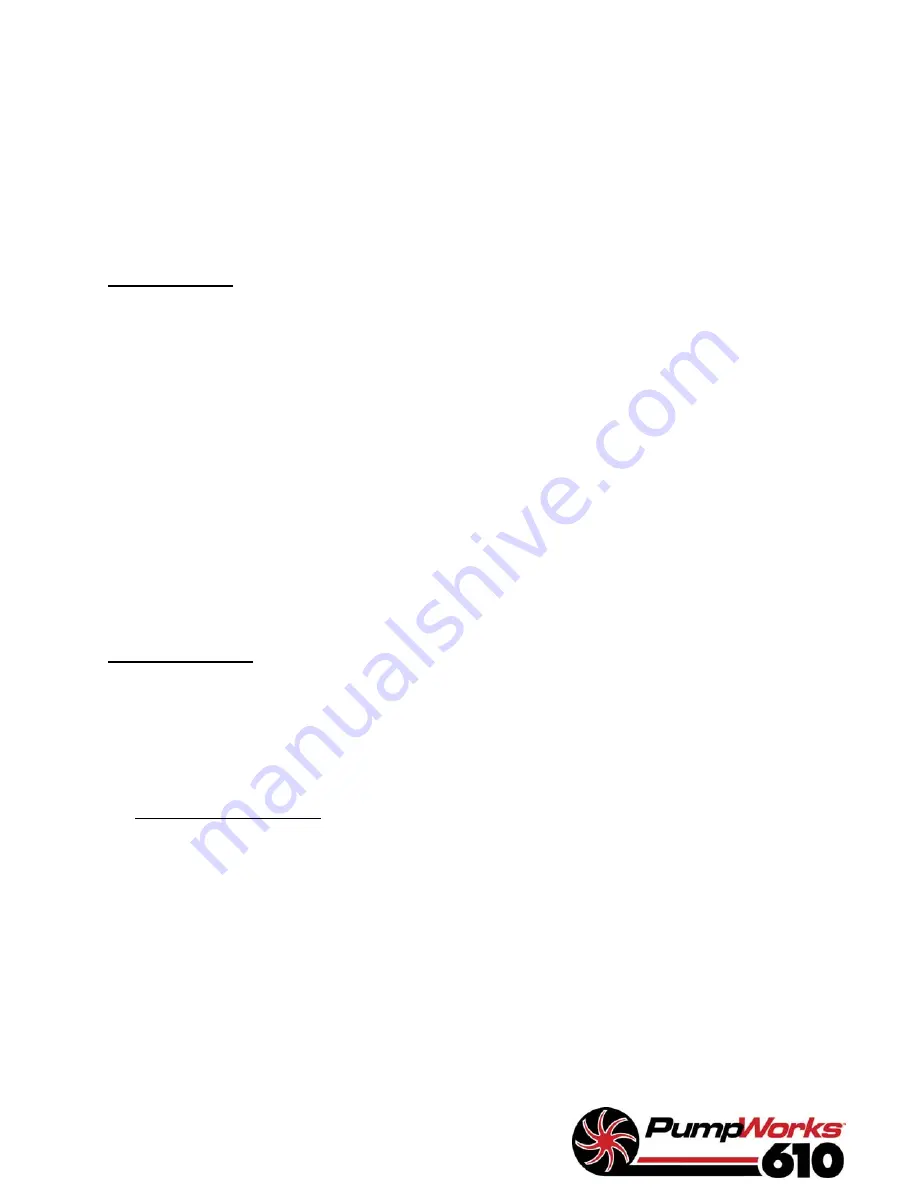
Model: PWD Rev. B_12/2/2015
A “Hot Alignment” should be performed
to verify proper alignment after unit has
reached and stabilized at normal operating
temperatures. Records of cold alignment
settings, and adjustments during hot
alignments should be kept to facilitate future
installations. Tighten all bolting, take new
readings and verify that the alignment values
repeat.
Note: Direct sunlight on the laser lens can
effect alignment readings, as well as
wear in gear tooth couplings.
Readings on gear couplings should be
made in one direction of rotation, to
eliminate backlash errors.
COUPLINGS
Each coupling type have their inherit
strengths and weaknesses. For that reason,
couplings should be selected on a basis of
operating conditions, thermal growth,
maintenance requirements, and operating
speed.
With the BB3 style pump, a coupling spacer
is necessary for the removal of the inboard
mechanical seal, without disturbing the pump or
driver. During seal replacement and normal
maintenance schedules, couplings should be
inspected for wear, disc warpage or cracking,
and signs of a poor fitting taper.
On taper fit shafts, fretting of the coupling fit
and wear of the shaft key is a sign of a poor
fitting coupling. When a shaft or coupling hub is
replaced new, the fit to the mating part should
be inspected to ensure a proper fit. This can be
done with high spot blue, or chalk. With high
spot blue, apply a thin layer in a line down the
length of the taper fit of the shaft or coupling
bore. Without the key in the shaft, ease the hub
on the taper fit and twist approximately 5° to 10°.
Pull the hub off and inspect the contact pattern
of the taper on the mating part. The contact
pattern should be reasonably uniform down the
length of the taper.
Improper fitting coupling can cause shaft
wear or breakage at the coupling fit. When
replacing a hub or shaft, ensure drive key has
clearance over the top of the key as to not
prevent hub makeup on the shaft taper fit.
LUBRICATION
Several methods of providing lubrication to
bearings are employed in pump lube systems.
The type of bearings used in the pump and
design specifications dictate which type of
system is used. The three primary lube systems
are:
Pressurized lube system: This system
involves an external lube oil pump with a
reservoir and filtering system. The oil is
circulated through the lube oil reservoir,
through a heat exchanger, then through the
filtering system, then to the bearing
housings. From the bearing housings, the oil
drains back into the reservoir. This type of
system will be fitted with controls to monitor
pressures and temperature and shut the unit
down in the event of a failure in the system.
Oil rings will be utilized in most cases on the
sleeve bearings for coast down of the pump.
Tilting pad bearings will always be pressure
fed. See Figure 3 for typical housing
arrangement.
This system has an auxiliary lube
pump to supply oil to the pump until the
pump is up and running. After the pump is
up and running the main lube oil pump,
which is in most cases attached to the pump
shaft, provides the lube oil supply and the
auxiliary lube pump shuts down.
Prior to starting, the auxiliary lube oil
reservoir should be filled to the specified
level with oil. This level will be indicated by a
sight gauge on the tank itself. This system
should be started and ran for at least one
hour prior to startup of the pump. If the
pump is in a cold climate the heater should
be turned on several hours prior to start up
in order to raise the temperature of the oil to
an acceptable level. Monitor the filter
differential pressure during this period, and if
there is more than a 2 PSI increase in this
pressure, the system should be run until this
pressure does not change for at least one
hour. At this time the active filter should be
changed out if there was a pressure
increase.
Once the lube system is purged per the
above, the pump can be started, (see start
up procedures).