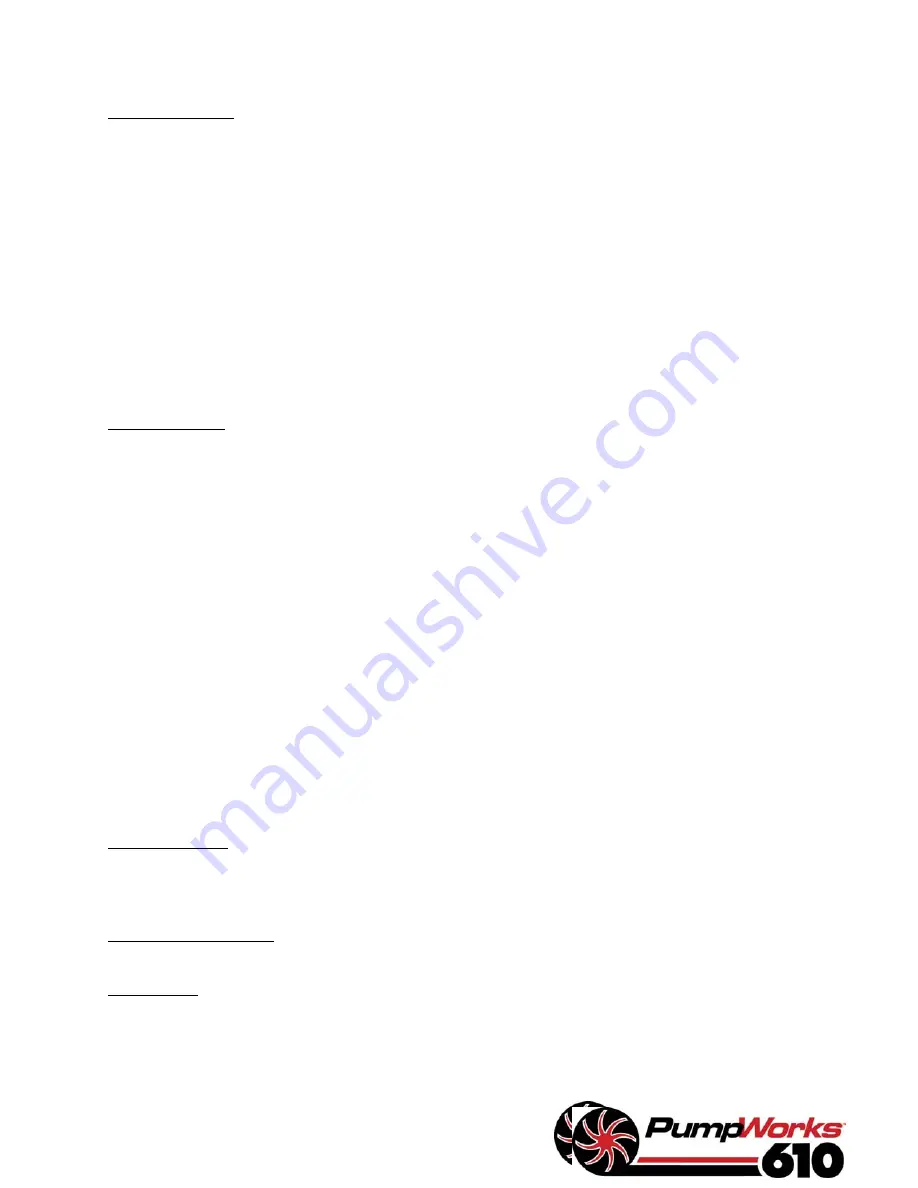
Page
3
of
28
Model: PWD Rev. B_12/2/2015
TABLE OF CONTENTS
INTRODUCTION
Company Details ........................................................................................................................................ 4
Declaration of Conformity ........................................................................................................................... 5
Scope ................. .......................................................................................................................................6
Description ................................................................................................................................................. 6
General ....................................................................................................................................................... 6
Safety ...................................................................................................................................................... 6-9
CE and ATEX marking and approvals ..................................................................................................... 10
Disclaimer................................................................................................................................................. 10
Copyright .................................................................................................................................................. 10
Design Performance ................................................................................................................................ 10
Duty Conditions ................................................................................................................................... 10-11
Specific Gravity ........................................................................................................................................ 11
Speed ....................................................................................................................................................... 11
NPSH ....................................................................................................................................................... 11
INSTALLATION
Receiving Inspection ................................................................................................................................ 11
Short Term Storage ............................................................................................................................. 11-12
Long Term Storage .................................................................................................................................. 12
Foundation ......................................................................................................................................... 12-1
3
Leveling .................................................................................................................................................... 13
Grouting .................................................................................................................................................... 13
Piping Recommendations ................................................................................................................... 13-14
Lifting ........................................................................................................................................................ 14
Pump Installation ................................................................................................................................. 14-15
Driver Installation ..................................................................................................................................... 15
Alignment ............................................................................................................................................ 15-16
Couplings ................................................................................................................................................. 16
Lubrication .......................................................................................................................................... 16-
18
Recommended Control Settings .............................................................................................................
19
Pre-Startup Procedures ..................................................................................................................... 19-2
0
Startup Procedures .................................................................................................................................. 20
Startup Inspection .................................................................................................................................... 20
Shutdown ................................................................................................................................................. 21
Extended Shutdown ................................................................................................................................. 21
MAINTENANCE
Preventative Maintenance ................................................................................................................... 21-22
Mechanical Seal / Bearing Housing Removal ..................................................................................... 22-26
Rotating Element Removal ................................................................................................................. 26-27
TROUBLESHOOTING
Troubleshooting .................................................................................................................................. 28-29
REVISIONS
Revisions .................................................................................................................................................. 29