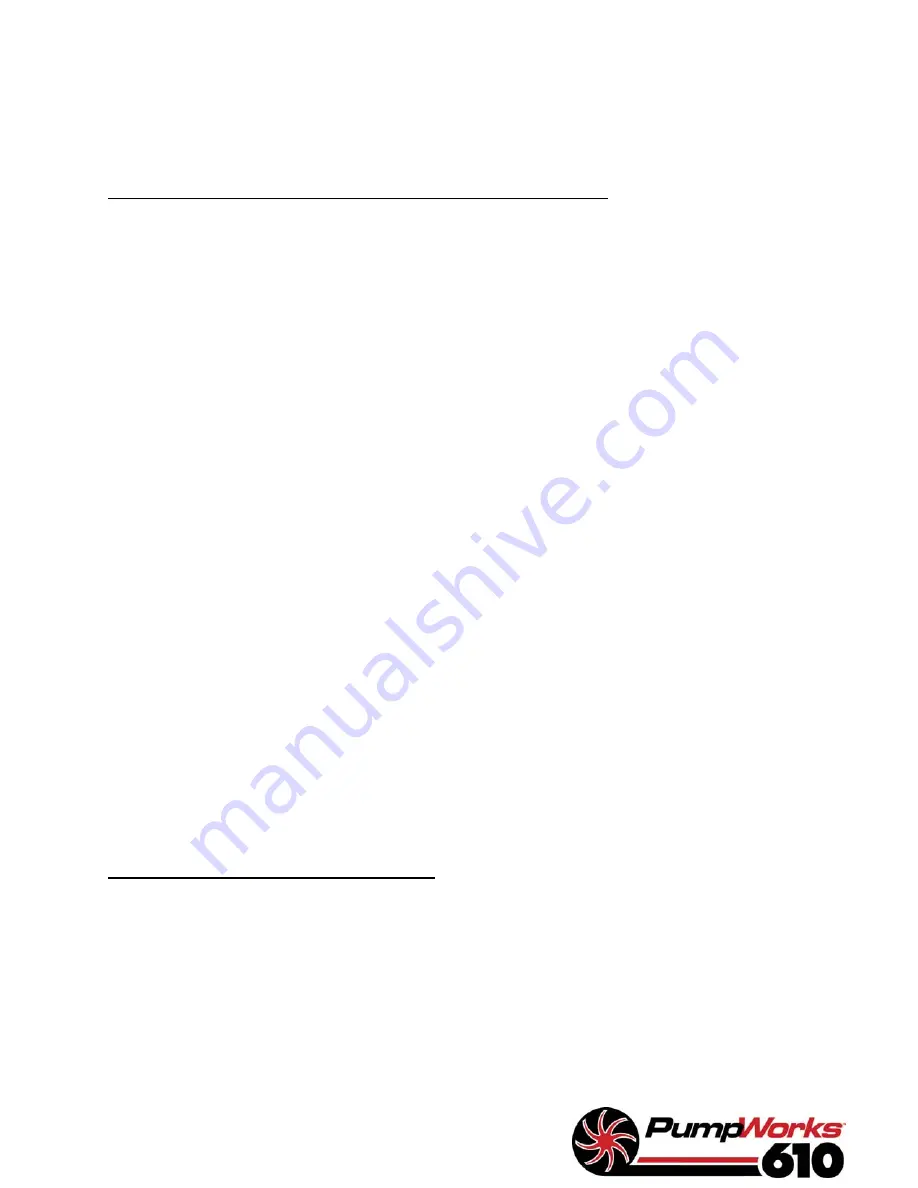
Model: PWD Rev. B_12/2/2015
L. After installation of seal, reverse order of
assembly per above. Seal should be set
after reinstallation of the housing and
bearing. Manually oil bearings prior to
rotation.
M. Ensure all guards are installed prior to
operation.
N. After re-pressurization of the casing and
during startup of the unit, monitor seals
for leaks and take corrective actions if
leaks occur.
SLEEVE – TILTING PAD BEARING HOUSING (OUTBOARD)
1) Follow all Lockout/Tag Out Procedures
prior to removal of guards and
maintenance of unit.
Ensure
ALL
electrical sources have
be de-energized and locked out.
Ensure suction, discharge, and
bypass valves have been closed
and secured.
Drain fluids from pump and bearing
housing that is to be removed. Use
proper precautions for hazardous or
flammable liquids. Remove constant
oiler globes. Refer to applicable
MSDS sheets as necessary.
2) Remove coupling guard, as necessary
for rotating shaft.
3) Remove RTD probes, as these protrude
into the bottom half of the bearing shell.
4) Disconnect and remove proximity
probes and vibration monitors as
necessary, or applicable.
5) Pull outboard bearing cover and main oil
pump. Check oil pump to ensure that it
turns freely and smoothly. Disassemble
and inspect if unit feels rough.
6) Remove bearing housing top half.
7) Disconnect drain and inlet lines as
applicable.
8) Remove screws in sleeve bearing top.
Pull top half of the bearing off. By lifting
up on the shaft, the lower half of the
bearing can be rolled out. Be extremely
careful not to damage sleeve bearing
journal, as this will adversely affect the
bearing life, and could result in damage
to pump internals.
9) Remove thrust bearing shoes and place
where they are not subject to damage.
Keep shoes in sets for inboard and
outboard positions. Inspect and replace
as necessary.
10) Back off set screws as necessary in
thrust bearing nut. Remove thrust
bearing retaining nut. Thrust bearing
nuts come off the direction the unit
turns. Pull thrust disc.
Do not loose shim
between the thrust disc and shaft
shoulder! This shim is used to center the
rotating assembly to the internal
components. Failure to re-install this
shim could result in severe damage.
11) Remove lower bottom half bearing
housing.
12) Remove the bearing isolator, chamber
ring, and oil rings from the shaft. The
seal is now accessible. Remove and
replace per seal manufacturer’s
instructions. Inspect oil rings to ensure
round and no damage. Replace as
necessary.
13) After installation of seal, reverse order of
assembly per above. Seal should be set
after reinstallation of the housing and
bearings. Manually oil bearings prior to
rotation.
14) Ensure all guards are installed prior to
operation.
15) After re-pressurization of the casing and
during startup of the unit, monitor seals
for leaks and take corrective actions if
leaks occur.
ROTATING ELEMENT REMOVAL
1) Pull bearing housing tops and bearings.
Refer to instructions in the “Bearing
Housing Removal” section above as
necessary. If split housings, the lower
half of the bearing housings can be left
in place if the mechanical seals are
pulled and re-installed with the rotating
element.
2) Remove the dowel pins in the casing top
half.
3) Loosen the mechanical seals set collar
and gland bolting. Separate the gland
from the seal chamber face. Be careful
not to damage the seal chamber face,
as this could cause seal leakage of the
seal gland gasket.
4) Remove all case nuts.
5) Set screws are located in the top to
separate the casing and case gasket.
6) Lift the casing top half by the cast
eyelets, being careful not to bind on the
case studs.
7) Lift the rotating element with nylon
straps on extreme ends. Care should be
taken not to allow strap slippage. See
Figure 8.