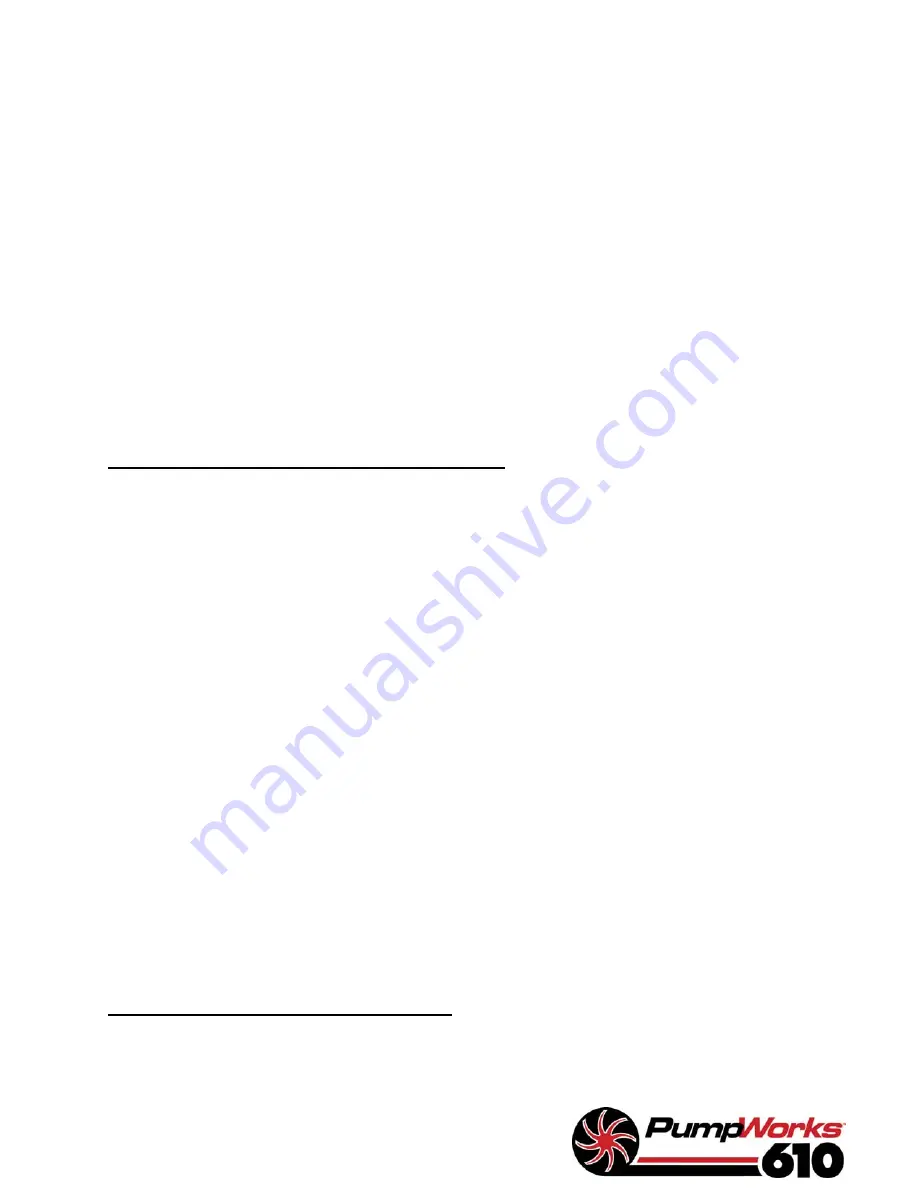
Model: PWD Rev. B_12/2/2015
4) Remove pump coupling hub. Normal
standard shaft extensions have a 1 1/4”
taper per foot on diameter taper. Loosen the
set screw in the nut face. Back the coupling
nut off a few rounds. A puller may be used
to put pressure on the coupling hub, and
with a soft or brass hammer, a mild bump on
the back shoulder should disengage the
taper fit. Be careful not to damage back fit
on gear shroud couplings.
5) Remove fan shroud and fan as applicable.
6) Remove
outboard
cover.
7) The oil slinger ring is accessible once the
cover is removed. Remove oil ring through
the outboard cover register bore. Inspect oil
ring to ensure round and no damage.
Replace as necessary.
8) Remove bolting on the inboard cover.
9) The housing can now be pulled off of the
bearings.
10) Bent “W” washer lock tab out of slot in the
bearing retaining nut. The bearing nut, lock
washer, oil ring carrier, and bearing can now
be removed.
11) Remove inboard cover.
12) The seal is now accessible. Remove and
replace per seal manufacturer’s instructions.
13) After installation of seal, reverse order of
assembly per above. Seal should be set
after reinstallation of the housing and
bearings. Manually oil bearings prior to
rotation. New bearing retaining nuts and “W”
lock washers should always be used during
re-installation.
14) Ensure all guards are installed prior to
operation.
15) After re-pressurization of the casing and
during startup of the unit, monitor seals for
leaks and take corrective actions if leaks
occur.
BALL / BALL BEARING HOUSING (OUTBOARD)
1) Follow all Lockout/Tag Out Procedures
prior to removal of guards and
maintenance of unit.
Ensure
ALL
electrical sources have
be de-energized and locked out.
Ensure suction, discharge, and
bypass valves have been closed
and secured.
Drain fluids from pump and bearing
housing that is to be removed. Use
proper precautions for hazardous or
flammable liquids. Remove constant
oiler globes. Refer to applicable
MSDS sheets as necessary.
2) Remove coupling guard, as necessary
for rotating shaft.
3) Remove RTD probes, as applicable.
4) Remove fan shroud and fan as
applicable.
5) Remove
outboard
cover.
6) The oil slinger ring is accessible once
the cover is removed. Remove oil ring
through the outboard cover register
bore. Inspect oil ring to ensure round
and no damage. Replace as necessary.
7) Remove bolting on the inboard cover.
8) The housing can now be pulled off of
the bearings.
9) Bent “W” washer lock tab out of slot in
the bearing retaining nut. The bearing
nut, lock washer, oil ring carrier,
bearings and shim can now be
removed.
Do not loose shim between
the thrust bearing and shaft shoulder!
This shim is used to center the rotating
assembly to the internal components.
Failure to re-install this shim could result
in severe damage.
10) Remove inboard cover.
11) The seal is now accessible. Remove
and replace per seal manufacturer’s
instructions.
12) After installation of seal, reverse order of
assembly per above. Seal should be set
after reinstallation of the housing and
bearings. Manually oil bearings prior to
rotation. New bearing retaining nuts and
“W” lock washers should always be
used during re-installation.
13) Ensure all guards are installed prior to
operation.
14) After re-pressurization of the casing and
during startup of the unit, monitor seals
for leaks and take corrective actions if
leaks occur.
SLEEVE BEARING HOUSING (INBOARD)
1) Follow all Lockout/Tag Out Procedures
prior to removal of guards and
maintenance of unit.
Ensure
ALL
electrical sources have
be de-energized and locked out.
Ensure suction, discharge, and
bypass valves have been closed
and secured.