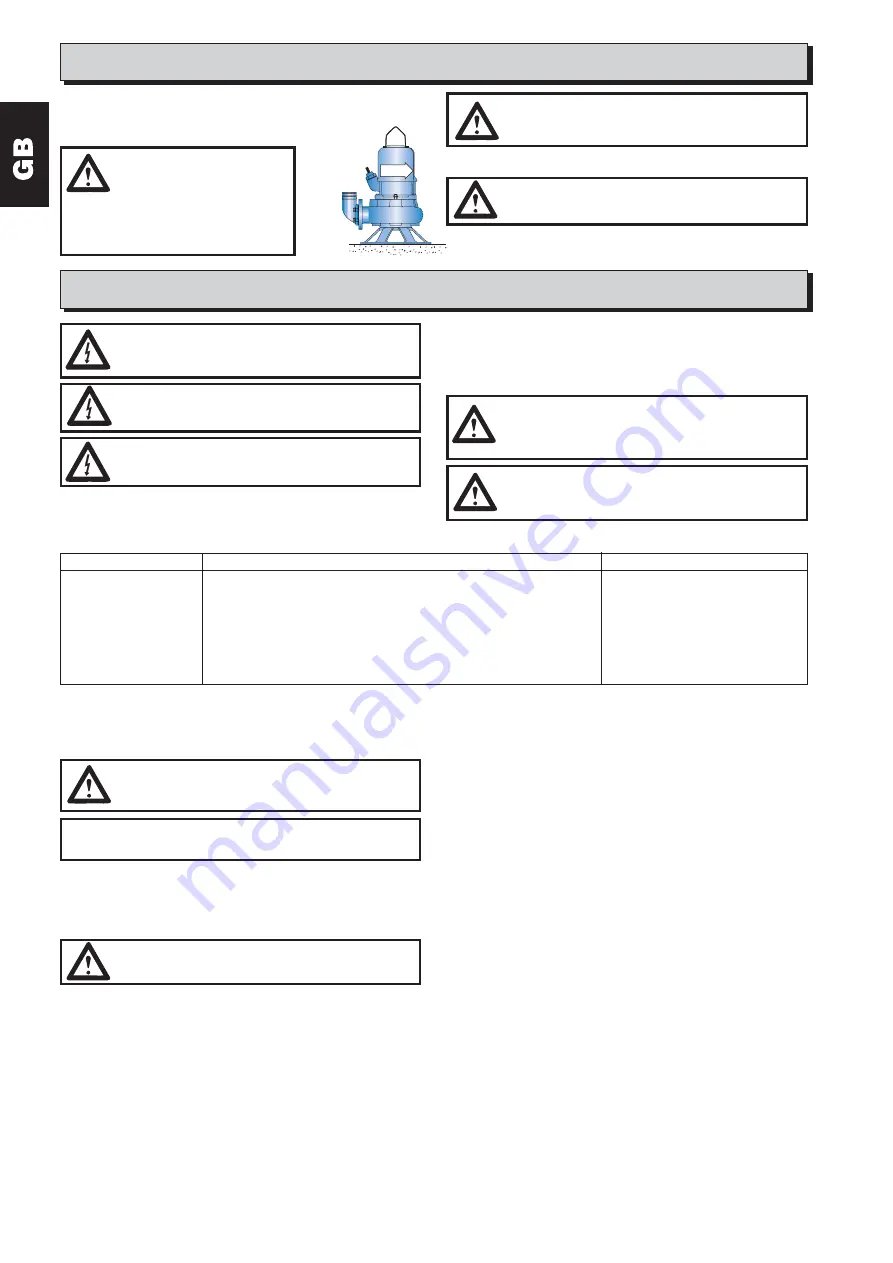
8
Inspection
Pump section
Inspection
Action in the event of a fault
Cables
Check that the sheath is not damaged. Check that the cables are not kinked or nipped.
Fit a new cable. Correct the fault
Visible parts
Check that all parts are in good condition, and that bolts
Replace worn parts. Tighten
and nuts are securely tightened.
any loose bolts and nuts.
Impeller/wear ring*
Check that the parts are not worn to such an extent that the pump performance is
1. Adjust the wear ring.
affected.
2. Fit a new impeller/wear ring.
Shaft seal
Check that the oil is clean and is not mixed with water. See under ”Changing the oil”.
In the event of slight leakage, change the oil.
In the event of major leakage, fit a new seal.
Hoses, pipes and valves
Check that the equipment does not leak or is otherwise damaged.
Adjust or replace defective equipment.
*= N.B. All pumps are not equipped with a wear ring.
Starting
jerk
Before starting:
Check the direction of rotation of the pump (see
figure). At the instant of starting, the pump will jerk
anti-clockwise when viewed from above.
Changing the oil
Change of oil is done the same way on cooled and uncooled pumps.
Open oilscrews on both sides (as picture 1 on page 19).
Lean pump or only motor on the side, drain the oil into a clean receptacle.
Examine the oil.
Operation
CAUTION!
Under certain operating conditions, the pump tempera-
ture may be high.
If the direction of rotation is incorrect, transpose two phases. See under the
heading ”Electrical connections”.
CAUTION!
The starting jerk may be violent. Don’t hold the pump
handle when checking the direction of rotation. Make sure
that the pump is firmly supported and cannot rotate.
WARNING!
Never insert your hand or any
other object into the inlet opening
on the underside of the pump
casing when the pump is connected to the
power supply.
Before inspecting the pump casing, check
that the pump has been isolated from the
power supply and cannot be energized.
Service and maintenance
CAUTION!
Before any work is started, check that the pump is isolated
from the power supply and cannot be energized.
The figures within brackets are item numbers and are shown on the sectional
drawings on the fold-out pages at the end of the manual.
CAUTION!
When the pump or motor section has been laid on its side,
always secure it with wedges from both sides to prevent it
from rolling away.
CAUTION!
Before undertaking any service work, make sure that the
pump is thoroughly clean, and bear in mind the importance
of observing good personal hygiene.
Follow your local safety instructions.
Regular inspection and preventive maintenance will ensure more reliable
operation. The pump should be inspected every six months, or more often if the
operating conditions are difficult. The cable should be checked more frequently.
For a complete overhaul of the pump, please get in touch with an authorized
Pumpex workshop or your Pumpex dealer.
Lay the motor section on its side. Secure the motor section with wedges on
both sides. Check that it is securely in place and cannot roll away.
Hold the impeller to prevent it from rotating and release the impeller bolt
(see picture 3 on page 19). Remove the washer. If the impeller is stuck, tap
it gently with a lead mallet.
If the impeller is still stuck, two crowbars can be used to prise under the
impeller hub (see picture 4 on page 19).
Remove the impeller and remove the key from the shaft.
To fit
Make sure that the shaft end is clean and free from burrs. Use fine emery
cloth to rub down any damage. Fit the key. Oil the shaft end and impeller hub.
Check that the key has been correctly fitted into the keyway in the shaft. Fit
the impeller, washer and impeller bolt. Use a screwdriver or similar tool to
Fill with new oil (see table on page 18). Use White Oil with a viscosity of 20
cSt, such as BP Enerpar M002 or equivalent. Always fit a new seal washers
on the oil screws. Assemble in the reverse order.
Changing the impeller.
To remove
Remove the motor section. Drain the oil.
prevent the impeller from rotating, and tighten the bolt. Raise the motor
section. Fit the motor section to the volute. Tighten the latch bolts.
Check the clearance between the impeller and wear ring.
Adjust if necessary. See under ”Adjusting the wear ring”.
Changing the seal unit
To remove
On cooled versions cooling liquid must be drained out before changing seal
cartridge. Drain cooling liquid by removing lower plug (below cooling pipe,
see picture 2 on page 19), and remove top filling screw.
The seal cartridge can be removed as one unit without the need for special
tools. Replace the cartridge by an overhauled unit.
Drain the oil and remove the impeller. See under ”Changing the oil” and
”Changing the impeller”.
Remove the four screws retaining the seal cartridge (see picture 5 on page
19).
To press out the cartridge, screw two M6 screws (at least 40 mm long) into
the tapped holes and tighten them (see picture 6 on page 19).
To fit
Note! Dry and wet installed pumps have different seal units.
Oil the shaft and the three O-rings on the seal cartridge (two on the outside
of the seal housing and one inside the seal sleeve).
Fit the seal cartridge to the shaft. Press it carefully into place.
N.B. Don’t use a tool to apply blows to the seal cartridge.
Secure the seal cartridge by means of the four screws. Fit the impeller and
fill with oil (+ cooling liquid). See under ”Changing the oil” and ”Changing the
impeller”.
Adjusting the wear ring.
A pump with a channel impeller is equipped with an adjustable wear ring
mounted in the volute. After a period of operation or after the pump has
been dismantled, the clearance between the impeller and the wear ring
should be checked.
Lay the pump on its side. Secure the pump in position by means of wedges
on both sides. Check that the pump is firmly retained and cannot roll away.
Use a feeler gauge to measure the clearance between the wear ring and the
impeller. The clearance must not exceed 0.7 mm.
If the clearance must be adjusted, release the Allen screws in the wear ring.
Tap the wear ring lightly with a hammer or a plastic mallet until the clearance is
correct. Tighten the set screws, check that the impeller can be rotated by hand.
CAUTION!
Dismantling and repair of explosion proof motors may only
be carried out by approved personnel in specially approved
work shops.
CAUTION!
Parts must be replaced by genuine spares, including
screws, to insure correct strength in Flameproof
enclosures.
CAUTION!
In the event of inward leakage, the oil housing may be
pressurized. When removing the oil plug, hold a piece of
cloth over it to prevent oil from splashing.
NOTE!
Old oil should be entrusted to an oil disposal company in
accordance with local regulations.
CAUTION!
A worn impeller often has sharp edges. Take care not to cut
yourself on them.