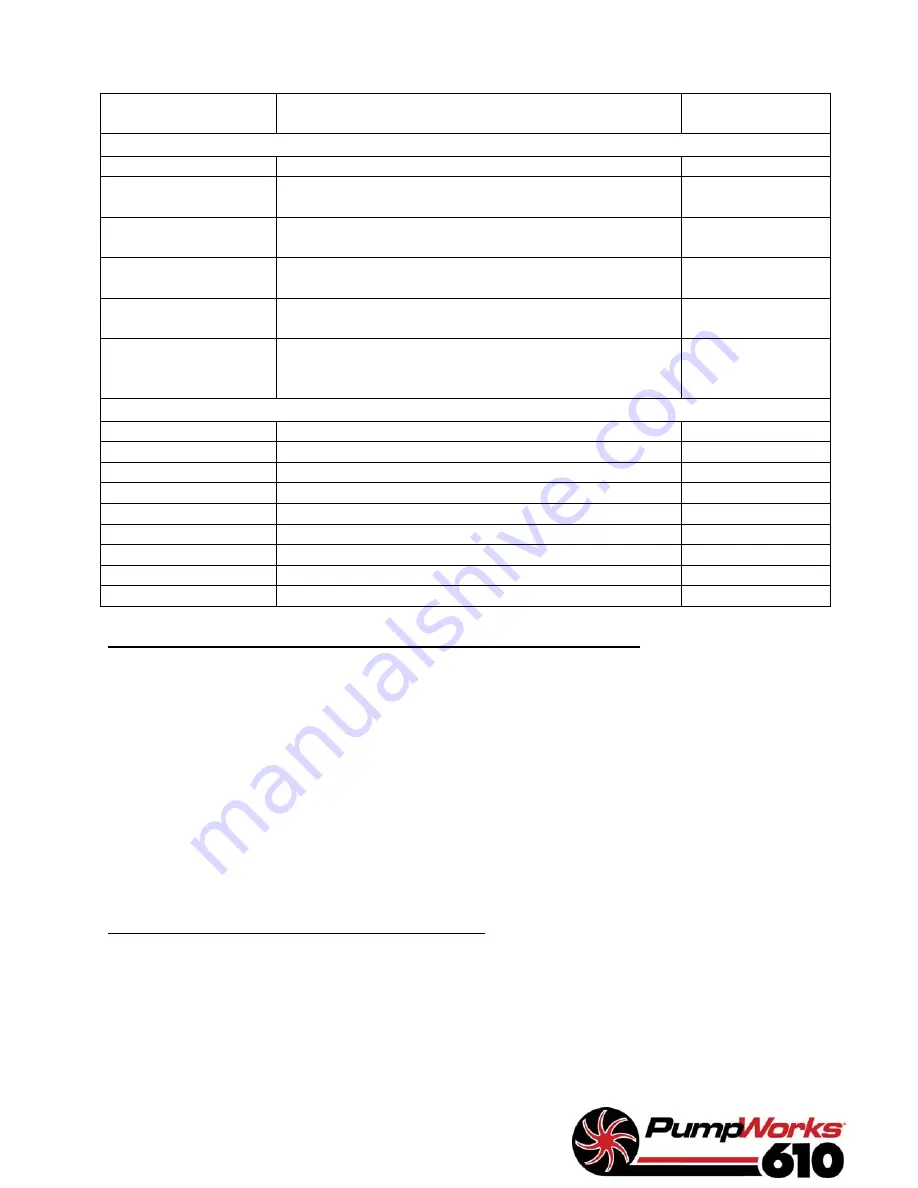
Model: PWD Rev. B_12/2/2015
Preventative
Maintenance
Description Frequency
Initial Startup & Commissioning
Oil System
Change Lube Oil
1
st
250 hours
Suction Strainer
Check pressure differential across suction strainer
Every 2 Hours for
1
st
Day
Mechanical Seal
Visually inspect
1
st
Hour After
Startup
Auxiliary Piping
Visually inspect
1
st
Hour After
Startup
Instrumentation
Check instruments for proper function and verify
calibration readings.
1
st
Hour After
Startup
Unit Monitoring
Monitor bearing temperature rise and stabilization. Ensure
no sudden temperature rises. Check vibration readings for
abnormalities.
1
st
8 Hours After
Startup
Normal Operations
Oil System
Change Lube Oil (Continuous Operation)
Every 2000 hours
Oil System
Change Lube Oil (Standby Operation)
Every 6 Months
Lube Oil Filters
Check pressure differential across filter.
Daily
Suction Strainer
Check pressure differential across suction strainer
Daily
Unit Monitoring
Monitor vibration, bearing and case temperatures
Daily
Mechanical Seal
Monitor for leaks
Daily
Auxiliary Piping
Visually inspect
Monthly
Cleanliness
Check for oil leakage and dust buildup
Monthly
Performance
Check pump performance & efficiency
Every 6 Months
Table 1
MECHANICAL SEAL / BEARING HOUSING REMOVAL
Packages manufactured by PumpWorks610
are made for replacement of the mechanical
seals, without disturbing the pump or driver. For
this purpose, packages are supplied by
PumpWorks610, and in compliance with API
610 specifications, with a spacer coupling to
allow clearance for seal removal
The following procedures are given as a
customer reference only, and do not necessarily
cover every step of removal for every
configuration of construction. It is the end users
responsibility to ensure that care is taken not to
damage components, fits, and finishes which
could cause leakage of the product, possible
failure of bearings, or of the entire unit.
Maintenance should be performed by
experienced and qualified personnel, and should
be performed in compliance with all safety
regulations and procedures.
PumpWorks610 maintenance personnel are
available for service, supervision, training, or
consultation.
Anytime bearing housing is
disturbed replace ball bearings.
Removal
instructions are as follows:
BALL / BALL BEARING HOUSING (INBOARD)
1) Follow all Lockout/Tag Out Procedures prior
to removal of guards and maintenance of
unit.
Ensure
ALL
electrical sources have
be de-energized and locked out.
Ensure suction, discharge, and
bypass valves have been closed
and secured.
Drain fluids from pump and bearing
housing that is to be removed. Use
proper precautions for hazardous or
flammable liquids. Remove constant
oiler globes. Refer to applicable
MSDS sheets as necessary.
2) Remove
coupling
guard.
3) Remove RTD probes, as applicable.