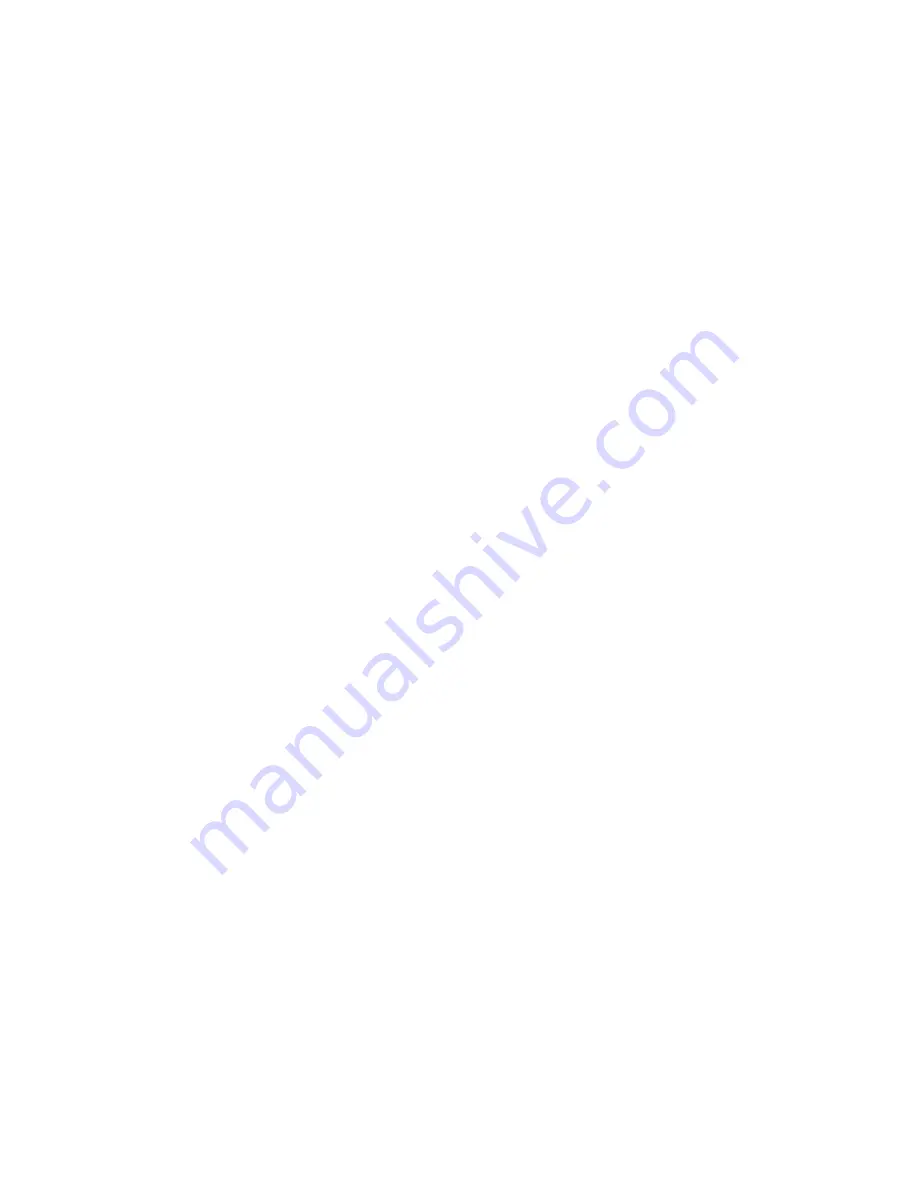
5
9. Do not spring piping, either suction or
discharge when mating up to the pump. Use
supports or hangers at intervals as required.
When necessary, provide for thermal
expansion and contraction so no strain is
placed upon the pump.
10. Check all bolts and nuts for tightness. Correct
any conditions which could cause destructive
vibration or leakage.
11. Where required, provide proper system for
containment can recirculation.
12. If start-up screens are used, be sure they do
not clog and starve suction. Start-up screens
should be removed prior to placing system into
regular operation.
13. If flexible suction lines are used, be sure their
selection and installation will prevent wall
collapse and thus a starved suction condition.
14. When taking suction from a tank or vessel,
avoid entry of sludge, solids, etc. into suction
line by placing suction line inlet above
maximum expected level of solids.
15. Discharge line should be fitted with properly
sized pressure relief valve to protect both pump
and discharge system. Pressure relief valve
outlet should be piped back to the supply tank.
16. When a by-pass system is used to control flow
from the pump, the bypassed fluid should be
piped back to the suction vessel to prevent
heat build-up due to recirculation. If it is
absolutely necessary to pipe by-pass back to
the pump suction line, the point of entry should
be at least
1
0 pipe diameters away from the
suction inlet. Provision for cooling should be
made in the event of excessive heat buildup
through fluid recirculation.
17. Where pumped fluids may solidify, crystallize,
precipitate etc., provision should be made to
thoroughly flush pump and piping prior to
periods of shutdown. Pay particular attention to
proper flushing and draining of the magnetic
coupling area because this area will not self
drain. There is a drain plug in the front housing
for access to this area.
OPERATION
1. Prior to operation, make sure all suction piping is
air tight and clean. Check that electrical service to
motor agrees with name plate ratings. Jog to
check rotation and for signs of binding. To check
rotation, observe the motor fan. Rewire motor if
necessary.
2.
Isochem Gear pumps are designed to handle
clear fluids at viscosities up to
500,000
SSU
(100,000
CPS).
No gear pump should be run dry. Damage
to wear surfaces will result.
Pumping fluids containing abrasives
should be avoided as accelerated pump
wear will result.
3.
It is recommended that pumps with metallic drive
and idler gears not be run with fluids having a
viscosity less than
500
SSU (
1 00
CPS) or at
speeds greater than
1450
RPM.
4. The pump will self-prime if fluid is supplied at the
pump inlet. If foot valves are used, the valve
should be of the flapper type and sized to
minimize friction loss.
5. If the pump is to operate near the boiling point of
the fluid being pumped, a recirculation loop can be
set up between the drain connection in the front
housing and the suction with provisions for flow
control in the recirculation loop.
6. Do not operate the pump against a closed
discharge. Doing so will cause the magnetic drive
to decouple. High temperatures will then be
created which can cause the fluid to boil or
damage the magnet assemblies. If decoupling
occurs, stop the motor and restart after the
obstruction has been cleared. As a safety
precaution a pressure relief valve by-pass system
is highly recommended. Ideally the pressure
relief valve is set for a low pressure for start-up.
7. Start pump with discharge and suction valves
open and check for proper operation. Excessive
noise or vibration is an indication of harmful
cavitation which is due to insufficient NPSH (Net
Positive Suction Head).
Summary of Contents for Isochem GM12 Series
Page 2: ......
Page 16: ...15...
Page 17: ...16...
Page 18: ...17...
Page 19: ...18...
Page 20: ...19...
Page 21: ...20...
Page 22: ...21...
Page 23: ...22...
Page 24: ...23...
Page 25: ...24...
Page 26: ...25...
Page 27: ...26...
Page 28: ...27...
Page 29: ...28...
Page 30: ...29...
Page 31: ...30...
Page 32: ...31...
Page 33: ...32...
Page 34: ...33...
Page 35: ...34...
Page 36: ...35...
Page 37: ...36...
Page 38: ...37...
Page 40: ...39...
Page 41: ...40...
Page 42: ...41...
Page 43: ...42...
Page 44: ...43...
Page 45: ...44...
Page 46: ...45...
Page 47: ...46...
Page 48: ...47...
Page 49: ...48...
Page 50: ...49...
Page 51: ...50...
Page 52: ...51...
Page 53: ...52...
Page 54: ...53...
Page 55: ...54...
Page 56: ...55...
Page 57: ...56...
Page 58: ...57...
Page 59: ...58...
Page 60: ...59...
Page 61: ...60...
Page 62: ...61...
Page 63: ...62...
Page 64: ...63...
Page 65: ...64...
Page 66: ...65...
Page 67: ...66...
Page 68: ...67...
Page 69: ...68...
Page 70: ...69...
Page 71: ...70...
Page 72: ...71...
Page 73: ...72...
Page 74: ...73...
Page 75: ...74...
Page 76: ...75...
Page 77: ...76...
Page 78: ...77...
Page 79: ...78...
Page 80: ...79...
Page 81: ...80...
Page 82: ...81...
Page 83: ...82...
Page 84: ...83...
Page 85: ...84...
Page 86: ...85...
Page 87: ...86...
Page 88: ...87...
Page 89: ...88...
Page 90: ...89...
Page 91: ...90...
Page 92: ...91...
Page 93: ...92...
Page 94: ...93...
Page 95: ...94...
Page 96: ...95...
Page 97: ...96...
Page 98: ...97...
Page 99: ...98...
Page 100: ...99...
Page 101: ...100...
Page 102: ...101...
Page 103: ...102...
Page 104: ...103...
Page 105: ...104...
Page 106: ...105...
Page 107: ...106...