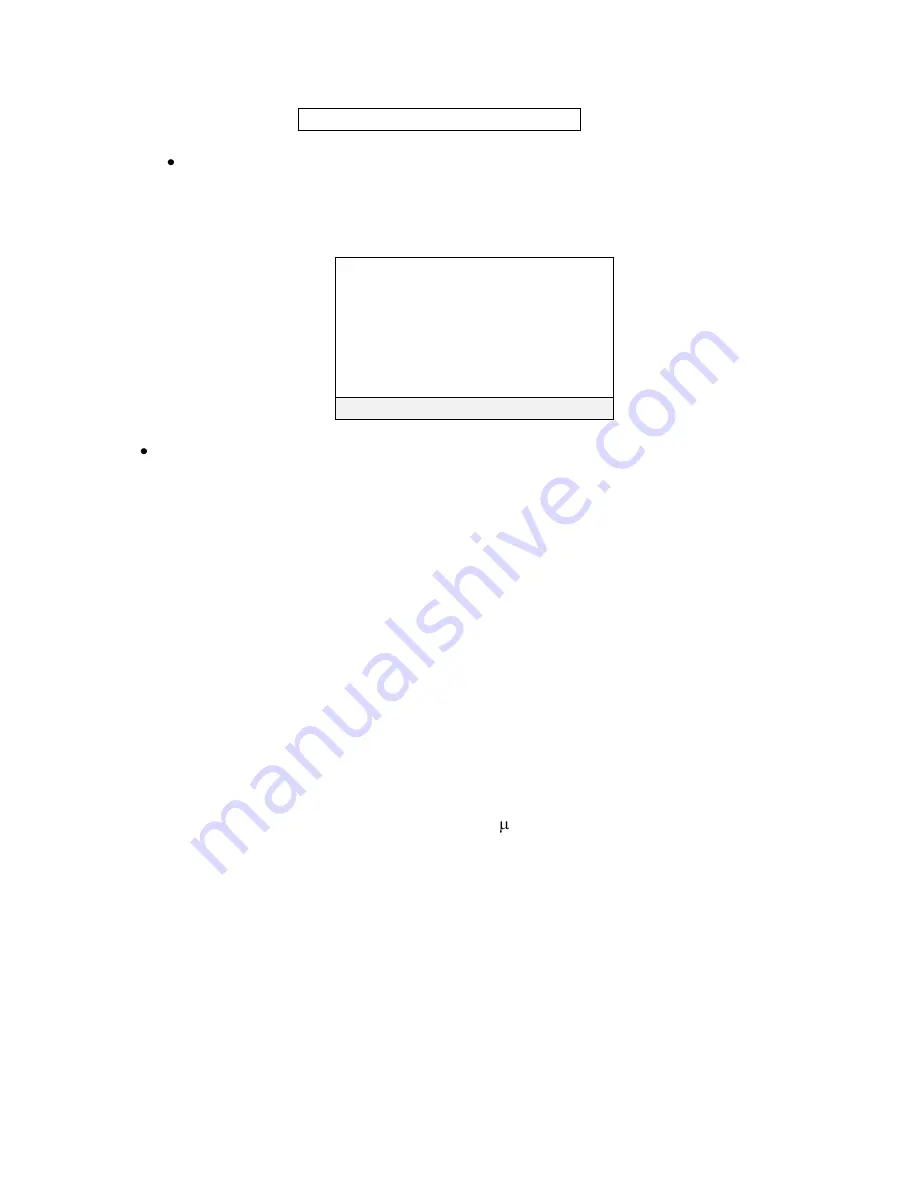
34
6 00 00:00
If there are no scheduled feeds, select the first schedule and press ‖
ENT
‖. If you are
editing the schedule, select the sc
hedule that you want to edit and press ‖
ENT
‖.
Below is an example screen for programming a chemical feed.
Before programming a chemical feed,
you need to configure Relay 2, 3, or 4 to be a Calendar Timer relay.
To program the schedule use the keypad to enter the values in the above screen. Press
‖
ENT
‖ to move to the next item.
NOTE: ALL TIMES ARE IN HOURS AND MINUTES
RELAY
is which relay you want to program (you must configure a relay to be a
Calendar Timer relay first). Use the arrow keys to select the available
relays. Only relays that have been configured as Calendar Timer
relays will appear.
CYCLE DAY
or
DAY
is the day you wish to actuate the Calendar Timer relay.
START TIME
is the time you want to start the Calendar Timer sequence. This start
time uses the 24 hour clock or military time.
06:00:00
is 6 a.m.
18:00:00
is 6 p.m.
COND SETPOINT
is a pre-bleed setpoint. This would typically be lower than the normal
conductivity setpoint. Because the bleed valve may be disabled
during a scheduled feed, a pre-bleed will help prevent a build up of
tower conductivity. 0 S will disable this feature.
BLOW DURATION
if the COND SETPOINT is not met within this time, the blowdown
will stop and the Calendar Timer relay will be actuated.
If
conductivity is disabled, this is the amount of time the controller
will blow down during the pre-bleed sequence.
Inputting 0:00 will
disable this feature. Pulsafeeder recommends that some time be
entered if pre-bleed is used.
FEED DURATION
is the amount of time the Calendar Timer relay will be on.
LOCKOUT TIME
after the feed duration is completed, an additional lockout time for
RLY 1, 2, 3,
and
4
relays can be programmed. The lockout time
RELAY (ARROWS) : NONE
CYCLE DAY
: 0
START TIME : 00:00
COND SETPOINT : 0
BLOW DURATION : 00:00
FEED DURATION
: 00:00
LOCKOUT TIME
: 00:00
<UP><DOWN>ENT: ACCEPT
Summary of Contents for PULSAblue 3300 Series
Page 5: ...4 FIGURE A ...
Page 52: ...51 24 Drawings ...
Page 53: ...52 ...
Page 54: ...53 ...
Page 55: ...54 Prewired ...
Page 56: ...55 Prewired ...
Page 57: ...56 ...
Page 58: ...57 ...
Page 59: ...58 ...
Page 60: ...59 ...