiator.
Cooling fan power performs via external power source. Cooling fan is
not included in the delivery set.
Control Signal Connections to the driver
06